Curious on thoughts about insulation on a new house.
Will be building a house in southern ontario, cold in the winter hot in the summer. Been reading up on insulation techniques, as i like the idea of thermal bridging but hate the idea of trapping moisture in the walls as i have seen some ugly things over the years in renovations and what moisture can do. Im unwilling to put foam board on the outside and vapor barrier on the inside. Just seems wrong. So here is my thought. Build the walls, apply a one inch foam straight to the studs with a layer of plywood fastened overtop with tyvek. Once the walls are stood i would spray foam 2 inchs with closed cell. Then after my wiring is done fill the rest of the 2×6 wall with batt insulation and drywall. Im not worried about the shear strenth of the plywood as i can add wind braces. I think the three inchs of foam would avoid a dew point. Thoughts please! Thanks for your time
GBA Detail Library
A collection of one thousand construction details organized by climate and house part
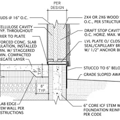
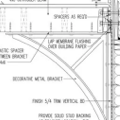
Replies
You're describing a modified "flash and batt" method, which is still hobbled by its downsides: it's expensive, it relies on the least "green" insulation, and it's interrupted (and thus substantially degraded) every 16 inches by a stud. Sometimes it's a good solution, such as in tightening up an old house. But if you're building new, you'll get better results if you can push all the foam to the outside. Substitute a "smart" permeable product for the poly vapor barrier.
The total R-value of the wall you described (assuming you use high density EPS, Roxul batts, R-6 spray foam) would be just over R-28. The Rigid insulation does provide a thermal break but not much of one as the exterior ends of those studs will only be protected by only 1 inch of foam.
Seems like a lot of work (wind bracing) and money (spray foam) for a slightly above average wall. Using spray foam to gain an extra R 3.5 or so likely has a long pay back period from an environmental standpoint as well. (How many btu's are you really saving with that?)
I suspect you could add 3 inches of exterior rigid foam (type II or higher EPS) over the 2x6 studs and sheathing for the same cost as the enclosure that you described. This would give you an R-33 wall with better protection from thermal bridging. From a moisture standpoint, this wall is at least as safe as the one you are considering so long as you lose the interior vapor barrier. (Obviously, be sure to add an air gap under siding in both enclosures.) If code requires a vapor barrier, then slice open the poly once the inspector leaves or opt for a smart vapor barrier like membrain or Intello plus, etc.
I agree totally that the three inches of foam on the outside would give better insulation results its the added time and costs that im trying to avoid such as 6 inch screws to attach strapping, boxes to house windows, installation of the foam itself, self supporting decks. But no means am i trying to go net zero or near. Just a well insulated house without moisture problems. The spray foam expense is minimal to me as i have a friend that will do it for cost because i have provided his company with much work over the years. As i said i agree there are better ways, im more curious if this could be a moisture issue. I've heard the flash and batt has it's issues but thinking the one inch thermal bridge should provide enough to combat that. Also could you give me an example of a "smart" vapour. Thanks
Ontario building code requires your vapour control layer to be on "the warm side of the assembly". Permit reviewers in Ottawa insist that calculations be provided for dew point control if the primary vapour control layer has less than 2/3 of outboard insulation r value. You'd have to run the math, but this doesnt sound like it is acceptable.
https://www.certainteed.com/building-insulation/products/membrain/
https://www.foursevenfive.ca/product/intello-plus/
Good point on the window boxes, etc! Here are a couple of links to the smart vapor barriers that I described. Both are available in Canada.
Thanks for all the insight! Greatly appreciated. Best im willing to do on the outside is a inch and a half, but would rather do the inch for ease of everything else. Is it better to just fill with roxall batts and put a smart vapour on the inside as well as finding the most breathable foam? Need to head to work now but will definitely check out all the links i have been sent after.
Look into Roxul ComfortBoard insulated sheathing, non-structural, available from R5 to R12 (1.25" to 3" thick). I've done one 1960's house renovation project adding Tyvek Commercial wrap (air barrier) with 2" of ComfortBoard, strapped with screws. I designed one new house with 1.25" of ComfortBoard, and one with 3". It's permeable, fire-proof and sound-proof. I'm in Ontario and it's Code compliant. See the "New USA wall" by LamiDesign.
