Energy Efficiency Benefits of Zip-R Sheathing

We are working with an architect to design a practical and cost-effective ‘energy-smart’ located Fairfax County, VA (outside Washington, DC). I am not an architect, engineer, or building scientist, so trying to decide on a practical, energy efficient, above-code (tight envelope and higher assembly R values, but not NZER or Passive), durable, cost-effective wall assembly has proven harder than expected. The architect (along with my HERS rater and independent HVAC designer) are pushing me to use Zip R3 as the exterior sheathing, but when I talk with most custom builders in my market, they look at me like I am from Mars and/or immediately double the total construction budget!
I can get into more detail of the wall ‘sandwich’ (inside out – 1/2 gyp, 2×6 24″ OC, blown cellulose plus 1″ CCSF, Zip R3, rain screen, hardie plank) but at this point all I am really trying to find out is whether the energy efficiency experts consider adding Zip R3 (with its’s measly 1/2″ of foam) in my CZ is worth its “thermal bridging, air barrier, vapor barrier” bang for it’s higher buck before capitulating to the builder’s ‘go-to’ (and higher profit) solution of using OSB sheathing wrapped in a WRB.
Don’t get me started on trying to find residential builders and framing subs willing to use 24″ OC framing, 2-stud corners and other advanced framing techniques.
And, speaking of water vapor, has anyone experienced condensation issues (winter or summer) issues when combining hardie plank with Zip R3 sheathing in CZ 4. trapping water vapor between the that
GBA Detail Library
A collection of one thousand construction details organized by climate and house part
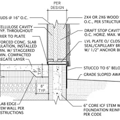
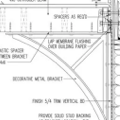
Replies
You do not have to use ZIP-R in Zones 1-4 (except for Marine 4). If you cannot find a builder or framer who is comfortable using the product, you could install standard ZIP, plywood, or OSB. If you decide to eliminate the R-3 product, make sure your architect and rater account for this change.
On your second question, you do want to use furring to create a rain screen (gap) behind the siding. See this article for details: https://www.greenbuildingadvisor.com/blogs/dept/musings/all-about-rainscreens
Agree with Steve. but to be honest I would think any builder worth his salt could install ZIP-R (R3). It's not rocket science for godsake. Also you won't get condensation on the interior side of the foam.
I'm also disappointed in the reaction you've been getting from custom homebuilders. Unfortunately it's SOP for them to double the price as a means of discouraging you from sheathing a house they way they want*.
*The builder may be getting OSB and housewrap incredibly cheap of possibly receive some sort of kickback from the supplier which he would of course lose by going with ZIP System.
Kickback? Or more likely they are used to going into their local lumberyard, finding OSB on the racks rather than ordering Zip-R, moving unused sheets from site to site, ordering their doors and windows a certain depth, keeping the same sheathing nails in their guns.
None of theses are compelling reasons not to use insulated sheathing. But the economics of building supply prices really doesn't make a very good case for kickbacks.
@Malcolm How about "rebate" does that sound better? ;) Maybe I was being a bit harsh. I am jaded after all as I hope to never, ever, ever, ever have to work with a builder. I have zero trust in them or their subs. If I ever have to sell my current home, I'm going to live the life of a renter.
John,
The reasons for the intransigence of builders to adopt new methods or materials is conservatism. Most just want to build, not innovate. Neither do they want to lose their shirts.
Fair enough, you don't trust them. It is a bit hard to hear myself described that way.
To say the homebuilders generally get kickbacks is an unfounded, uneducated and offensive statement. FYI, I’m not a Builder now, but I was 20 years ago. That is not to say that occasionally a shady and dishonest builder doesn’t exist, but that happens in every industry. I’ve been working over 30+ years in this industry, designing for 3 or 4 dozen of builders in 13 states, and I can’t tell you of a single case I would call a Builder known for receiving kickbacks.
On the merits of the post, and based on my experience of designing high-performing and Zero Energy Homes only, I can say the Zip-R and Zip panels are good products with even better tapes. Having said that, I have a problem with REAL installation on the field, where tapes are not installed per manuf. Instructions, thus having the OSB on the outside of the wall assembly, has a higher tendency for moisture problems, being the only moisture barrier.
