Different SIP thicknesses, different shell types, windows…..

Working on a fun home that will get some solar gains and pretty simple design. We plan to make it future PV adaptable when the costs drop some. Looking at a few wall design concepts.
Owner is really liking SIPs. I have nothing against SIPs, I think they are a great product. We have a plant within a couple hours that produces urethane panels so a lot higher r then the eps ones. Ships costs are next to nothing so more cost savings. The 4″ panel is approximately an r26 they claim while the 6″ is about r42. My thought was to use the r42 panel, but now we are looking at the costs vs energy use to see if this is the right way to go or not.
Running some numbers in my program, the 4″ panel would make the heat load about 19k btu. THe 6″ would drop it to about 17,500 btu. What this means for the current electric rate is a yearly savings of about $40. The cost differece is just under $2000 for materials in the panels, plus some added cost in window jambs, etc. I am guessing around $2500 difference. Doing super dirty and easy payback math (excluding extra financing, etc), best case is 60+ years. Knowing this, does it still make some sense to use the super insulated 6″ panel……..”just because”?
Same with the window arguement. I have them introduced to some of the good Canadian fiberglass companies, but they also like the locally made Pella Impervia (fiberglass) and the close to local Marvin Integrity. I have used the Impervia on projects before and they have some pretty good glass options. Their Smartsun glass gives me a SHG of over .5. Their air infiltration numbers are .05, only .02 higher the Inline (and similar). I have a project starting construction now using the Marvin Integrity (full ultrex). They do not have as good of u values or many glass options. They also do not publish their true infiltration numbers, simply <.30, the testing standard. Currently the price for the US/close to home windows is about $1500 cheaper then the Inline double panes and about $2800 cheaper then all triple panes. However if I mix doubles on the south and triples on the north, the difference is about $2000. Again, this makes for a 60+ year pay off with energy savings. Other shell options include vertical ICF (also produced locally) with an r roughly 26-28, or a 10″ double stud wall assembly. ICF is higher then SIPs and the double stud would be similar to SIPs. However the SIPs would decrease construction time, which could result in interest savings. I am also confident we can get a tighter shell, easier with the SIPs. So the questions are….first off: zone 6, about 7200 HDD the 4″ vs 6″ urethane SIPs…worth it to go to the 6″ just to hit the r40s? Full shell ICF- slightly higher cost, similar r as the 4″ SIPs…we are in tornado alley, so there are pros to ICF around here other then energy efficiency. 10″ double stud shell- approximately the same overall costs as SIPs, maybe cheaper. Slower build time, more work to make air tight. All options will have a vented trussed roof (no SIPs roof) with air sealed ceiling plane and r60 insulation. Also, the on going window arguments………….
GBA Detail Library
A collection of one thousand construction details organized by climate and house part
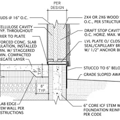
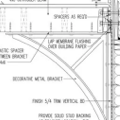
Replies
Jesse,
You raise many issues.
Briefly, you're right that superinsulated envelope upgrades can have a long payback period at current energy prices. Old story. However, other factors may matter -- comfort, the ability to ride out energy shortages, and the possibility of future energy cost increases.
Concerning your math: reducing the peak heating load by 7.9% only saves $40 a year? That's surprising. It sounds like the total annual heating bill is only $507. That's low.
Martin
The utility company did the quick cost estimating using my load numbers. Actually for the 6" panel they had around $400/year based on the all electric rate, which is currently $.041....so ya, pretty low.
Do you have any thoughts on the various proposed shell types?
Jesse,
OK, so you've got some of the cheapest electric rates in North America.
A better envelope is always a better envelope. But when energy is cheap, many homeowners don't see the logic of paying for a better envelope -- which is understandable.
You don't say how big the house is or how many window but it sounds like you can upgrade from R-26 with average windows to R-40+ with much better windows for a total of $4-$5k. My advice would be to spend the money and futureproof the home agianst rising energy prices. There are so many benefits to the homeowners other than today's energy bill.
Exactly. What difference does 4-5K make on a mortgage? Very little, and enough that the decreased operating cost offset it. Martin had an excellent post on true payback calculations not that long ago. To me, and I understand I'm probably in the minority, but I would prefer to step down a line on my kitchen cabinets to save money for a better performing house.
