Does anyone have thoughts on this wall section in regard to avoiding moisture problems and drying to the interior & exterior?

I am an architect in Boston preparing to build a home for my family on a marshfront site in Scituate MA (Zone 5 and 110MPH winds due to coastal proximity). Energy conservation is a key goal for the project. Originally I was planning an R48 double stud wall but circumstances have changed and I am now planning a single 2×6 stud wall with cellulose cavity insulation and rigid exterior insulation – total wall R value is about R38. The thinking on vapor / air / moisture barriers and retarders has gotten so complicated in recent years. I’ve read dozens of articles including those on GBA and I think I have a general appreciation for it at this point but worry that specification of the wrong material in one layer could cause significant problems. In days of old a layer of poly on the inside was standard (I actually think it still happens a lot). If I understand the science correctly the goal today is to allow a slight migration of vapor through that interior layer incase the wall ever needs to dry toward the inside. I believe that in Zone 5 a class 3VR, which includes certain paints is acceptable but I don’t really feel secure counting on paint to assure my wall performance, so a Class 2 Vapor retarder such as certainty MemBrain seem to be a wiser choice – if you think otherwise feel free to comment / offer your experience / advice. In the previous double stud wall version the VR layer could be on the backside of the inner stud layer allowing wiring and box installation to not complicate the VR layer. Encasing outlet boxes and such in the vapor retarder layer in a single stud wall seems tricky but necessary – if you think otherwise feel free to comment / offer your experience / advice.
Again, if I understand the science correctly, the outside of the stud wall requires an air barrier that will also allow vapor to migrate out of the wall while keeping liquid water from entering. as noted I am planning to incorporate 3″ or 4″ of rigid foam insulation on the outer face of the wall. In theory I believe I could put the air barrier outside the rigid or even allow the rigid insulation to be the air barrier as its perm rating is pretty low when joints are taped. BUT, here is one of my big concerns: I imagine the plane where the plywood sheathing and insulation meet (which is about 60% of the way across the R value of the wall) might be a common place for condensation to develop. To help with this I propose a layer of building wrap between the plywood sheathing and insulation; the wrap should be a drainable layer type (one of the krinkly surface products like tyvek drain wrap or one with bumps for example). However, I am concerned whether or not the drainage feature will work if the condensation takes place on the plywood side of the building wrap. Is my concern justified or not?Tyvek and similar products seem to fit this bill well and lots of helpful videos and articles help describe joint sealing, integration with flashing, etc. Another concern is whether or not the drainage layer, though incredibly thin will serve as an air leak between layers and actually carry heat away from the wall / reduce the overall R value of the wall by eliminating some of the insulting opportunities from the rigid insulation.
I have attached a sketch of the wall. Feel free to comment and share your experience. I am usually not this perplexed by building science but it just seems like there are so many variables now and the final result is always nasty if errors are made. Please feel free to comment / offer your experience / advice. I look forward to it. Thanks.
GBA Detail Library
A collection of one thousand construction details organized by climate and house part
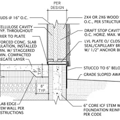
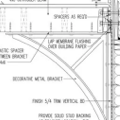
Replies
Here is what I think: this wall will dry to the inside and will accept water vapor with no issue. But I think you don't need the MemBrain vapor retarder. I think Sheetrock and latex paint is what you want. You don't want anything slowing down drying from that enclosure to the inside. Martin, Dana and others will correct me if I am wrong. I love the "Drainwrap up against the sheathing. One thing I might add is another layer of less expensive (I.e. "House brand" or Tyvek) OVER the foam, especially given the coastal climate. Just an added measure of insurance for a few hundred dollars more. But I have a question about your windows and doors- Are the INNIES or OUTTIES? Because the WRB needs to tie in with them, with at the Drainwrap (if innies) or at the outer foam (if they're outties.)
Sean,
The basic principle is as follows: you need to make your rigid foam layer thick enough to keep your wall sheathing above the dew point during the winter. As long as you do this -- and of course, as long as you pay attention to airtightness when the wall is being built -- you won't get any condensation at the sheathing level.
This type of wall is routinely built. It is a robust wall. When tested against other types of walls, the sheathing on this type of wall stays dryer than the sheathing on any other type of wall. This type of wall is designed to dry to the interior, so you can't install any interior polyethylene. The use of MemBrain is unnecessary.
All of these principles are explained in this article: Calculating the Minimum Thickness of Rigid Foam Sheathing.
