Demilec HFO high lift vs Gaco one pass low GWP

Building a home near Boston and getting down to time for insulation.
I’m using Zip R6 sheathing for a thermal break on the outside.
Then planning 2″ closed cell in walls then filling the cavity with blown mineral wool.
Backs of roof are all R49 closed cell.
My question is if anyone has experience with these to products or has strong feelings one way or anything between Demilec and Gaco either in terms of product of company standing behind it.
GBA Detail Library
A collection of one thousand construction details organized by climate and house part
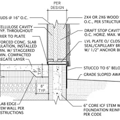
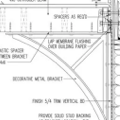
Replies
Dave,
Cannot comment on either product but think you should review the comments in this thread (and especially Dana Dorsett's take on using closed cell foam).
https://www.greenbuildingadvisor.com/question/closed-cell-spray-foam-demelic-heatlok-pro-hfo
>"My question is if anyone has experience with these to products or has strong feelings one way or anything between Demilec and Gaco either in terms of product of company standing behind it."
I don't have strong feelings about either vendor, but I have strong feelings about how this type of product is best used.
Even HFO blown closed cell foam has a fairly hefty CO2e footprint, and should be minimized where possible. See:
https://materialspalette.org/wp-content/uploads/2018/08/CSMP-Insulation_090919-01.png
Any closed cell foam between studs is a waste, the 2" of closed cell is buying you next to NOTHING on thermal performance! Do the math:
https://www.finehomebuilding.com/membership/pdf/184243/021269086NRGnerd.pdf
The R6 ZIP sheathing is sufficient R for dew point control for up to R24 in the cavities in a Boston climate so for 2x6 framing you'd still be fine at the ZIP-R/ rock wool boundary with only a Class-III vapor retarder (standard latex paint on wallboard), or a "smart" variable permeance membrane vapor retarder such as Intello Plus or Certainteed MemBrain.
For an R49 unvented cathedralized ceiling it's pretty safe to do 3" of HFO-blown foam + R30 rock wool batts or R30 blown fiberglass. R30 cellulose would be greener (would almost offset the CO2e of the 3" of HFO blown closed cell foam), and that stackup fits neatly in a 2x12 rafter bay. The framing fraction of rafters is usually much smaller than walls, but R20 foam + R30 fiber (any type) is still going to outperform 7-8" of closed cell foam.
The thermal diffusivity of cellulose is considerably lower than closed cell foam or rock wool, and though it would be subtle, there is a small but measurable energy use benefit to going with R30 cellulose rather than rock wool in the unvented roof, independently of the lower thermal bridging. The higher distributed thermal mass of R30 cellulose inserts a delay between the peak outdoor temperatures (either hot or cold) and the peak ceiling temperatures (high or low), which lowers both the peak and average heating/cooling load of the roof gains & losses.
Dana.. back in September your input helped with this approach:
https://www.greenbuildingadvisor.com/question/sub-slab-insulation-for-walkout-basement-near-boston-zone-5
“ The 1" ZIP-R isn't much of a thermal break @ R3 on R6.6-ish 2x6 framing, but better than nothing. It is insufficient for dew point control without adding 1" flash of closed cell to the interior side.
With 1" ZIP-R and 1" of closed cell (R9-R10-ish total) there is plenty of dew point margin in climate zone 5 for filling the remaining 4.5" with blown cellulose (~R17) or 1.8lbs blown fiberglass or a compressed R21-R23 fiberglass or rock wool batt (~R19). Despite the much higher center-cavity R, the whole-wall performance difference between filling the full 4.5" fiberglass or cellulose vs. 4.25" of closed cell foam is negligible compared to what is gained with the R3 ZIP. Due to the large difference in thermal conductivity of the framing fraction, even at a 20% framing fraction (24" o.c. framing, single top plates) the framing would be conducting more total heat than the closed cell foam.
The closed cell foam in the cavity is buying next to nothing from a thermal performance perspective, so using more closed cell foam than is necessary for dew point control is pretty much a waste.”
I also included the heat and moisture analysis for Boston that was shared with me. Seems 2 inches plus the r6 should be enough but still not sure if there’s a difference between the vendors.
Thanks
Dave
You realize that Demilec is only in the business of selling foam, and that their analysis is at odds with the IRC prescriptives for Class III vapor retarders (such as interior latex on wallboard rather than 6 mil polyethylene) in chapter 7, right?
https://up.codes/viewer/washington/irc-2015/chapter/7/wall-covering#R702.7.1
Demilec's stackup shows gypsum board, but no PAINT! (Gee d'ya think it even matters? :-) )
Garbage in = = garbage out (can somebody please take the garbage out?)
Unpainted gypsum board runs about 50 perms. Gypsum board painted with standard interior latex runs about 5 perms. There's a difference.
They are also talking about eliminating CONDENSATION, rather than avoiding moisture BUILD-UP of liquids or adsorb to levels that can cause harm (which is the real concern). Fogging a mirror is condensation, but is it a problem?
When it's cold enough a thin film of condensation will form on the ZIP-R taking moisture from the entrained air in the rock wool, lowering the vapor pressure inside the cavity relative to the conditioned space. But the rate at which moisture is pulled from the conditioned space through 5 perm paint is very limited, so when it warms back up teh condensation goes back into the rock wool as water vapor. This can happen dozens of times over a winter, but it's not a problem as long as it doesn't continue to draw more moisture in. With R6 on the exterior of R24 at the average wintertime temperature in Boston there is not moisture build up over a winter to matter, even if during cold snaps non-harmful "So what?" amounts of condensation do occur from time to time at the foam/fiber boundary.