And on the other hand....
Opportunity cost. Putting that 4-5K toward the PV could provide better long-term performance, as many net-zero designers have suggested. As Martin says, old story. With no definitive answers.
Thanks.
All thoughts were exactly what I have been pushing on them. THe current electric rate is .08, still low, but by going all electric and having an Energy Star rated home (obviously will be much better then that) the owner can get .041 rate.
One interesting thing however is there does not seem to be much focus on SIPs on these forums (besides roof issues). There are a few blogs about owners building high performance homes with SIPs, but they are using the 6" EPS with good results which has a lower r then the 4" ones the owner is thinking about. THey too have read the blogs which is also why they are questioning it. Does anyone have any input on the double stud vs SIPs debate?
I obviously understand exactly what everyone is saying about putting the money into the shell. That is the thoughts, and the finishes on the inside are skimmed back to do so. Its many times hard to convince an owner to have a higher upfront cost to hopefully payoff big in the future.
The house is approximately 2300 sqft split between a main level and a walk out basement (to the north). There is about 9% south facing glass, and about 6% north facing (where the views are).
Only 2 east facing bedroom egress windows. No windows on the west. The garage is also on the west to help block some of wind for the house.
4-5k would pay for just under half of the PV system (after rebates and credits).
Several other considerations to muddy things up a bit. I would concur with the above responses, that unless energy prices go up, it is difficult to argue from a pay back perspective that energy efficient upgrades are worth it. However, considering the average American moves every 5 years and sells their home, then they might be able to sell their house for more and quicker...especially if it is some the areas where this is well entrenched, Portland, Seattle, Austin etc. Then there is the much greater comfort, which is certainly worth something. Also you might want to look at EPS based SIP panels. The down side to the polyurethane based ones is that their R factors degrade over time (something closer to R5/in) wheres EPS doesn't. Also when I was taking bids for our SIP project we found the EPS ones much cheaper. Lastly, the surprizing thing for me was that 12" EPS SIP panels were only 10-15% more than the 6" ones!
I would concur about the additional insulation being worth it, and would plan on increased utility costs.
I don't know where Kevin sees data on Iso degrading down to R5 except for in EPS panels ad materials.
I have looked into EPS panels as well. What is interesting is they are around 4.90/sqft for 10" blank panels, however the quotes I have received for fabrication have made them on par with the iso panels, higher in some cases for some reason. A lot has to do with shipping costs. The iso panels locally only cost about $150 to ship to the location. The other quotes are pushing $1k. Then you have the 10-12" vs 6" thickness issue which can decrease floor space and increase window opening costs. I also plan to sit the panels directly onto the ICF foundation and sit the floor structure inside the panel on the foundation, so the thinner the better for the panels. I also like the greener properties of the iso.
The long-term thermal resistance (LTTR) values of most types of polyiso are in the range of 6.0 to 6.25 per inch. While some conservative builders prefer to assume an R-value of R-5.6 per inch, I don't think there are any data supporting a value as low as R-5 per inch for polyiso.
Here is another thought...after reading Martin's service cavity blog, I am wondering if that might be a good option for SIPs as well. The thought could be to go with the r26 4" panels and then use a 2x4 cavity on the interior. One of the issues to deal with is the electrical and plumbing with SIPs obviously, so this would eliminate that. We could then batt insulate the cavity with cheap batts resulting in only about $600 in total cost (vs the $2000 difference between 4" and 6") and have similar r value to the 6" panel with the ease of the cavity. This would also help my SIPs to foundation issue as the 6" plus floor structure is barely fitting on the ICF wall. The 4" would allow for better bearing space for the floor. Obviously the interior wall would just sit on the floor structure.
$600 for a 2x4 service cavity material and labor? And insulated? Wow. I personally think its a great idea, but i think your estimate is a bit low unless there's no labor charge.
no labor charges included in that number. also about 140 lf of exterior wall. I am sure the owner would do the install as it would be pretty easy.
Nope pretty easy. Seems like a good plan to me. Would you splay the window openings for more light? 8 1/2" is getting pretty thick. Also, drywall returns on the window or custom extension jambs?
drywall returns on 3 sides of the window, but use bamboo plywood for the window sills. Splaying the windows is something I could discuss with them. Attached is a proposed detail.
Any thoughts?
