Does it make sense to install rigid foam insulation on only one wall?

Hi all,
Background:
I live in an area where temperature’s varies from -40 to +38 deg Celsius. I have a home built in the 1940s and I have a question about increasing the insulation in exterior walls. Note, my foundation footprint is a rectangle.
At construction, loose coconut fibre was placed between the studs, and no vapour barrier was installed. I’ve done some research and have found that about 4″ of loose cocounut fibre equates to about an R3.
The sheeting is made up of 1×6 tongue and groove wood planks, covered with builder’s felt. The original exterior wall seems to be some sort of parging that was applied to a wire mesh, about 1″ thick.
Most of my home has since been covered with aluminum siding (no insulation added between siding and original exterior). That said, my attached garage (not insulated, no foundation) wall is still original.
I’d like to know if it would be worthwhile to install XPS (or EPS) rigid board on the exterior side of this wall to improve the household’s overall insulation.
My concern is that without a thermal break between the attached original walls/siding, that I wouldn’t really realize any benefit because the cold/heat will still transfer through the attached walls to a large degree.
Any thoughts?
Thank you.
GBA Detail Library
A collection of one thousand construction details organized by climate and house part
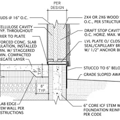
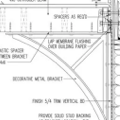
Replies
Robin,
I'm not sure that I understand your plan. Do want to install rigid foam on the interior or the exterior of your wall? Which wall -- the common wall facing the attached garage, or a different wall?
The short answer to your question is, adding rigid foam insulation to one of your walls will definitely reduce the rate of heat flow through that wall. Of course, it won't have the same effect as performing the work on all four walls. A simple energy modeling program could be use to quantify the resulting energy savings.
Thanks for replying to my post.
To answer your question, it was the exterior of the common wall I was looking
at installing rigid foam on.
I was worried that since the masonry is such a good conductor, that simply
installing foam on top while leaving the edges exposed would just be a waste
(sort of like installing fibreglass batts but leaving the edges exposed to
wind)
I've seen it done at other places, but I'm certainly far from being an
expert.... I've learnt that just because someone else has done it, doesn't
make it a good idea!
It sounds to me like you're saying in general that it's probably worth doing?
Any thoughts on XPS vs EPS? I was thinking XPS due to higher R value's and
because it could be considered a vapour barrier, but then thought that if I
ever upgrade the insulation on the inside, that I'll end up with vapour
barrier issues if I add more than a third of the overall R Value on the inside wall.
Any thoughts on what is most common practice and what makes the most sense in my situation?
Robin,
I'm not sure what you mean by "masonry." Do you mean the stucco cladding?
If you are installing rigid foam over stucco cladding, just be sure to extend the rigid foam so that (as much as possible) it covers all the stucco. The perimeter of the rigid foam should be sealed with caulk or canned spray foam, and the seams should be sealed with a compatible tape, caulk, or canned foam.
EPS is more environmentally friendly than XPS, and polyiso is even better. If you want more R-value, just buy thicker foam, or put on more than one layer.
The garage side of the foam should be protected with a layer of 5/8-inch drywall for fire protection.
The vapor permeance of the foam layer is irrelevant; what matters is the total R-value, which must be high enough to keep your sheathing above the dew point. More information here: Calculating the Minimum Thickness of Rigid Foam Sheathing.
Thanks Martin, I was talking about stucco cladding.
As for the Minimum thickness calculations relating to dew point, I know that there is no shortage of "experts" out there, but I found one resource that explains concisely that in addition to total R-Value, an important factor is the ratio of R-Value inside the wall and outside the wall in order to control condensation within the studs when no vapour barrier is present.
Here is a link to the article: http://www.buildingscience.com/documents/digests/bsd-controlling-cold-weather-condensation-using-insulation/
Just something to think about. Thanks again for your advice.
Robin,
You'll notice that my article -- the one I linked to -- also considers the ratio between the R-value of the insulation between the studs and the R-value of the foam insulation outside the sheathing. That's why the tables in my article call for thicker foam on 2x6 walls than on 2x4 walls.
In your case, the coconut fiber insulation has a very low R-value. That moves you in the direction of less risk, not more risk, since the ineffective coconut fibers keep your sheathing warmer than (more effective) fiberglass would.