Design Charrette: General Building Envelope Questions for Mixed-Humid Climate

I’m in need of some focused input on the overall insulation strategy for a home I’m designing, and rather than taking hours upon hours searching through the archives and reading what now seems to be seemingly countless (and often divergent) opinions on these matters, I’m hoping through a quick online charrette a general consensus could be found to help me and my client understand the best route to achieving a fairly high-performance home for a mixed-humid climate (only!) in the Blue Ridge Mountains (meaning we don’t get quite as high humidity levels as lower elevations, but can get some fairly low temperature wintertime cold spells).
Some background, assumptions, parameters, and a couple specific questions to guide the discussion:
I’ve already learned quite a bit over the years from this website, but as I suggested above, there is often such divergent opinion on even some of the fundamentals that it can leave one’s head spinning. Thus my desire for “focused input”.
Assume that the builder is very competent, but not necessarily fully knowledgable about all the intricacies of green building design and detailing, such that you have to design to the builder, rather than trying to fully move the builder into a world he’s not yet fully familiar with. Besides, I’m still learning, too. I know this is a separate discussion that goes to “Pretty Good Building” concepts, so please set that aside—not to ignore it, just not to spend time on it here. In my area of the country it is still rare to find a builder who is even willing to move in this direction, without, I might add, using that move as an opportunity to up-charge so significantly, thus putting out of reach better building practices for the average homeowner, who tends to be the type of clientele I serve. For example, I’m lucky to get a builder to use crinkled house wrap for a little bit better drainage plane. I will spec it, but once I’m out of the picture, the builder says to the owner it’s “x” amount more and the owner chooses standard house wrap. In the case of this particular home, however, the builder will generally move in the right direction, and the homeowner does want to get it right and is willing to pay a bit (not to say exorbitantly) more to do so.
The shell of this one-story home is as follows: Floor: radiant slab-on-grade (also set aside that discussion of whether or not it’s worth it. The client wants it. Period.) Walls: brick (primarily, with small areas of cedar lap over furring for drainage plane) over air space over house wrap over 1/2″ sheathing (yes, probably OSB) over 11 1/4″ double stud walls. Roof: all ventilated cold roof with deep enough trusses and shed roof rafters of either 16″ TJIs or trusses for 15″ max. thick insulation. Windows: uPVC German-style, u-factor 0.27 or so, possibly with triple-glazing for 0.17 or so u-factor (willing to hear input on worthwhileness of triple glazing in mixed-humid. Most of the discussions at GBA seem to deal with cold climates. Also, the additional cost is a major factor on whether the client goes to triple).
Assume tight construction and GSHP for heating (again, set aside that discussion of whether or not it’s worth it, but in this case if you can provide a compelling argument for an alternative, please do so), a Zehnder ERV system for ventilation, no air conditioning, and possibly a standalone dehumidifier if found to be warranted.)
The goal is not net zero or PH standards, though if we get close without exorbitant (there’s that word again) cost, we’d all be happy.
Question: in the mixed-humid/mountain climate with the wall shell as proposed is there any particular insulation to be avoided or recommended to keep the sheathing from getting wet—and at what r-value? Or is that really more a cold climate concern, as opposed to here where drying potential is in both directions?
At what level of insulation r-values do we reach the point of diminishing returns? Like I said about divergent opinions, I’ve seen where both “more is always better” and “‘x’ is good enough” propounded.
Finally, I’ve not mentioned the size of the home, but does that really matter with regard to the questions I’m seeking answered?
GBA Detail Library
A collection of one thousand construction details organized by climate and house part
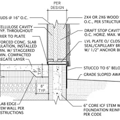
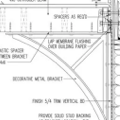
Replies
Marc,
You didn't tell us your climate zone -- I'm assuming Zone 4.
One approach is to use the table developed by Building Science Corporation for "high-R enclosures." The table is reproduced as an image, below.
The table comes from this document:
High R-Value Enclosures for High Performance Residential Buildings in All Climate Zones.
A double-stud wall is usually insulated with blown-in fiberglass or dense-packed cellulose, but it's possible to use mineral wool or fiberglass batts if you want.
