Discussion of unvented foam-free roof assembly

I’ve had this article stuck in my to-read list for a while, and just got around to it. I searched to see if it had already been discussed on GBA and didn’t see anything, please point me in the right direction if it’s already been covered:
http://foursevenfive.com/unvented-foam-free-roof-retrofit-with-dolphin-insulation/
This assembly was put together by David Posluszny, whose house in MA has been discussed in depth. This assembly is a bit different, as it’s installed in an existing attic and doesn’t include any changes to any roof layer from the sheathing out.
My question (which was also raised by Katy Hollbacher in the 475 website comments) is – this isn’t code compliant, right? Further, what makes this a safe unvented roof assembly?
If climate matters, I’m in Maine. Our projects almost always include cathedral roofs somewhere, and our current strategy is to install spray-foam, or spray-foam to the code requirement and then install a layer of batt insulation.
GBA Detail Library
A collection of one thousand construction details organized by climate and house part
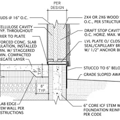
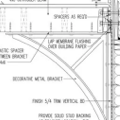
Replies
Sam,
This debate has been raging in New England for decades.
Many builders (and a few cellulose insulation manufacturers) firmly believe that this type of unvented roof assembly is safe, as long as the installer does a good job of dense-packing the cellulose. (To read a defense of this approach, see this article: How to Install Cellulose Insulation.)
Skeptical experts sometimes point out that there have been a few failures. Even one or two failures should be enough to make a builder nervous.
It's probable, of course, that there were installation errors that led to these failures. Perhaps the insulation contractors installed the cellulose at an insufficient density. But builders need to remember that installation errors are always possible.
The short answer to your question is: This approach violates the building code.
Some building inspectors in New England allow the approach anyway. Local inspectors have broad authority to approve methods that don't meet the letter of the code.
If you are interested in my opinion, I don't advocate this approach. It's always less risky to include a ventilation channel between the top of the cellulose and the underside of the roof sheathing.
Not only is it less risky -- it complies with the code. And if a builder ever gets into a legal dispute with an owner, it never hurts to be in compliance with the code.
Thanks for the link, Bill Hulstrunk did talk a bit about the theory behind the practice:
Replace drywall with Intello in the article from 475.
If drywall would be vapor retarding in winter, then getting it airtight would suffice. Unfortunately it is around 10-15 perms (depending on how many layers of latex paint is has), so not an effective retarder in that season to keep the cellulose and sheathing dry, even when installed airtightly.
In our experience, it is also not practical to make drywall permanently airtight. Furthermore it is not vapor variable like ProClima INTELLO Plus is - meaning that product is below 0.17 perms in dry winter conditions, while over 13 perms in humid conditions in summer if needed. Providing you and building inspectors with the confidence that this is a sound solution, if installed air-tightly, ie taping overlaps, using gaskets around pipes etc etc (making the insulation air-impermeable and verify this with a blowerdoor). This airtight layer does allow inward drying in summer with it high perm in that situation with inward vapor drive - this gives the roofs drying reserves that exceed the wetting potential in 99% of the cases in cold and mixed climates. This inward drying reserve is something that vapor closed (spray) foams cannot provide, albeit being code compliant....and the next code revisions are going in that direction. None the less a vented ceiling (either above or below the sheathing, is an even saver solution, but not always possible with dormers, valleys etc).
Disclaimer, we distribute ProClima's airsealing system, that includes TESCON VANA airsealing, tapes, gaksets and the best in class vapor variable retarder INTELLO Plus
Sam,
A couple of things come to mind:
- If all that was necessary to insure that roofs didn't experience moisture problems was an air-barrier, then why are we still having problems with them even though many areas have used very effective poly air-barriers for decades?
- With the best of intentions, workmanship and materials, no house has ever had a perfect blower door result.
- Systems that rely on perfect conditions for their success are not very resilient, especially over time, in the real world where building scientists don't have control over what occurs to a house or the behaviour of its occupants. Evaluating any new technique, we should ask ourselves: what are the consequences of minor imperfections or alterations over time?
- It may well turn out to be a good way to insult roofs, but the evidence isn't there yet.
Floris - thank you for your perspective. I appreciate the role that 475 has carved out on these subjects, and enjoy the project/application documentation that you guys put online.
Malcolm - agreed on your points. Now that I understand that success with this assembly likely is due to achieving a narrow window of performance with regards to air/moisture tightness, it seems unlikely to be a good fit for many of the applications I come across.