Cut and Cobble

I’m doing cut and cobble on my attic with 2 inch polyiso and the temperature inside the attic have dropped by 20-30 degrees from before but nowhere near expected.
On a hot day, its about 104F outside and it can be 102-104F inside the attic, and 88-90 inside the house. I was expecting on this kind of days, 85-88F inside the attic. My zone is 3B and the code calls for R5, but I have R13 (2 inch polyiso) underneath roof sheathings.
What was the issue? Some missed spot? Not thick enough? When I install HVAC unit next, will there be a problem under these condition? (planning to run all metal duct without duct insulation).
GBA Detail Library
A collection of one thousand construction details organized by climate and house part
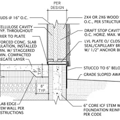
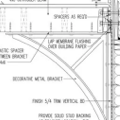
Replies
The thermal bridging through 2" of rafter is only about R2.4, so those extending rafters are basically radiator fins heating up the space.
It would have performed a heluva lot better if it were continuous, mounted on the under side of the rafters rather than cut'n'cobbled.
If you are in US climate zone 3 or lower you can improve the performance a lot by filling the rest of the rafter depth with unfaced high density batts (rock wool preferred), held in place by perforated aluminized fabric type radiant barrier & 1x4 furring 24" o.c. perpendicular to the rafters. For zones 4 and higher some attention needs to be paid to dew point control for thicker fiber insulation layers.
Hopefully there is soffit-to-ridge venting, with at least 1" of space between the polyiso and roof deck(?).
Trojax,
Building codes require a minimum of R-38 ceiling insulation, not R-5, in Climate Zone 3. So your R-13 is nowhere near the minimum code requirement. And, as Dana Dorsett correctly points out, it's always better to install rigid foam as a continuous layer, rather than cutting the foam into narrow rectangles and inserting the foam between framing members.
In cold climates, unvented cut-and-cobble roof assemblies are risky, with many reports of moisture problems. I hope that your roof assembly is vented. For more information, see Cut-and-Cobble Insulation.
Thanks Dana and Martin for the feedback. Dana, when you mention extending rafters, If I understand it correctly...its the space directly under polyiso (about 3 inch remaining), not the exposed wood right?
The roof construction is complex and I wish I have good amount of room to work under there, but I have to maneuver in awkward position most of the time to get the board between the rafter. I was thinking adding 1 inch of closed cell below it on some hard to reach part and add rock wool on parts that i can reach as you suggested.
Why rock wool? Would R13 denim insulation works?
I was thinking using insulation holder instead of 1x4 furring strip. Its much easier, and since this is 1958 house, the rafter not always 24", they are irregular.
Does radiant barrier absolutely needed after I filled the remaining space on the rafter?
Another problem why I choose this method because there is ridge venting but no soffit. The ridge venting doesnt really work, and there is furring strips (1x2) across & above the rafter, under the sheathings. So there is about 3/4" of air space.
Martin, I thought the cathedral/un-vented type construction only need R5 for zone 3? R-38 if you go with conventional way right?
Trojax,
Q. "Martin, I thought the cathedral/un-vented type construction only need R-5 for zone 3? R-38 if you go with conventional way right?"
A. I'm not sure why you have that impression. Some building codes allow reduced R-values for cathedral ceilings -- you can check with your local code enforcement office or building office -- but I've never heard of a reduction as extreme as the one you are proposing. Below is the prescriptive chart for R-values from the 2012 IECC, showing that the minimum R-value for ceilings in Zone 3 is R-38.
.
By "extending rafters" I meant the amount of rafter protruding toward the attic from the foam. Being ~5x more thermally conductive than the foam, all of that surface area of wood in contact with the attic air makes it a heat exchanger, much like a finned radiator.
Rock wool insulation is usually rated as a fire barrier at 3"+, whereas denim insulation is not. If using denim it will need a half-inch gypsum board as a a thermal barrier against ignition, but probably won't if you use rock wool.
If the rafter spacing is irregular you'll have to trim any batt insulalation for a perfect fit. If the rafter bay is too wide, cut the batts in to chunks long enough for a friction fit when mounted sideways.
The PERFORATED radiant barrier (no smooth stuff, no bubble-pack stuff) isn't absolutely necessary, but limits the amount of friable fiber getting into the attic air, and delivers another R1 or so of average performance to the (still sub-code) R value. With R15 rock wool batts compressed into a 3" space the batts will be about R13, so your total center-cavity R is still only R26, not R38. The RB would bring that up to R27- still not enough, but at least something.
If there is not 1" of unobstructed air space between the foam and the roof deck it's a code violation, and the roof deck is more susceptible to rot. What are the roofing materials on top of the roof deck?
Dana, what if I sprayed closed cell foam on that exposed wood (extending rafters)? Would this eliminate the thermal bridging?
Ah I see why Roxul preferred. The reason I preferred denim because it doesn't itch to work with and I would assume better air quality overall....but again, the fire barrier issue...argh! I'm in trouble.