An inch of foam on the outside of the studs isn't much of a thermal break- it doesn't even double the R-value of the framing fraction.
Expensive and environmentally damaging sprayed closed cell foam between studs at ANY thickness is a waste of foam, since it's high R/inch is so severely undercut by the R1.2/inch wood of the framing fraction. Even a full cavity fill of closed cell foam adds less then R2 to the whole-wall R, at high (financial & environmental) cost. Your stackup as-described is still less than R20 "whole wall", after factoring in the thermal bridging of the framing.
At the same wall thickness you can get higher performance at a lower cost out of 2" of exterior polyiso held in place by 1x4 furring through-screwed to 2x4 framing with 5" pancake head timber screws 24" o.c, R13-R15 batts in the stud bays, with the siding mounted to the furring. The plywood layer can be between the foam & studs, and fully structural. Your proposed stackup has the plywood out in the cold, where it it is subjected to exterior moisture drives (and would need to be rainscreened, not just housewrapped) to be reasonably well protected. The 2x4/R13 + 2" polyiso solution comes in at slightly higher thermal performance, and in a southern Ontario climate it would not accumulate moisture over the winter, even using just standard latex paint on gyprock as the vapor retarder (though you may need to install a 2-mil nylon smart vapor retarder such as MemBrain to convince the inspectors.)
Dana have you ever dragged trusses on a 2x4 wall? Not easy to walk. 2 inches of foam would still require a vapour barrier with a 2x6 wall which i most certainly will build, as im building knee walls an prefer more than two inches of bearing for floor joists that are spanning 19 feet. I have resided houses 30+ years old with no house wrap and the plywood has shown no sign of moisture damage. If you side correctly no rain screen is required. As for the environmental issue ill not comment unless you live in a straw bail home, we are all just as guilty. Its ridiculous people bring it up, like rigid foam is a natural resource and not produced in a factory. Lol
If you come to a website with the name Green Building Advisor and ask for input, you shouldn't be surprised if some of the advice is about how to make a house "greener", in addition to more comfortable, efficient, durable, etc. If you have different views, you're free to ignore comments, but you're not likely to encourage people to share their valuable experience and knowledge if you slam the door in their faces.
Your personal experience in working on old houses may be pertinent to a new buiild with different materials and different levels of air-sealing and insulation than were common in the past. Maybe not. If the majority of experts now recommend rain screens for most siding applications, perhaps you should consider it.
I came to a website and got some good information, but never really got my question about moisture answered! I don't feel i slammed the door, but got the door slammed on me, it seems most people want to plug their own ideas without any regard for other ideas, the exterior roxall batts was the only idea that even remotely took my thoughts into context. Sorry not everyone agrees with the yours or others thoughts, but some of us look at it from a building standpoint. Time and pressure. Maybe something you fail to comprehend. Lucky you!
User-6782048,
Q. "I came to a website and got some good information, but never really got my question about moisture answered!"
A. Here is the answer: Your house is located in Climate Zone 6. If you intend to install rigid foam on the exterior side of your wall sheathing, and if you want to avoid moisture problems in your 2x6 walls, then the minimum R-value of the rigid foam is R-11.25 (assuming, that is, that the stud bays are filled with a fluffy insulation product like fiberglass).
If you install only 1 inch of rigid foam (about R-4 to R-6, depending on the foam type selected), you risk moisture accumulation in your stud bays. To learn more, read this article: Calculating the Minimum Thickness of Rigid Foam Sheathing.
I have no idea about your code requirements, but if you don't want to reduce condensation on sheathing with R11.5 of exterior foam, you could build the walls according to "permeable to both sides and more so to the cold side". Rigid foam on the interior side makes this easier.
If you want 1" of foam on the outside and are planning on diagonal bracing for racking, then you could reduce rotting risk by eliminating the plywood.
2x6 plates and staggered 2x4 studs would eliminate some thermal bridging without effecting moisture flow. Strips of foam along studs and plates (on either side) has a similar effect.