If you're still concerned about interior moisture drives using only latex paint as the interior side vapor retarder, a sheet of Intello or Membrain is a lot cheaper and greener than even one inch of closed cell polyurethane, and would take the vapor permeance down to about a half-perm when the moisture in the rock wool condenses onto the foam, pulling even less moisture from conditioned space.
Also note, at the current rate of climate change Boston is going to be in US climate zone 4 in another 25-30 years.
See also:
https://www.greenbuildingadvisor.com/article/calculating-the-minimum-thickness-of-rigid-foam-sheathing
https://www.greenbuildingadvisor.com/article/are-dew-point-calculations-really-necessary
Dana’s advice is spot on as usual.
In new construction it is easy to avoid spray foam all together. Define your air barrier as the sheathing, seal that and have a blower door done before any interior insulation goes in.
For the roof, why not put 3.5” (R21) of polyiso on the roof deck? With the rest of the insulation being something fluffy in the bays. That thickness of foam is pretty straight forward to screw and finish the edges.
Why were you thinking of using ccSPF on zip r wall makes. Spray foam is actually not awesome for air sealing as there are a ton of joints that are not sealed.
Retrofits may be a reasonable application for ccSPF. I have 3” of Gaco one pass low gwp in my attic that has HVAC. My installers said they liked it because it goes down flatter than any other product they had used.
Matt and Dana..
Roof is already completed so exterior foam not a possibility. Multiple gables and sheds making up the roof and over roof areas so would have been difficult anyway.
If you think that 3” closed cell with mineral wool bibs would work better than r49 closed for roof I could certainly get that quoted.
In terms of walls, I was after the air and moisture ceiling properties then filling with mineral wool which I’m told is less expensive than blown fiberglass here.
Had a bad experience in my current house when I had cellulose in the attic I where the hvac was located I had a huge amount of dust in the house constantly. When we finished that 3rd floor and did closed cell my propane bill dropped by 50% and dust went away. I believe the air sealing made the big difference on energy but the dust turned me off from cellulose. (Maybe unfairly)
Sounds like a blower test pre-insulation is a good idea to find any holes.
In terms of walls the plan had been
Zip 6 + cc 14 + mineral 12 for a total of 32 knowing studs will of course impact that.
Doing just mineral wool would be
Zip 6 + 6” mineral 18 For r24 total with the same impact of studs.
Likely a membrane on top of that.
You guys think I’d be better off with the mineral wool walls vs the hybrid system?
Matt, one more question in your suggestion of doing the blower door test pre-insulation.
I asked my builder about it and he was pretty sure all the soffits would leak like crazy since they aren’t closed off with blocking and insulation at this point. Apologies if it’s a dumb question just trying to learn a bit more
Dave
On the blower door test, the builders comment makes it clear that the exterior was not planned fully to be the air control layer. A blower door test in this case would make sense after the spray foam.
You will need blocking between the rafters at the soffit if they didn't do that yet. This block is way easier to place before the roof sheathing goes on, but is still doable. Make sure that it is installed so foam lands on the top edge of the exterior sheathing. You should see that edge still with the blocking installed so it can be sealed. It common to cheat the blocking in too far. Wood, foam, or even a carefully placed rockwool batt can work.
Was the bottom edge of the sheathing sealed to the foundation on the exterior?
The important thing with the roof insulation is that you fully fill the rafters to limit thermal bridging. With ccSPF the rafters don't get fully filled, which lessens the R value of the rafter. 3" flash and batt, bibs, or ocSPF works well. Depending on the roof design, ocSPF can be used to encapsulate the rafters entirely.
For the walls, anything fluffy will work. Dana says up to R24 with painted wall board. I haven't checked that, but am going to assume it is right. This could be R23 rockwool batts, R21 fiberglass, cellulose etc.
Play with this total wall R value calculator: https://ekotrope.com/r-value-calculator/
These are for the insulation portion of the wall only:
Wall with the ccSPF = R25.7
Wall with just BIBS = R21.7
Using R23 Rockwool batts gets you R24.3
Make sure the drywall is well sealed, this prevents moist air from getting into the wall. Cellulose dust is not a concern if the interior or exterior is well sealed.
Thanks Matt.. super helpful
I ran that ekotrope calculator with the planned wall assembly and landed on R33.6 with the siding, airgap drainage plain, zip r-6, 2" R7.2 ccSPF, 3.5 R4.1 Sprayed Mineral Wood, and BlueBoard and Plaster.
Your comment on doing the blower test post foam seems to be what i'm hearing from the hers raters and insulation companies as well. They are suggestion doing blocking and airsealing, then foam phase, then blower door test, then rock wool.
In terms of the bottom of the sheathing.. The bottom of the zip board was zip taped first. There is stone veneer on the foundation wall exterior so scratch coat and lathe with 3" of stone on it. Above that is a kickout flashing for the slicker max drainage plane, then the first 2-3 feet of zip have the lathe and scratch coat on them as well. Not 100% sure if that seals as well as the liquid flash that we hit the nail holes with.
In terms of the roof was going to be 7" of ccSPF but playing with your suggestion and the calculator looks like 4" of CC with 7.5 of blown rockwool might get my to R52 instead of effective 33.7. Is this what you're thinking about?