Compensating for Walls With Low R-Value

Our new home will be contractor built in Montana. We are looking for feedback and alternative ideas on our insulation plan which may include above grade walls that just barely beat code. Contractors here are not comfortable meeting the R11.25 minimum recommended exterior insulation so we may drop the exterior insulation all together to avoid moisture issues and stick with standard above grade walls with only cavity insulation. If we end up going this route we really want to make up for this in other areas of our home in smart ways. The house has one main level with an exposed walkout basement. Ceiling will be partially cathedral and partially standard attic. Current proposal: Above grade walls – R23 or 24 cavity insulation. 2 by 6 walls with rainscreen and internal vapor barrier/retarder. Likely blown in fiberglass. (Code is only R21 cavity) Below grade walls- R 21+ using 2inches of interior continues rigid foam against concrete walls and then 2 by 4 framed walls with fiberglass or mineral wool cavity insulation. Basement Slab- R10 using 2 inches of rigid foam under slab. Ceiling/roof – R60 blown in cellulose Questions: If we go with R23/24 traditional walls can we make up for some of the thermal loss with insulation elsewhere as proposed above where the contractor is more comfortable? Are there other ways to get better rate of return? Is there any problem with basement walls being about equal or possibly beating above grade wall R values? Thank you.
GBA Detail Library
A collection of one thousand construction details organized by climate and house part
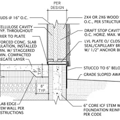
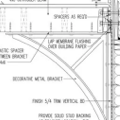
Replies
I often see in the Q&As folks mentioning that builders in their area don’t do this or that, and I wonder who’s paying the bills. There’s plenty of FREE EDUCATION on line, from PowerPoints to videos to full websites dedicated to teach builders how to do things nowadays. IMO, if a builder can’t learn a new building process to secure a job, he/she needs to get out of business and let someone else do a good job which is hire to do.
I design homes in many States that have no code enforcement, or are still in old versions, and yet, I always find a way to instruct those builders with my full set of drawings, and complementing with online or in person education.
Everything in a house build starts with a set of drawings, and to be fair, it does make a difference when you provide the builder with a full set of detailed drawings and specifications. Most drawings I see are a floor plan and four elevations… and you can’t expect any labor to do a good job if there’s no direction.
In CZ6, one of the requirements is to build a wall with R20 cavity + R5 ci. That is about as easy to do anywhere, and if a builder is not willing to do that as minimum, that would be pathetic and shame on them! FYI, if you still don't want continuous insulation, you need to build a wall with cavity insulation for R30 minimum, somewhere in the neighborhood of 8.5" wall thickness... and that brings more problems that installing 1" R5 rigid foam.
You get what you pay for, and if you are willing to lower your standards, you are going to get a less than your desired house.
Hi Armondo,
Thanks for your feedback. Unfortunately, I can't create new builders so we have to work with the experience, views, and techniques that we have in our area or we simply don't build a home.
Contractors here do regularly use 1 inch of exterior foam on 2 by 6 walls but we haven't found one that wants to install exterior foam at a thickness to get to R11.25. Code in our area allows for walls to only have R21 cavity insulation. So we are finding ourselves needing to go with that and beating it by a couple R or go with only 1 inch of exterior foam. Only one inch of exterior foam makes us nervous from a moisture perspective. I would love to be convinced otherwise.
I'll say it again: In CZ6, 2021 IRC TABLE N1102.1.3(R402.1.3) - One of the requirements is to build a wall with 5.5" R20 min. cavity + 1" R5 ci, exactly what you said your builder can do.... OR... Build an R30 minimum wall, 8.5" wall thickness with 2x10 (9.25") plates and staggered studs. That is more complicated as far as building science goes.
Nicko23,
What you are discussing is exactly what energy modelling is designed to do. It lets you see what decisions around each assembly mean for overall efficiency.
Go to 2x8 framing, this is almost conventional and any builder should be comfortable with it. And the energy wizards on this site agree that the thermal bridging is not the concern that you might think it is. With a rain screen it should be a high performing wall.
Thanks for sharing this idea. I am interested in the 2x8 concept but haven’t seen any thorough endorsements or explorations of this. Would love to learn more.
While I share some of the frustration about builders not willing to adopt the latest best practices, as someone living in a small rural mountain town, I know that often options are limited.
In light of that, if one is looking to do trade-offs between envelop components alone, this is a relativity straight forward analysis. You need to know the total surface area (A) of each different envelope assemblies (windows, above grade walls, below grade/basement walls , attic ceiling, vaulted ceiling, etc) and the required/desired U-value for each. The sum of all UxAs for the different required/desired assemblies will give you a whole house UA target. You can then start messing with the the different proposed assembly U-Values to find how much you have decrease the U-Value in one assembly to off set the higher U-value in another. If you had costs per square foot of the different proposed assemblies, you could find the lowest cost solution that achieves the target, whole building, UA.
For assembly U values, I find the Title 24 reference appendix JA4 to be a user friendly source covering many different options: https://www.energy.ca.gov/sites/default/files/2022-08/CEC-400-2022-010-AP.pdf
One last note, for a simplified analysis such as this, I would avoid trade offs between assemblies not exposed to air and those that are. I would also not apply this approach in climates where cooling energy use is significant.
Get better windows and doors. They make a much larger difference on the overall wall performance than adding exterior insulation. https://www.zolawindows.com/post/how-windows-make-or-break-wall-performance-illustrated
We’re building in MT next year and I’ll be DIYing the exterior insulation. Nobody does it around here either. That’s one option.
This is a helpful idea, thank you!
"[Good windows] make a much larger difference on the overall wall performance than adding exterior insulation."
This statement is far too broad. It may or may not be true depending on several factors, including glazing area, continuous insulation thickness, stud spacing, what the U value 'upgrade' for the better windows is, solar insolation, etc.
And then there's the question of cost effectiveness.
I'm not saying don't get good windows but it's not that simple.