With the wall you have described, the hardest part will be the supervision needed to make sure that the brick mason doesn't fill the air gap with mortar droppings. The air channel must be clear (not clogged) and well ventilated if you want the sheathing to stay dry.
The size of the home is very relevant, especially if you want to install a ground-source heat pump. A GSHP only makes sense for enormous houses. For an average house or a small house, it's more cost-effective to heat with ductless minisplits.
In zone 4 there's no point to an 11.25" double studwall unless you're going for PassiveHouse or something. According to Table 2, with a reasonably careful design it's possible to hit Net Zero Energy with a PV array that fits on the house at Y2010 type PV efficiency with an R25- whole-wall type construction. (Efficiency has improved incrementally since then, and you might be able to do it with R20 whole-wall construction.)
An example of the estimated R25-ish wall it would take in zone 4 would be 2x6 w/ R20-R23 cavity fill + 2" of continuous rigid polyisocyanurate on the exterior. That's a lot easier to build than a double-studwall, and it has fewer thermal bridges to detail since the studwall plates & subfloor & band joist all have R12-ish foam on the exterior side. At 2" thickness on the foam it complicates the masonry tie issues a bit on the brick-clad sections, but there are standard products that will accommodate 2" without too much trouble. (At 3", 4" 5" it gets a lot harder.) Almost any brick-tie can work with 1" foam, but shrinking the foam to 1" takes a huge chunk out of the whole-wall performance.
That's a considerably thinner wall, and all of the structural timber will run drier than in a double-studwall approach since it's partially inside the insulation, on the warmer-in-winter side of the foam. With a double-studwall/brick the sheathing would be subjected to the intense moisture drives of the brick cladding. With the foam-over approach all drying is toward the interior, but with R12 on the outside there is huge dew-point margin at the sheathing layer for a mixed climate.
In a zone 4 climate with low-temp slab radiation and an optimal system design an air source chiller (Chilltrix, etc) or Daikin Altherma air source hydronic heat pump would deliver GSHP type efficiency for less money. In a humid climate latent cooling is important, and it might be better/easier to take a mini-split approach rather than chilled water wall-coils, but that's a detail to be determined once you're into the weeds a bit more on the mechanical loads. Humid climates are lousy candidates for radiant cooling, but with sophisticated controls it can be done in combination with other heat pumps to manage the latent loads. It's a bit silly to specify the mechanical equipment before the loads are quantified though- it matters (a lot!).
Martin, sorry for the oversight, and thank you for the reply. I had it mind to say Zone 4 in conjunction with the Mixed-Humid, Blue Ridge description. I've seen the building science document/chart and I put that into the "divergent opinions" category, because I've also seen elsewhere (including here at GBA) other numbers/rules of thumb which didn't match that, along with a general statement (I believe from you) of "the more the better".
Martin and Dana: Like I suggested the owner doesn't have it as a stated goal to meet any certifications or definitions of Net Zero or PassivHaus, but he certainly wouldn't mind if that resulted from a thick wall strategy. The house is oriented and structured such that a future PV addition would work quite well. Also, the reason I want to stay within the parameters of double stud vs. rigid exterior for the purposes of his post is for essentially the same reason I wouldn't go to an African country and try to propose building with stick frame. It is as I said: in this area of the country finding a good builder who will build the way you suggest, Dana, is still close to impossible. My definition of "good builder" includes a moral component, i.e., someone who is not going to over-charge by taking advantage of these "exotic" methods. They're not exotic to you or me, perhaps, but they're certainly sold that way. Further, because exterior rigid insulation systems still are rare in these parts, even more rare are the subs who will do it right. In my mind the double stud wall has less intimidation factor in the minds of framers and thus I have a higher probability of getting that accomplished reasonably well. On the other hand, I've even had trouble having any builder buy off on advanced framing techniques. Changes around here have to be sloth-baby steps.
So that said, while I appreciate the attempt to move away from the double stud, Dana, if you had to stay within the double stud parameters and everything else I said, what would you recommend for insulation values and types? How do we avoid the wet sheathing potential assuming the 11 1/4" wall?
