How does one best make CI to non-CI transitions in the same and separate walls?

Hi!
Some background
I am scrambling to integrate continuous insulation (CI) and max air sealing into a build that is in the final stages of the foundation pour. The timeline is tight for plan revision and re-approval without adding major delays — I’m in the Seattle, WA area, so dry-in before Fall is critical. Unfortunately, CI has not come up in discussions until recently (and by accident) and air sealing has had less attention paid to it than it should have had.
As I understand it, R3.5 is required in my new 2×6 walls (R21 inside interior cavity) and less in my existing 2×4 walls (R15 inside interior cavity). My total interior insulation plans allow me to meet code as-is without exterior insulation. The exterior:interior R ratio seems to be ~ 15% for my climate (Zone 4 Costal, Seattle area and using [this BSI article](https://buildingscience.com/documents/building-science-insights-newsletters/bsi-026-they-all-laughed) as guidance on how to calculate it), but I’ve read mixed things about how this is important regardless of insulation type or that it might only matter with rigid foam or a “wrong side” vapor barrier (i.e., using a vapor-closed exterior CI), and I am *planning* to use mineral wool for CI and fiberglass batting inside.
Questions:
So, I have a few targeted questions related to some wall assembly drafts I’ve been playing with (attached) and my climate zone (Zone 4 Coastal, Seattle area and using James Hardie plank or James Hardie shingle siding). The notes in these drafts are the primary changes I’m requesting on the approved plans or relevant context, even if already on the original plans.
1) Does adding CI mean I must now meet the CI-specific code requirements, or is total R of the wall just fine if I can meet the total R threshold?
2) Do dew-point effects, and thus minimum CI R-value, for my exterior wall assembly matter if I am using a vapor-open exterior CI like mineral wool? (see attached sketch “Exterior wall assembly Addition Only”)
3) Is there a good way to transition between CI and non-CI assembly in the same wall when retrofitting an existing wall? (see attached sketch “Exterior wall assembly, transition from CI to non-CI in single wall”) Specifically, I will need to bump out the assembly ~ 2-3″ beyond the non-CI part of the wall, and I’m wondering if an abrupt 2-3″ square protrusion is fine, or if I should do some smoother transition with 45-degree wedge-shaped cuts in the firing & CI.
4) One of our planned CI walls will end at a 90 degree inside corner with a wall that cannot receive CI due to setback restrictions. Are there any best practices one might recommend for abutting a CI wall with a separate non-CI wall at a corner?
5) Related to questions 1-4. The transition from CI to non-CI both in the “same wall” example (Q3) and “different wall” example (Q4) will create a section of the CI-covered sheathing that drops below the recommended CI R-value, as it will be receiving conductive R-loss from its adjacent or abutting non-CI sheathing. The section is likely to be very small and only at this CI/non-CI joint. Is it a concern in terms of dew point and wood rot in my climate and when using mineral wool?
6) Our current plans are to vent the attic space and only insulate the attic floor. Should we thus leave the attic’s gable-end walls as non-CI? Is there any benefit or perhaps event moisture related danger to adding CI to these otherwise uninsulated gable end attic walls in our vented attic? Is it pennywise and pound foolish to not just condition our attic (we don’t need the storage space, and I’d like to air seal the attic from the main house anyhow for air quality reasons. We *may* put an HRV and it’s small ducting runs up there under the loose-fill insulation, but it might also be fine in a closet or something)?
7) Do any of these answers change if I use rigid foam siding, which will provide slightly greater R per inch, and is a rain screen air gap needed with rigid foam insulation?
8) On the topic of insulation, but not quite CI: is it silly to insulate the walls of a vented (at 1 ft2 venting /1500 ft2 floor space) crawlspace. The entire crawlspace will have 10mil poly floor barrier battened at the base of the interior stem walls? The new foundation has a tar-like damp-proofing and exterior dual foil-faced polyiso insulation outside of that, and I’m wondering if I should complete the insulation on the rest of the foundation (mainly interior walls due to above noted setback issues).
9) Back to CI: how to you finish the top edge of a CI wall assembly with mineral wool (see see attached sketch “Exterior wall assembly Addition Only”)? I’ve extended the sheathing & vapor barrier up just beyond to the top of the top plate to the underside of the roof, with CI ending just beneath it and a bug screen covering the air gap between siding and vapor barrier to allow flow through the air gap. Is this not OK where fire rating is needed? Is a thermal break needed between underside of roof and sheathing? Anyone have a relevant architectural detail that I can examine?
If anyone has insights they can share on any of these questions, I would be eternally grateful. Full disclosure: I did receive a couple of good comments on [a more vague question around Dew Point effects](https://www.greenbuildingadvisor.com/question/join-a-continuously-insulated-wall-with-a-regularly-insulated-wall).
Thanks so much!
GBA Detail Library
A collection of one thousand construction details organized by climate and house part
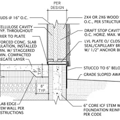
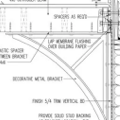
Replies