Dense pack cellulose retrofit for a Chicago brick veneer home

I am about to have my 1950’s one story brick ranch home insulated. It has a brick veneer with 1” air gap followed by a “celotex” type sheathing, with 2 x 4 studs, than rock lathe plaster finish- no insulation in the exterior wall assembly. It also has a new roof as of Nov. 2010 with 2 courses of ice and water shield, with almost 24” overhangs and newer guttters with long downspouts away from the house. Also the bathroom fan is a Panasonic, venting through an insulated flexible duct exiting the underside of the soffit area. The attic hatch is going to be insulated with 2” foam board top and bottom and weather stripped on the edges.
The attic has a mix of blown mineral wool and blown fiberglass, that is not sufficient ( 2 x 6 rafters on the attic floor, with the insulation up to to top only ). Also, the rim joist area doesn’t have any insulation.The basement has a full height of 8′, and is a partial older finished basement with studs, no insulation, and paneling.
I had an energy audit performed on the house this past spring with a report that states “The blower door test revealed air leakage of 2200 CFM50 (cubic ft per minute at 50
Pascals pressure). Assuming the volume of the house to be approximately 20,000 cu. ft., the air changes per hour at 50 Pa (ACH50) are 6.6, which is relatively tight. This number translates to about 36% ACH natural, or a loss of 36% of conditioned air each hour throughout winter.”
I have researched the whole project before, during, and after the audit; this website has been the most influential and educating by far, and I think I have come to some conclusions…
1. Use a dense pack cellulose for the exterior wall cavities.
2. Seal the outer surface of the brick with silane/siloxane water repellent.
3. Air seal the attic floor before blowing cellulose insulation to have a finished R 48
4. Insulate rim joist area with rectangles cut from 2” Owens Corning FOAMULAR¯ 150 extruded polystyrene insulation, sealed and affixed with 2 part spray foam and Roxul Safe and Sound batt insulation as a fire barrier.
My questions pertain to the procedure the insulation company should / can use.
Has there been any success in drilling and filling the exterior walls with dense pack cellulose from the “rim joist” area under the bottom plate of the exterior wall, instead on drilling and filling through the interior wall through the plaster? ( My roof is a hip roof, and access to the top plate seems impossible.)
Should the installers move the existing old blown in insulation in the attic, and spray the entire attic floor with a thin layer ( approx. 2” ) of open / closed cell foam for air sealing, then blow the cellulose over that? Or just have them do the canned foam approach. ( I am concerned mainly about the interior wall junctions not being air sealed sufficiently, or overlooked all together.) Or is it a waste of money? I am going to do the rim joist area myself to save some money, and leave the other areas to the pro’s.
Mainly, I would like to avoid the extra mess, complication and expense of having the holes drilled in the plaster on the exterior walls for the dense pack and go through the underside of the bottom plate, it seems feasible as I have access from below the whole way around the basement.
Is that something that can be done with a dense pack cellulose? Or any type of insulation?
As a whole, am I on the right track???
Thanks for any help,
Chris
GBA Detail Library
A collection of one thousand construction details organized by climate and house part
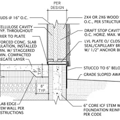
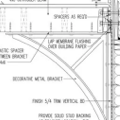
Replies
Chris,
1. I have never heard of anyone dense-packing walls with celluose from the basement through holes in the bottom plate. I hope that a cellulose installer can comment on whether that will work.
2. Installing a continuous later of spray foam to air seal your attic floor is likely to be more expensive but would probably be more effective than using canned spray foam. But really, the quality of the job depends mostly on the skill, knowledge, and dedication of the air-sealing workers rather than the method used.
3. Your walls are likely to experience inward solar vapor drive during the summer. Brick veneer and Celotex sheathing are a bad combination. If you intend to air condition your house during the summer, you must make sure that your walls have no interior polyethylene or vinyl wallpaper, or else you will end up destroying your walls quickly.