Oh, and thank you for the input on the mechanical. No, the mechanicals are not being designed first before quantifying the loads. As I suggested, I think the GSHP is certainly up for grabs, which is why I asked for compelling alternatives. My client started with the desire for the warm floor and GSHP. I've suggested movement away from the GSHP but not the radiant, simply because the comfort issue (on the feet) of radiant trumps all other arguments. But my client is certainly willing to explore GSHP alternatives, and I'm certainly not learned enough to know all the options.
Marc, I'm building in Tennessee, and I appreciate your comments about finding trades who will do things differently from how they've always done them. For this reason I have settled on a 2x4 wall with dense-pack cellulose, and 4" of foam on the outside with EIFS for the finish, resulting in R-26.
For the same reasons that you yourself postulate as a given, I urge you to reject brick. I have not yet seen an air space behind any installed brick, nor a capillary break or flashing between the brick buried below grade and the brick above the foundation, nor any weep holes anywhere, even in the more expensive homes in the Parade of Homes last week. I think it was Lstiburek who said just don't use it.
EIFS on the other hand is common around here (meaning I can easily find someone who can achieve a good result), and adding 4" of foam increases the price by only the material cost. Price point is less than brick as well.
You may similarly want to educate your client about radiant floor heat. If you insulate as you propose, and your construction is reasonably air-tight, your client will never feel a warm floor beneath her feet. There simply will not be a need for the temperature to get so high as to feel it on the skin. The floor will just be not-cold, which can also be achieved with R-7.5 foam beneath the slab as suggested in the BSC table Martin copied above. So your client may be demanding it now, but will be disappointed if it is installed. Better to disappoint her dream than her reality.
Intus has many window packages available. I will be choosing the 4, which is less expensive and yet gets to 0.194 Ug. VT is also significantly higher than anything offered locally.
A double studwall approach can work, but it doesn't take an 11.25" double-studwall to hit Net Zero Capable in a zone 4 climate.
If you make the structural walls 2x4 16" o.c. and use finger jointed 2x3s for the interior walls you can pull off an R25-ish whole wall in about 8", outer stud edge to inner stud-edge. See the details for case 4 in the following docment, which is a 9.5' double studwall w/cellulose, that comes in at about R30 whole-wall:
http://apps1.eere.energy.gov/buildings/publications/pdfs/building_america/high-r_value_walls_case_study_2011.pdf
If you use asphalted fiberboard for the sheathing it's moisture tolerance is quite high against moisture drives (works great under brick), and adds about R0.5-R1 in whole-wall R above an OSB or half-inch plywood sheathed wall would have. While there are structural grades of fiberboard, with a double-studwall the sheathing doesn't even have to be structural- you can brace the studs on the interior side without needing to let-in the bracing. If you have true batt-installation artists available you can use R15s in the 2x4 wall as soon as the shell is up and air-sealed, and use blown insulation for the rest after running the plumbing & electrical. Or, wait until it's all plumbed & wired and use damp-sprayed cellulose (or damp sprayed JM Spider in mesh,which is higher R/inch than cellulose.)
If you sheath it in OSB you can still do OK using Huber ZIP behind the brick. The wintertime moisture drives are fairly modest in a zone 4A climate, and if you used cellulose rather than fiberglass it would add plenty of moisture resilience to the assembly. If using fiberglass you might consider using a "smart" vapor retarder behind the interior side gypsum, which limits the interior moisture drive in winter, but doesn't impede drying toward the interior if the cavity ever gets wet. Of the more-available smart vapor retarders, Certainteed MemBrain is pretty cheap & effective ($100 in 8' x 100' rolls even through retail type outlets, but also available in 10' and 12' widths through distributors). It's basically 2-mil nylon- installers who know how to make 4 & 6 mil polyethylene vapor barriers air tight will have no problems installing it. But unlike polyethylene, it doesn't create moisture traps or condensation issues, summer or winter.
There are multiple vendors of air-source hydronic chillers that can be made to work at high efficiency with slab radiation, but without the load numbers the water temp requirements and the 99% outside design temp there's no way to recommend one. Chilltrix has a nice modulating unit of modest capacity and decent specs that might work (http://www.chiltrix.com/ ) there are others, but many would be too big. (I've never designed a heating system around them, but the concept is clear enough.)