Another suggestion is to use TAPED regular Plwd/OSB and TAPED Rigid Foam, with staggered seams, and installed in opposite directional runs (horizontal plwd and vertical foam). FOR LESS PRICE THAN THE ZIP-R PANEL. You still have the tape installation quality issue, but you cut dramatically the chance of moisture penetration AND the foam is on the outside of the wall assembly, which if taped with approved tape, it become a WRB. We go a step above and install HouseWrap on top of the foam to protected from the elements, since in our market it may take forever to get a mason or sider nowadays.
@Armondo. I was thinking rebate. As in using product from X-manufacturer because we get a discount over a certain amount but don't pass the savings onto the client.
@Malcolm,
I understand not wanting to innovate, but one has to question the idea behind "doubling of the price" as stated by the OP, who's working with a custom builder no less. My impression from the tone of the OP is that the builder has no interest in entertaining the idea of doing something different let alone taking a serious look at what the client is proposing. Of course materials costs differ because we are comparing nailbase to OSB + housewrap w/out exterior foam. I would think that labor costs would be about a wash between both approaches.
Edit: Btw..neither of you should take anything I say personally. I'm a bona fide curmudgeon. It's genetic.
John,
Quoting a high price for changes or substitutions is a pretty common practice among some builders. Sometimes motivated by inertia, sometimes because the change affects a lot more than the client realizes, both in actual building and also in the administrative side of the project.
No offence taken. I have to admit to being a bit disingenuous about how your remarks affected me. My friends regularly describe me in much worse terms :)
Last fall it was Zip offering a rebate of $400 for the first home a contractor installed Zip on.
Walta
First, I want to thank all of you for taking the time to comment and your spirited discussion.
Second, as the "OP" and owner/payer, I never intended to question the integrity of most custom home builders. I fully realize I will never find total transparency between cost of production/OH/profit and price regardless what I am buying including construction or a new car. That said, I continue my search for a custom home builder who will 'trust' me as much as I am expected to trust (but rarely verify) him/her.
My real 'energy' or 'green' question about specifying/using Zip R sheathing is CZ 4 is whether or not Zip R's (or Zip) higher first-cost compared to other more traditional (and perhaps less risky) materials and assemblies (i.e., OSB and WRP) is justified if my energy efficiency objective is to use Zip R solely to 'eliminate' thermal bridging. Or, am I playing a fool's game, as thermal bridging can never be totally eliminated, only marginally reduced, and the marginal ROI in my CZ isn't worth it?
Or, more to the point, is eliminating or reducing thermal bridging in CZ 4 really worth the dollars and cents invested upfront?
My other 'big' question is what is the actual SF cost difference (preferably in Northern Virginia/DC area) between constructing a typically AGW using OSB and WRB compared to a Zip or Zip R . Does anyone have recent unit cost or assembly cost market data they'd like to share? Again, most of the custom builders (acting more like CM or CM at risk firms) tell me a 4x8 Zip R3 panel will cost 3 times as much as a 4x8 OSB panel.
Hi! I am in a similar situation as you were when you posted this. The only difference is we are in CZ 2. Could you please share what you have found out? I imagine by now you are already enjoying this home you were posting about
I would not be surprised if ZIP-R cost three times as much as OSB, but I don't know that you can secure reliable costing information by posting on GBA. After you find a builder, I suggest you ask him/her to price this part of the build both ways. (That is, with ZIP-R or OSB plus tape, WRB, and rigid foam.) You can create a reliable assembly either ways as long as it is properly installed.
PS. Here is another way to address thermal bridging: http://www.finehomebuilding.com/2014/11/26/breaking-the-thermal-bridge
> Last fall it was Zip offering a rebate of $400 for the first home a contractor installed Zip on.
What's the standard on things like this when materials add to the price? The $400 is pocketed by the builder? With or without telling the owner? I've seen the latter.
Is there an "all supplementary benefits will be disclosed and the penalty for not..." contract clause that makes sense?
Here is a deep dive into the Zip-R system that might help you decide: Working With Zip System R-Sheathing.