Sean,
The Tyvek Drain-wrap between your exterior foam and sheathing isn't necessary and will do more harm than good. As Martin said , there should be no condensation on the sheathing if it is kept warm enough by the foam. However, for the Drain-wrap to work in the way you intend it, it would have to be open at the bottom to allow somewhere for the condensate to go. If it's open it also will allow air movement and defeat the whole point of having exterior foam. Without the drain wrap the wall is very resilient.
Thank you for the three really well thought out answers. This is much appreciated. I have learned a great deal in this process but tend to go for the belt and suspenders approach when in doubt - hense the wrinkle wrap and Membrain.
The average dew point in January in Boston is 19º and average temp for the same is 24º. In August those figures are 56º and 80º. Under both sets of circumstances it does seem that the foam (60+% of the R value from inside to outside) will be above the dew point so it seems you are all right that condensation should not occur at the boundary of sheathing and foam. That's good news.
As for the latex paint instead of Membrain: Most residential work in this are is skim coated blue board. The skim coat layer is plaster NOT drywall compound. I can't find a number on the web but I assume plaster has a similar or slightly lower perm than GWB. Perhaps this detail will enhance to the characteristics of the latex paint and create a more uniform perm rating across the wall.
BTW, the windows will be outies.
Thoughts? Thanks.
I want to rewind on this to Malcolm. Malcolm, you are saying that no house wrap is needed? I disagree. I am surprised, because I believe there needs to be a drainage plain to integrate the window flashing with. Drainwrap is a perfect solution here because it provide a draining surface for condensation and rain to run off of. I wish we had other opinion on this.
Joe,
Sorry if I was unclear, a WRB is certainly needed. What I'm not sure of the value of is using Drain-wrap to create a drainage plane behind the insulation. If either bulk water or condensate accumulates on the drain wrap, where is it designed to go? If this inner-cavity is open either at the bottom, or some other way, then the outer insulation will lose its effectiveness.
I'm certainly open to other opinions on this.
Drainwrap is simply another version of Tyvek house wrap that has crinkles to help shed water that gets past the foam drained as easily as possible. See video: http://www.dupont.com/products-and-services/construction-materials/building-envelope-systems/videos/install-drainwrap-under-rigid-foam-board.html.
Thanks Joe, I've seen Drain-wrap, but I still don't understand where in this assembly it is "shedding" or "draining" the water to. What does creating this thin drainage plane accomplish that having regular tyvek instead wouldn't?
Usually Drainwrap or similar proprietary rain screen products like Homeslicker and others, are placed behind the cladding, so that either the water can dry through it if the cladding is permeable, or drain behind it if it isn't. 4" of foam isn't going to allow any drying to the exterior so the only alternative is for any water to drain to the bottom of the a wall assembly. But unless that assembly is sealed at the bottom, you will have air moving behind the insulation. Maybe I'm over-thinking this, but I can't see the benefit of the second drainage plane - especially in a wall that already has one.
So Malcolm you would just use regular tyvek house wrap and skip the Drainwrap? I think the Drainwrap would give superior performance at shedding the water between it and the foam if water were to get behind the foam particularly of you were doing innie windows. I think, one can tape it at bottom, or leave it open. The video illustrates that. If you don't use a wrap, your plywood or OSB would not have much protection.
Malcolm and Joe,
This issue is addressed by Joe Lstiburek in his article, "Mind the Gap, Eh."
Here's what Joe Lstiburek says: you don't need a gap between the OSB and the exterior rigid foam unless you are installing vapor-impermeable insulation (something like closed-cell spray foam) between the studs.
Here's what he says about the loss of R-value when you include the gap: “But won’t the tiny gap cause a loss of thermal performance of the foam sheathing? Yes. How much? About 5 percent of the thermal performance of the foam sheathing (not the entire wall assembly) with the 1/8-inch gap, less with a smaller gap. With 'crinkly' stuff you loose next to nothing.”
The stack-up is fine, from a dew point control perspective but the labeled R23 cellulose must be from trees grown on Mars, since it would need to average R4.2/inch instead of the more typical R3.6-R3.7.
On the foam-over 3" polyiso would have roughly the same performance as 3" XPS or 4" EPS, but would be both greener and more fire-safe than polystyrene, and it's dead-easy to air-seal reliably with foil tapes. During the coldest hours of the coldest days it's performance would be less than 3" XPS, but averaged over the season it would be comparable from an energy-use point of view. If you want to beat that performance, bump it to 4", which is still a very buildable thickness.
With that much exterior foam you neither need nor want a class-II vapor retarder on the interior. MemBrain might make it easier to make the interior air-tight, but it's vapor retardency is irrelevant in this stackup.