Simply putting foam under a concrete slab doesn't make it warm enough to be bare-foot comfortable in winter, but it doesn't have to be much above room temp to feel the difference. It's not a bad way to go for heating, but it's a fairly subtle luxury in a high-R house, since most of the time it's BARELY above room temp, even in the winter.
Another alternative to double stud wall that is definitely doable, even seemingly in Tennessee, is regular single stud wall with ZIP R-6 on the outside. This is extremely easy construction it seems to me. It is just as easy as typical construction but incorporates the foam outer layer with the osb sheathing. If your builder can master osb sheathing then believe me they can master ZIP. It also makes flashing and keeping the house air and water tight extremely easy. I would use 2x6 framing so as to allow more insulation within the walls. I think this is the most effective way to build an energy efficient tight home in a climate like Tennessee. And there is very little to go wrong in this type of construction though people always seem to find a way, don't they?
EDIT: I just noticed Dana's ZIP suggestion above. Yep, I second that vote.
Marc,
If your client has at least a 30-year outlook on operating costs, then I'd recommend:
~R-20 under slab insulation with as much insulation as you can muster at the slab edge
2" exterior insulation over a 2x6 insulated wall
R-60 to R-70 blown in insulation in the attic
If the client is willing to pay for in-floor hydronic heating, then they should probably consider triple pane windows. Lots of options to choose from...too many to list here...
As Dana pointed out, if the building enclosure is going to be quite good and the heating load quite low, the slab temperature, even on a very cold day, will not likely be noticeably warm to the feet if the hydronic loop is evenly spread throughout the slab. If you concentrate it in several areas, you can get the same heat output and some degree of "warm toes" effect. The downside is that the other areas of the slab will be at room temperature, which is not comfortable in the winter unless you're wearing slippers.
I'm (obviously) not sure exactly where this house is going to be built, but I've worked with a lot of good people and some very good people up and down the Shenandoah Valley. The good ones are out there. Feel free to contact me outside of the Q+A if you'd like to chat.
http://www.think-little.com
Thank you all for the excellent info and suggestions. It's focused my thinking about the direction to go and how to advise my client (which will include contacting you, John, shortly. Interestingly, that was on tap before I posted this topic. You and I were introduced via email on another project a few months ago, if you recall, and the builder on this project brought your name up.)
When we fully sort out the whole system I'll post the results here, but for now a few comments in response to the various suggestions...
I like the idea of rigid insulation over sheathing, in particular when it's part of the EIFS route as Dave suggested. One of my best energy-performing houses is just that, a standard Dry-Vit system (1" foam) over 2 x 6 with R-19 batts (yes, with StuccoWrap and OSB). I like it particularly because it puts the primary onus of rigid insulation installation of the EIFS crews, and there are at least a few experienced crews available. Generally speaking, because I hardly ever have a say in the final decision on builder choice and his crews, I have to work from a basis of assuming the crews will not be ready to make quantum leaps in detailing ("baby steps"). This is the area of the country I am in. Dave and Eric in Tennessee (I'm guessing eastern, yes?) get it. So I tend to filter out building systems and methodologies which might be like presenting Masters Thesis work to high school juniors. In other words, I feel like I have to operate on the KISS principle as much as possible while still moving my clients (and their builders) to better building practices. That's my philosophy, anyway, informed by experience.
Brick is a non-negotiable in this project, as it often is with other traditional materials and styles my clients desire for our neck of the woods. So, while I like EIFS and the possibilities with stucco looks (my own home is a synthetic stucco on Durisol ICF), it doesn't usually play well here (a number of neighborhood's CC&Rs flat out ban a stucco look). As far as the problems with brick, believe me, I know all about it. My first brick home about 15 years ago was under construction and the brick was laid about halfway up the wall when the GC called me at the time of some heavy rains to help diagnose why there was so much water in the basement. I looked for weep holes, and not finding any, I suggested to the GC to drill some holes through the joints. He did and the water came gushing out. I have confidence that the builder for this post's subject home will keep an eagle eye out for properly done work (I'm not usually retained by my client's for construction observation services).
