Cut-n-cobble/flash-n-batt insulation application

Hello,
Great resource here. Really enjoy the technical information met with real world application scenarios from pros and personal patrons. At the risk of catching flak from veteran users, I am bringing up the much covered topic, albeit new to me; flash n batt or cut n cobble insulation. However, due to time constraints I am looking for some specifics I may have overlooked or misconstrued after researching these techniques.
I am in the middle of a somewhat small remodel of my own house. (2 bedrooms and a bathroom) In my haste to meet a very definite and dwindling deadline, I have found myself in somewhat of a pickle. Normally this part of the job would be sub-contracted, but as most of you probably feel, everyone is behind.
Alright, cut to it, typical story.. Old house in Michigan, (climate zone 6a) true 2×4″ framing. Nothing straight, or plumb, or square, or any of that. Farmboard (clapboard?) sub-siding, etc. etc. There is vinyl siding over old asphalt siding on most of the house. I have re-framed a large part of it. However, the exterior walls I have sistered new 2×4 studs close to level and straight. (approximately 1-1/2″ out at the top most places) In an effort to seal the old farmboards, I started with 1/2″ foil-faced polyisocyanurate cut tight to ext. sub-siding with lots of great stuff around the seams. This was before I had even heard of these techniques, it was simply what I came up with for an “air seal” behind the old sub-siding due to not being able to schedule spray-foam. Before rolling out the kraft faced batts, it dawned on me that I would essentially be creating a moisture envelope within my walls. Which, in turn, sent me down the rabbit hole of diy insulation and led me here.
bottom line:
Will the faced foam board work or should I be worried about condensation? Should I just add another layer? I thought about adding the polystyrene that is supposed to be more permeable, but would most likely be a futile gesture behind the faced foam board. Also losing room for batts, and I am not adding more wood to my already cobbled framing.
Will it matter if the insulation is faced or not? I thought about exchanging it for Rockwool at a premium. I have worked with it before, and it is a nicer product. What is the best solution for the “fluffy” stuff?
Regardless, it will be better than virtually non-existent insulation that was left in the walls. haha!
Thanks for any and all advice!
Thought I should add, I plan to do the exterior of the home within a couple years, which may involve replacing old boards with OSB etc.
GBA Detail Library
A collection of one thousand construction details organized by climate and house part
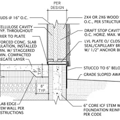
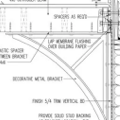
Replies
Thicker foam would be safer as far as interstitial cavity condensation. In zone 6A, at least 35% of your R value should be air impermeable (foam). Look up Building Science Corp's "Hybrid Assemblies".
I would add a little more foam over the 1/2" foil faced if you have the opportunity, and do an excellent job with the air sealing. EPS is more permeable, meaning it has more drying potential and forgiveness, but any scrap foam you have should work.
Netted and blown insulation like cellulose or fiberglass will do an excellent job at filling cavities around electrical, plumbing and framing irregularities. Batts can also work if installed well. All of these allow drying back towards the interior.
On future remodels, I would go full cavity netted and blown dense pack insulation with an interior class 2 vapor retarder and air sealed membrane like "DB+" or "Intello plus" or "Membrain". Much easier to airseal. Or if it must be DIY, kraft faced batts and airtight drywall back-sealed to the plates and rough openings. Or you can reside the whole thing and get your housewrap airtight.
Best,
j
As you seem to have discovered, 1/2" of rigid insulation is not enough in your climate to prevent condensation. I see three options:
1. Add another inch of foil-faced foam, being careful to seal around the perimeters. The general resistance t0 cut-n-cobble is based more on economics than performance. A diligent DIY can make it work, it's just not generally the best production method. Fill the rest with unfaced fluffy stuff (doesn't matter much what kind) and prime and paint the walls.
2. Use a variable-permeability membrane on the interior, like MemBrain, and fill the walls with fluffy stuff.
3. Just fill the wall with fluffy stuff and prime and paint the interior and hope for the best. When you do the exterior siding, plan to add at least 1-1/2" of continuous exterior foam insulation.
Thank you for the tips! I am really enjoying all of the information on this site. And appreciate your time and advice. Believe me, I absolutely loathe this method. I am a carpenter by day; building new construction custom homes 90% of the time. There are a few remodels thrown in here and there with similar circumstances. Feel a bit sheepish asking for advice, but we always sub out the insulation, so I never paid much mind to the science of it. Our company used the same insulation contractor essentially since day one almost 40 years ago, until he retired. Only within the last couple years have there been spray foam contractors in the area. Now it seems to be the number one choice these days. I had them loosely scheduled before the shutdown. Now everyone is too behind, including myself obviously haha.
Upon further investigation, it appears I was confused as to the term "clapboards". The 1x boards are in fact the "sheathing" of old. There is tar paper and a layer of old shingles siding under the vinyl siding. So according to my continued reading of articles and comments on this site, I shouldn't have too much to worry about in theory. Though less than 100% reliable, the felt should act as my WRB and air barrier for now. I can address that when the siding comes off. Most likely add foam to up the R and avoid condensation. For now, I am adding another 1" of foam and rockwool so I can get it in there good and tight. Try my best to get the drywall air tight. (that is usually up to the sub-contractor too) Hope for the best.. maybe r-19 without too much compression?? Wishing I had done a double wall. Or at least 2x6 sistered studs as I have done in the past.
It is funny, I always thought exterior foam was a thing of the past. A lot of houses in this area from the 80s/90s had this and when renovating it always seemed like an antiquated process to me. I sure hate trying to reattach siding to foam. I have never had to do it in new construction. Now I am seeing it is the choice of some top quality builds. So you might see where my confusion is rooted, and why I was looking for some reassurance with a cobbled together mess. I understand the concepts, but when you learn how to do it one way, the other way seems problematic, and/or counterintuitive. It is great to have an open discussion about different ideas and new insight! Does not happen too often on the jobsite without ego in the way. (and don't even mention "green" anything ha) I will continue to nerd out on this building science stuff, and hopefully improve my own skills along the way.
Thanks again!