Do My External Insulated Walls Even Need Sheathing?

I am building a heated garage to be built in Minnesota – climate zone 6. I have designed the walls as follows (in to out): gypsum wallboard -> 2×6 stud wall 16″ o.c. w/ cellulose insulated wall cavities -> 7/16″ OSB sheathing -> WRB -> 1 1/2″ XPS foam panels (R7.5) -> 3/8″ strapping to create rain screen (w/ venting above & below) -> cement fiberboard cladding above & stone veneer cladding below.
Having read a great deal about the risks of “injury” to the sheathing if temp at sheathing below dewpoint (e.g. https://www.greenbuildingadvisor.com/blogs/dept/musings/calculating-minimum-thickness-rigid-foam-sheathing), I have a simple (stupid?) question….
…does one even need to put wood sheathing on?
While I could consider increasing my XPS layer to 2″ thick as advised here on GBA and leave the OSB sheathing, that extra 1/2 inch of wall thickness would entail multiple additional design changes that I would prefer not to deal with. So, maybe I could ditch the sheathing and increase the XPS to 2″ and never have to worry about the sheathing getting cold?
…or should I reverse the XPS and OSB? Thereby bringing the OSB into a space where it can dry – adjacent to the rain screen.?
Of course, James Hardie does not approve installation of their product over greater than 1.5″ of XPS (see http://www.jameshardie.com/pdf/USTB-Applying-James-Hardie-Siding-over-Advanced-Framing-or-Continuous-Insulation.pdf), so really, I have issues no matter what, it would seem.
Thanks for the insights! Great resource, for the DIY builder/nerd, by the way.
K.S. Jeffery
GBA Detail Library
A collection of one thousand construction details organized by climate and house part
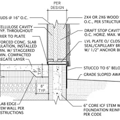
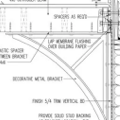
Replies
Kent,
I'm unsure of what type of siding you plan to install. You mention "cement fiberboard cladding [presumably, fiber-cement] above & stone veneer cladding below," but your title refers to EIFS (synthetic stucco). So -- what type of siding are you planning on using?
Q. "Does one even need to put wood sheathing on?"
A. No, as long as you have a plan for bracing your wall, and as long as your local building inspector approves of your wall-bracing plan. For more information, see 4 Options for Shear Bracing Foam-Sheathed Walls.
Q. "James Hardie does not approve installation of their product over greater than 1.5 inch of XPS."
A. That's only true if you leave out the vertical furring strips. If you include vertical furring strips, James Hardie has no problem with thicker foam. For more information, see Fastening Furring Strips to a Foam-Sheathed Wall and How to Install Rigid Foam Sheathing.
Yes... sorry. I took EIFS to generically mean "External Insulated Foam Structure", but I see it refers to a specific stucco wall structure. Edited title to correct, as I am using fiber cement board and stone veneer cladding. No stucco.
So, I'd like to carry in this discussion further - for primarily academic reasons as the inspector has ultimate authority over what I finally do build, according to the 2007 IRC Supplement: Section N1102.5 Moisture Control.
It would seem that, in keeping with Mr. Lstiburek’s understandably crude simplifications, further assumptions can be made that might make me feel my wall as designed is satisfactory. First, as a garage, I am designing to an internal temp of between 50F and 60F. While this lowers the temperature at the OSB sheathing surface slightly, it notably lowers the delta-T used to calculate the necessary external to internal insulation ratio.
Furthermore, I am not intending to regulate the internal humidity, and thus would expect it to be on the order of 25% or less when the air is very cold in January. As a consequence, vapor diffusion pressure is less than might be expected for a humidity controlled home in winter.
Looking at Table 1 in John Straube's excellent article on BuildingScience.com, BSD-163: Controlling Cold-Weather Condensation Using Insulation, I should be OK with any exterior to interior insulation ration of 1:3 or better. (This assumes conditioned space relative humidity of 25% when outdoor temp is 15F, or rel. humidity of 20% at T(out) of 5F... not unreasonable assumptions for a garage, I feel)
Thus, exterior R7.5 for XPS (ignore R1.3 for OSB on exterior - extra margin of safety), and interior R 17.7 (R0.45 for wallboard plus R17.3 for fiber) give ratio of 0.42. That is, I could accept an RH of 5% greater at given outdoor temp than I assumed.
So, shouldn't I feel pretty confident building my walls as described, acknowledging this is a garage with different design parameters? Of course, as mentioned, I understand that any arguments I might make supporting my design is moot if the inspector holds rigidly to N1102.5 requirements for R11.25 exterior insulation for 2x6 wall in Zone 6.
Thanks!
Kent,
I presume you will be heating the garage, which is why you want the walls to be insulated.
As long as your garage is kept cooler and dryer than the typical house, you are correct that your risk of sheathing problems is reduced or eliminated.
However, if conditions change in the future -- that is, if you or a future resident decides to raise the temperature of the garage or to convert it to finished space, your calculations will, of course, no longer hold.
Martin -
So, I'm brainstorming methods of meeting code without altering the thickness of my wall. If I decided to try to go ahead and do things "by-the-book", I'm assuming I get credit the 7/16" OSB sheathing in my total exterior insulation R value? That is, R10 for 2" XPS + R0.5 for the OSB?
This still leaves me short R0.75, but what if I applied a thin layer of closed cell spray foam, say, 1/2 inch for ~ R3. It would seem I would then realize added benefits of moving the condensate (sorptive) plane internally, decreasing the internal R ever so slightly, appreciably increasing the external R, and providing superb air sealing to boot.
Is there anything wrong with my thinking? Or this scenario? (Besides cost, I mean!) After all, if I am understanding pertinent wall construction issues correctly, my wall is designed to dry both internally and externally, with the division at the ccSPF coated OSB, right? And the goal is to position this dividing line at a location where the temp rarely if ever drops below the dewpoint.
Kent,
Q. "I'm assuming I get credit the 7/16-inch OSB sheathing in my total exterior insulation R value? That is, R-10 for 2" XPS + R-0.5 for the OSB?"
A. I think you are assuming wrong. See IECC 402.1.2: "Insulation material used in layers, such as framing cavity insulation and insulating sheathing, shall be summed to compute the component R-value. ... Computed R-values shall not include an R-value for other building materials or air films."
However, as with all code questions, your local code inspector makes the final ruling.
Kent
A couple of things to consider...If you plan to use your garage for storing a vehicle(s) in the winter, you will find it very hard to keep the interior humidity down due to all the snow and ice that melts and evaporates. Also, you do not mention if you plan to have windows, but if you do, you will find it very difficult to keep condensation from collecting and puddling on or below the interior glazing. The cooler you keep the interior temp, the worse this problem becomes.
Good luck on your build.
Excellent feedback and insights. I guess I neglected to consider window condensate with lower temps, due to lower vapor holding capacity of the lower temperature air, right Garth?
Tell me, Martin, can I achieve (exceed) the R target by using ccSPF against the backside of the OSB sheathing? Am I correct in my understanding that spraying ccSPF indeed moves the condensate (sorptive) plane internally while increasing the external R value, and would allow me to meet N1102.5 requirements?