Huber ZIP, yes. Huber Zip-R, probably not (yet). Again, baby steps (even for me in this case). If I can keep to using prescriptive wall-bracing design I will do so, in part to bring the best value for my client, only bringing in an SE where absolutely necessary. Likewise, the builders around here have taken a long time adjusting to R602.10 & .12 requirements, and it appears (only on quick look—I admit I could be wrong) that the Zip-R will bring additional complications we're probably not quite ready for.
Finally, "finger-jointed 2 x 3s"? Right when I read that I had a suspicion that that would be a non-starter. I called the local supplier (an 84 Lumber center) which supplies the vast majority of framing material to the builders around here. "Do you have this?" (I could hear the head-scratching on the other end. Never heard of it.) "What about standard 2 x 3s?" "No. We don't carry it. We don't supply it."
Marc,
I'm in Nashville and we just finished framing. We sheathed in Zip-R. It was not cheap at about $44/sheet, but it's on par with OSB plus 1"rigid foam (super expensive around here for some reason), but with just one installation. The framers didn't flinch a bit since they had experience with regular zip. It went on about the same. We only had to make sure they accounted for that inch of foam on layout and they were good to go. Overall I'm pleased, but I obviously don't have performance numbers yet.
I second the whole baby steps thing. The industry here builds big cheap houses. Small, quality houses just frustrate them. The big houses gives them a lot of room to fix mistakes. I am lucky and have a great architect and builder who get it. Slowly but surely we're making progress. It's not for the faint of heart though.
Finger jointed 2x3s are straighter than 2x4s, and can usually be ordered through distributors. They're not a particularly expensive upgrade, but if the local distributor doesn't even know where to order them, go with 2x4s. Milled 2x3s tend to be twisted and bowed (beyond all reason!), making for lousy choice for the framing of a finished interior wall.
You can design a 9.5" double studwall using 2x4s that comes in between R25-R30, which makes Net-Zero-Ready a reasonable goal (provided the other assemblies are comparably up to snuff thermally.)
Can I assume the local distributors know where to get asphalted fiberboard sheathing, or is that off the table too?
There's no advantage to using ZIP-R in a double studwall other than it being 0.5" thinner than an equivalent performance double-studwall.
R19s? Seriously? Are people still installing low density R19s in exterior walls in TN? Compressed to 5.5" in a 2x6 assembly they only perform at R18, which is part of the rationale behind code minimums being boosted to R20.
In zone 5 2x6/ R20 is code min, and mid-density R20 batting being manufactured by the mile, but high density R21s and R23 rock wool are superior to the contractor-roll R20s, and worth specifying in a higher-performance wall if batts are the only solution.
I'd be a bit surprised if the local distributors carried MemBrain, but any Certainteed distributor should be able to order it up for you (along with R20 and R21 batts). If not, it's available retail online without a budget breaking mark-up, and still cheaper than the European smart vapor retarders.
Dana,
No, I wouldn't call for milled 2 x 3s. I know the issues. And no, I haven't checked on availability of asphalted fiberboard sheathing. You'd be amazed at the distance one has to go for certain building products which you'd think would be readily available. And then you get back to the issue of finding builders who will work outside of what they're familiar with. This stems from, I believe, deeply ingrained cultural mindsets. 5 years ago I started specifying Obdyke's "Home Slicker Plus Typar" and it met with such resistance that I quickly gave up on that and switched to just attempting crinkle wraps (see my OP).
R-19s, yes, seriously. That was 6 years ago, though I've be specifying R-21 for about 10 years. Again, just because I specify it doesn't mean it's going to get done, whether in Tennessee or here in southwestern Virginia. Just correcting your assumption. I never said I was in Tennessee! Still, the cultural roots of the two regions are pretty much the same.
As John said in post #7 there are some good builders around my area—"good" as in their expertise and willingness and ability to build better homes. But quite a few of these good builders I know or know of also happen to command 25 to 35% overhead and profit margins. I'll leave it to your imagination as to what kinds of things the homeowner is willing to cut in order to still achieve a reasonable semblance of their overall programmatic space needs.
PS The energy code for Virginia at the time of the R-19 home (plus the EIFS) required R-13 for walls. Now it's 15 or 13+1. By accounts of the owner in terms of it's energy performance I think it certainly moves into the pretty good house category, whether you believe it or not. Of course the owner did a heck of a lot of air sealing because that's something he couldn't get the builder to do.