Martin,
Thanks for the reply, and I am concerned about the solar vapor drive too. With my plan, should I apply the silane / siloxane on the brick? As far as I can tell there is not a poly vapor barrier in the wall assembly, and no vinyl wallpaper anywhere in the house.
Also, looking at the results of the energy audit, do the numbers show a relatively tight house?
I forgot to mention all of the windows have been replaced with Pella windows in 2004.
What kind of change should I look for after the project is complete in the numbers from a well executed retrofit?
Chris,
1. No, 6.6 ach50 is not "a relatively tight house." A 2002 study of 24 new Wisconsin homes showed a median air leakage of 3.9 ach50. According to Matt Gates, "Most new home builders in Minnesota get to 2.5 ach at 50 pascals. Some builders we work with get below 1.0 ach at 50 pascals."
2. Masons and brick experts I trust advise that neither silane nor siloxane should be used to try to seal bricks except in unusual circumstances. These sealers can cause more problems than they solve.
3. I think you'll be OK as long as you don't have polyethylene or vinyl wallpaper. However, if you have any mirrors on the wall, or particleboard cabinets screwed to the wall, check behind them now and then. I wouldn't put any mirrors or vapor-impermeable artwork on exterior walls, especially the south and west walls, if you have air conditioning.
So for my plan, and age / style of home I should look for numbers like the "2.5 ach at 50 pascals"?
Should I worry about the dense pack cellulose in the exterior walls, and change my plan to a different ( open cell foam??? ) insulation with the said brick veneer and celotex sheathing combo?
I don't want to beat a dead horse, but want to do this correctly for my situation. It seems to me that all I can gather from reading about all of this, is that old houses like mine built in the 1950's with no insulation in the wall cavities performed ok as a wall assembly ( ignoring the waste of energy in a cheap energy era. ) Obviously not even close to the way it is done now, but I can say there is, for now, only one way to do it right with the new products and techniques and I want to have it done that way.
I started out thinking the open cell foam was the way to go for the exterior walls, then was convinced by the energy audit company to go with dense pack cellulose. I have had companies come in to give estimates for both spray foam and cellulose, and need to pick one or the other soon.
For the contractors, anyone work on a home like mine with insulation either foam or cellulose installed from under the bottom of the wall from the basement through a hole drilled through the bottom plate instead of drilling holes in the plaster wall?
Chris,
Your air tightness goal should be the same as everybody else's: "as tight as possible." Don't obsess about your number, but strive to make your house as tight as you can, within your budget.
Because of inward solar vapor drive, spray foam makes more sense for your house than cellulose. But as I explained already, I think either will work.
Chris,
I have a home with walls that are brick on 2x4 studs and a questionable perforated aluminum radiant/bulk water barrier on the outside of the studs just behind the brick. I like cellulose but I'm not comfortable using it against an older brick wall (1937) with a questionable drainage plane. Bulk water and cellulose don't mix.
Instead I used closed cell foam on walls that were open and dense-pack fiberglass Spider insulation blown through drilled holes on walls that were intact. The Johns-Manville Spider insulation is fibrous like fine cotton -- it is nothing like the fiberglass in batts and you can dense-pack it. http://www.specjm.com/residential/insulation/jmspider.asp
I felt comfortable with this approach but you may not want to use closed cell foam to insulate the inside of old brick walls in areas with heavy freezing. See http://www.buildingscience.com
http://www.buildingscience.com/resources/more-about-brick
William,
Thanks for the info,
I too am not comfortable with the cellulose in my situation. I just had a company give me an estimate for Air Krete, a cementuous foam. I don't know if it is the right thing to do either. Here is the link:
http://www.airkrete.com/
Martin,
Do you have an opinion on this solution...
Thanks again
Chris,
I've never used AirKrete, so I don't really have an opinion. I've heard both good and bad things about it. The worries: it is a crumbly type of insulation that may shrink away from framing or deteriorate over time. But I have no firm data or examples of failures.