R38 on the ceiling is like about 5.5 inch thick of closed cell, the spray foam contractors here always offering 2 inch and that cost around $8k, maybe because its uncommon to insulate attic this way over here. I wonder how they achieved R40+ using foam under the roof in northern part of the country? the roof material is asphalt shingles. The best way to remedy this might be using SIP but the roof just got replaced about 4 years ago, I wish I knew about SIP that time.
Nothing "eliminates" thermal bridging. Encapsulating the rafters with an inch of closed cell foam would roughly triple the R value of the thermal bridge, but would increase, not reduce the exposed surface area. For every inch of rafter length you currently have 7.5-8 square inches of exposed rafter surface on the interior. If encapsulated with an inch of foam that becomes ~11-12 square inches of surface area.
It's cheaper and better to fill the 3" of space with fiber insulation, which leaves only the 1.5-2" of rafter edge width still exposed to the interior. The exposed surface area is then only about 1.5-2 square inches per running length of rafter, which would emit less heat than the 11-12 square inches of encapsulation surface.
And it still would not bring the roof deck ventilation up to code, and it wouldn't bring the R-value up to code.
Removing the cut'n'cobbled foam, installing R15 fiber flush with the bottom edge of the rafters would give you ~1.5-2" of vent space. Then reinstalling the 2" foam in a continuous fashion would put a solid R13 over the rafter ends, bringing the R value at the thermal bridge up to ~R17 (with no expanded surface area!) rather than the current ~R2.4. The center-cavity R would then be R28, R29 if you count the effects of the foil facers pointed at the attic (or gap to the gypsum board). To meet fire code it would still make sense to add 1x4 furring through screwed to the rafters, mounting half-inch gypsum board onto the furring.
To bring it fully up to code would take another 1" layer of polyiso, making it a total of 3" of foam. At 3" of polyiso the center cavity R would be R19.5 foam, R15 fiber for a total of R34.5-R35.5 which is still less than R38, but with R19.5 of thermal break over the rafters it would meet code (or nearly meet it, depending on the roof stack-up) on a U-factor basis:
https://up.codes/viewer/general/int_residential_code_2015/chapter/11/re-energy-efficiency#N1102.1.4
Thanks Dana. Looks like I'm not done after 4 months, instead I open up another insulation project :(. I will filled up that 3" with probably with denim, furring strip those for future drywall project as I need to jump on to HVAC project next.
Another question I want to ask, on part of the house...the ceiling were actually not dry wall, instead its T&G pine that were drafty and hotter before. So I put down the 2 inch polyiso above that ( 1st and 4th pictures) and then I put a masonite to protect the polyiso.
I didnt know it until recently that you supposed to remove the insulation on the attic floor if you insulate the roof the way I did it. Also on the hallway (pictures 3 & 5), under that 1 inch plywood, I installed R30 denim insulation.
I will be at around R26-27 after I done filling up the rafter, will those 2 things cause another issues?
In almost all cases it's just fine to leave the pre-existing insulation on the attic floor when insulating at the roof deck. That's even more true in climate zone 3B than 4A or colder/wetter.
The insulation on the attic floor does not count (at all!) toward code compliance on R-values, but it's still doing something.
Adding R13 or even R30 (if it actually fit) in the rafters under the R13 polyiso would be fine.
"The insulation on the attic floor does not count (at all!) toward code compliance on R-values, but it's still doing something."
Dana, Can you please explain how this works, from a building science perspective? How does the insulation on the floor impact the thermal performance of an insulated roofline? Thank you.
Emerson,
The purpose of insulation is to slow the rate of heat flow.
If you have insulation on the attic floor as well as along the sloping roofline, the insulation on the attic floor reduces the rate of heat flow through the ceiling. In winter, that means that the attic will usually be cooler than the heated rooms below.
If there is also insulation along the sloping roofline, the insulation between the rafters reduces the rate of heat flow through the roof. In winter, that means that the attic will usually be warmer than the outdoors.
Depending on the thickness of the insulation and the leakiness of the building components, you'll have different temperature regimes resulting from this arrangement. But let's say it's 20°F outdoors. With insulation as described, you could end up with a house at 70°F, and an attic at 50°F.
There are lots of factors that affect these conditions. If the attic air sealing work is imperfect, and outdoor air is allowed to flow through the attic, the insulation installed between the rafters might be almost worthless.
Because the open attic space between the two insulation layers passes air easily it can be a large thermal bypass. Code only counts the insulation layer at the pressure boundary of the house (the roof, in this case), and not any interior partition that's insulated, since the open space between the exterior and partition can be fully conditioned or bypassed by air currents, exchanging air with the fully conditioned space.
But if the ceiling is reasonably air tight between fully conditioned space and attic, the floor insulation in the attic is still providing a very real thermal benefit, even it it can't be counted from a code-compliance point of view. The same is true for a not directly heated less-used room with insulated partition walls from the rest of the house- the exterior wall insulation counts, the partition wall insulation doesn't.
Just be careful, without addressing it, semi-conditioned spaces tend to have humidity problems (large volumes of air near the dew point). A humidity meter is cheap insurance.
Attic temperature is more effected by roof surface temperature than outdoor temperature. Ie, it might be 104F outside, but the surface might be 120F.
If air flowed out your ridge vent, where would it come from (the attic?).