You can't use highly vapor retardent interior finishes with this stackup, since even with EPS as the foam the capacity for drying to the exterior is very limited. That means no foil or vinyl wallpaper. Oil paints may be OK in thin coats, but latex/acrylic would be preferred.
The vapor permeance ofplaster on blueboard is extremely high, more than an order of magnitude higher than latex paint, and not really worth measuring or thinking about.
The discussion above is terrific and much appreciated. I feel like a dummy compared to you guys! I have been practicing architecture for more than 30 years but I have not been in the residential side of things for a long time and so much has changed in those years. Thanks for the input and patience. Unfortunately the more advice I get the more questions I have.
I've reread the referenced articles, checked out the IRC table as mentioned, and relistened to a couple pod casts (Martin was the guest on one!). Coupled with all of your comments its been quite helpful. As I rethink my wall assembly, I am still getting stuck on a couple items though.
Starting from the inside out I think I will modify my wall to be one of the following options:
Option 1. Skim coated Blueboard, 2x6 studs with cavity filled with dense cellulose (the table I was using listed the r value at 4.2 but your comments inspired further research. 3.9 seems to be a more accepted value. Thoughts or article that help me decide between spray applied and dry applied will be appreciated), plywood, 3-4" of insulation (EPS, XPS, or ISO to be determined), building wrap, 1x4 pt furring strips, siding. This assembly should dry well to the inside.
Option 2: Same as option one but a flash coat of closed cell spray foam would be applied to the inside face of the plywood sheathing. Two matters confuse me with this option:
First, if the plywood gets wet (This is a marsh site not far from the coastal velocity zone. No matter how well you flash, tape, and seal water infiltration is not out of the question in a hurricane. ) the fact that it is sandwiched between two layer of low perm foam might mean that it can't dry in either direction. Obviously that sounds problematic.
Second is the related language of the code "a. Spray foam with a minimum density of 2 lb/ft3 applied to the interior cavity side of OSB, plywood, fiberboard, insulating sheathing or gypsum is deemed to meet the insulating sheathing requirement where the spray foam R-value meets or exceeds the specified insulating sheathing R-value."
What "insulated sheathing R Value" am I trying to meet or exceed? Is it supposed to equal the R of the a. plywood or b. the R15 of the foam insulation (3-4") I am stacking on the outside, or c. the R7.5 called for in table N1102.5.1? I think the answer is c (which equals approx. 1.5") but the language is confusing to me.
I will appreciate your thoughts and again thank you for your patience.
Sean,
1. Furring strips don't need to be pressure-treated. A rainscreen gap stays extraordinarily dry. In fact, the point of the rainscreen gap (if designed well, with vents at the bottom and the top) is to encourage fast drying. Your furring strips will have a low moisture content for most hours of the year.
2. Cellulose insulation isn't going to achieve more than R-3.7 per inch. There's a lot of exaggerating going on in the insulation world.
3. For more information on cellulose options, see this article: How to Install Cellulose Insulation.
4. If you want to install exterior rigid foam -- and I think it's a good move if you do -- you certainly don't want to install any closed-cell spray foam on the interior side of the sheathing. The sheathing needs to dry to the interior. Again, if these details are new to you, I suggest that you read Calculating the Minimum Thickness of Rigid Foam Sheathing.
5. As far as I know, the code reference to "the insulating sheathing requirement" is a reference to the requirements listed in Table N1102.5.1 (in the 2007 IRC), or Table R601.3.1 in the 2009 IRC, or in Table R702.7.1 in the 2012 IRC.
Thanks Martin. Great info. Much appreciated.
Sean, I would skip the idea of spray foam and save it for your mudsill area assuming there is a basement. That is a great application for spray foam. I would put the Drainwrap over the OSB and "scituate" your windows (pardon the pun) as INNIES and tie into the Drainwrap with flashing for your WRB. I wouldn't hesitate to take a few hundred dollars of plain old house wrap from Loews or where ever to put OVER The foam as well for double insurance in this wind-driven rainy coastal environment. But considering the harsh environment with hurricane like conditions, I would definitely build innie windows using the Drainwrap over the OSB as your weatherized layer. You can tape the 3" of polyiso foam as well and use these measures to keep her dry. Remember that you need 1x4 furring and six inch screws, too. But as to cavity insulation I would be looking for dense packed cellulose installers rather than doing the wet-applied stuff or the loose pack. And IF your client really, really wants spray foam then fill the cavity with an open cell, water-blown product. All of the above I learned from the experts here.
Thanks Joe. This has been a great learning experience. Happy Holidays all.