Jesse,
It's hard to read the details at the sill, so I may be misinterpreting your detail. But it looks like your sill flashing is behind the 1x4 exterior trim. I don't like the looks of that exterior 1x4 -- looks like it will rot quickly, for sure.
I prefer a more subtle piece of trim -- usually just 1"x1" or 5/4" x 5/4" -- with the window sill drip extending well beyond the trim.
Jesse...
You didn't mention considering a modified PERSIST or the 'perfect' wall, but you are pretty close to one in the drawing you posted. The 'perfect' wall may be what you are looking for.
Martin
You are exactly correct...the window trim/frame is not shown ideal. That window detail component is Accurate Dorwin's, which puts the nailing flange flush with the exterior of the frame....not good at all IMO. Since the exact window brand is up in the air yet, I left that detail very generic and unresolved. Obviously when the time comes typically the flange is 1/3-1/2 back on the frame and it extends out over the trim/siding plane.
Bruce-
I have gone down the exterior thick foam route many times. My initial opinion would be the SIPs panels would install in a fraction of the time it would take to do a PERSIST wall and would most likely be a stronger system. While air tightness is achievable with either, I would also assume the SIPs make it easier to do so with less joints to worry about. I also have some concern about the foam shrinking or moving around over time possibly loosening the tape or opening up gaps around nail holes. Would I be correct with these assumptions?
Jesse...
First, I like SIPS, it just seems your diagram shows a double structure, SIPS and framing. I wish I had all the answers!
Here are my thoughts:
SIPS would allow a quicker dry in, though if you are then going on to build a service run as you described the total time would be similar. When using SIPS I would consider running the service bays horizontally rather than vertically.
I am not convinced the air sealing would be easier with SIPS as each joint could lead to direct path into the structure, thus be a critical joint. Staggering the rigid foam panels and taping each layer should provide some advantage for air sealing, except at the screws in the panel fields. The screws should be running into the studs though, so how much air would get through? In my mind the possible issue with the screws is the potential for condensation on the screw as some folks have mentioned on the site in the past.
I know folks are concerned about the shrinking and I certainly worry about tape. But when I look at the whole assembly the pressure relieving gap behind the cladding, in front of the insulation in front of properly air sealed wall sheathing is critical as it should reduce the amount of air movement between the insulation panels. Wouldn't the overlapping rigid panels essentially create a dead-end maze for air if the entire structure is 'wrapped' in foam? Since the pressure is relieved to the outside, little air should be forced to the wall.
Love the idea of plyboo sills w/ drywall returns. Please post a pic when done. Other than the trim detail Martin pointed out I think you're on a good path. With only 160lft of wall, I would think you will have very few joints in the panels, I'm in favor of fewer things to get right than more (like multiple layers of foam).
I tend to agree with the fewer joint idea. There is no doubt the joints are a weak spot in the sips shell, but there are far far fewer joints and connection points in a sips shell then a wood framed shell for sure.
I am discussing joint options with the manufacturer of the panels. I like the concept of using 2 plywood splines instead of a solid bock. Then after the walls are attached together, you drill a few holes through the connection and fill the void/spline space with foam. This will seal it completely and allow for a continuous thermal break (no solid framing).
I still have not completely ruled out ICF from footing to roof as I love how it provides a continuous thermal break, continuous insulation, and no weak spots (joints). Just have the window sealing and details that would be typical with any project however.
Our local power rates on the Calif/Oregon Border were the same as yours a couple of years ago. They are now $.11665/kwh for the bottom tier. #2 Stove oil was $.95/Gal in the early 1990's, it is currently $3.97/gal.. I suspect we are going to see dramatic increases in our Electric Rates as our Power Company removes Dams and converts to other sources of power generation. I would not have much confidence that your Electrical rates will remain low.
Off topic....
Jesse, If you're interested, shoot me an e-mail and I'll scrounge up some pictures of details we've done on a couple of really neat modern homes for trim/base.
bdrfab@gmail
Great discussion. Upgrades sound reasonably priced and become permanent. Upgrade countertops later. Worst ROI is to modify the shell or windows at some later date.
And I too think the low cost electric regions will suddenly be gone when whomever is least prepared.
My semi-Mormon good friend is adding a third fuel source this spring. Good to be prepared or at least be great friends with the bunker in types.