Is cross hatching interior of walls worth it?

Hi, I was wondering if it is worth it to cross hatch or “mooney wall” exterior 2×4 walls. I have the opportunity to do it right now during my remodel project. Climate zone 5/6 border with a brick ranch so I cant foam the exterior. Will the added R value be worth it? I was thinking that it would really be beneficial for the large headers above windows. Although I dont know how much 1.5″ of cellulose/foam board on top of those headers will matter that much.
Would I be able to spray stabilized cellulose effectively with the cross hatching there?
Any thoughts?
GBA Detail Library
A collection of one thousand construction details organized by climate and house part
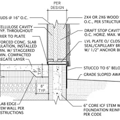
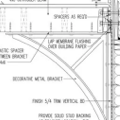
Replies
If you are doing the Money wall type of install, I would aim for more than 1.5". The R value bump from that is not that much, might not be worth the effort.
Your 2x4 wall as is with R3.6/inch insulation works out to R13 for the whole assembly including the brick cladding.
Adding 1.5" of cross strapping to that bumps up your whole assembly to R19.
Going to 2.5" (2x3 on edge) gets you up to an R22, which would drop the heat loss through your walls by almost 50%.
If you want to stay within 1.5", I would go with a continuous layer of polyiso on the interior. This would bump your wall up close to R23.
I would talk to the installer about the spray cellulose. With spray foam, the installers I've used never had issues getting behind 1.5" wide strapping.
If I were to use a continuous layer of 1.5" polyiso, should I still be bothered with furring the entire wall out for the drywall installation or would I just be able to use longer drywall screws?
Im going to assume that I want to use unfaced board so that I maintain some vapor permeability, correct? All I can find for 1.5" polyiso board is faced, any recommendations as to brand of unfaced 1.5"?
Roofing-type polyiso is usually either “felt” faced (kraft paper or fiberglass mat), so it has vapor permeable facers USUALLY. This type of polyiso is also usually a little cheaper, especially from reclaimers. It’s lower density too, and a little bit less R per inch (around 5.7 instead of 6).
The biggest downside of the felt faced polyiso is its more difficult to tape the seams between sheets. Tape sticks awesome to foil facers, not as well to felt facers. If you use the right tape it’s not really a big problem, or you can squirt some canned foam in between for some extra insurance.
Bill
I've hung drywall directly over 2" polyiso. It is not a problem provided you have the correct screws (commercial drywall places stock the longer ones). The problem with directly over the foam is that it is hard to hang things such as shelving afterwards.
Another option that needs less foam but bit more work:
https://www.finehomebuilding.com/2014/11/26/breaking-the-thermal-bridge
Either way you go, remember to bring out your electrical boxes out to the new finished surface. You can re-mount them further out or use device box extensions.
I am using a gas mod con boiler with hydronic floors and ceilings throughout the house. From my rough calculations it would take roughly 10 years to see a return on the cost of materials alone.
As far as insulation for the walls, is cellulose the right way to go about it? Do I want to have an interior vapor barrier on these walls or do I want them to breathe some to allow the brick to dry to the interior as well as the exterior?
ROI sounds about right. This type of energy retrofit is generally not worth it, mostly about comfort.
Cellulose is a great way to seal up building, just make sure your brick details are in good shape. I would read through this first:
https://www.greenbuildingadvisor.com/article/insulating-old-brick-buildings
In colder climate you want an interior vapor retarder, which could be your painted drywall. An interior vapour barrier also works, this is a standard detail in my area (zone 5) even with brick veneer.
More than vapour barriers, focus on your warm side air barrier. You want a well sealed wall both for energy efficiency and durability.
I am also in Zone 5 and I did read that article about brick buildings a few weeks ago. My brick is only 1 layer thick (mostly a veneer) and it has a 1960's style fiber board between it and the wall studs. The drywall will be painted and I know that does cut down on vapor diffusion.
Blown in stabilized cellulose is the cheapest option besides fiberglass (I wont be using FG). I am not necessarily looking for the cheapest option but I also do not want to create a moisture trap or encourage spalling of the brick.
Will the cellulose do the trick or should I be looking at open or closed cell foam? Closed cell would completely prevent any drying towards the interior at 3.5" and also provide the most r/inch. Open cell would allow vapor to pass through (not sure if thats what I want or dont want) and has about the same R value as cellulose but would air seal completely. Cellulose is 1/4 the cost.
I dont know the best route. I have read that spraying closed cell in the walls is a waste of money if you dont address the thermal bridging.
Provided there is a wrb between fiberboard and the brick, there should be no issues with insulating with any fibrous insulation. If you are not sure, you can cut a small opening to see and patch it from the inside.
If there is a WRB and you do a decent job of air sealing, you won't create a moisture trap. The wall should work great weather no matter what you insulate with. Cellulose works quite well as it can buffer and redistribute a lot of moisture which protects the whole assembly.
There is no weather resistent barrier between the fiberboard and the brick. While replacing the windows, old concrete sills and a few damaged bricks around the window openings, this was evident. The brick was put up leaving an air gap between the fiberboard and the brick so I would assume that air gap would act like a rain screen.
I know I am getting off the original topic here but I have read a ton of Joe and Martin's articles and Ive seen talk about vapor diffusion vents in trying to help cure the moisture problems in conditioned attic spaces. From what I understand, the issue is that if a "hot roof" is made, the air in the attic must be conditioned just like the air space in the living portion of the home. Code seems to have a problem with circulating air from the living space to the attic space because of potential fire hazards. Wouldnt the easiest solution be to put a dehumidifier in the attic space? Rather than circulate the air from the living space? Or would this not really cure the problem of humidity because of the temperature differences between the attic and living space?
What about making the air seal between the living space ceiling and the attic floor, more open (less tight)?
I am just trying to be more informed on the topics before I make some decisions.
There is no easy answer with a lack of a WRB. Some fiberboards are rated to be used without house wrap, don't know how common that was in the old days.
Usually the bigger problem with brick veneer is lack of proper flashing details/misssing weep and excessive mortar bridges. If these are not a problem for you, then the existing air gap should work well to keep things dry. If it is not, lot of this becomes a judgement call, no easy answer there.
My only idea would be to staple a layer of house warp inside the cavity to protect the insulation, not idea how well that would work.
As for your other question, best to start a separate thread.
The old mineral wool that was in the walls was not wet or molded so I am going to assume the brick was not staying too wet. The house has 2ft overhangs all the way around so unless the rain is being driven by strong winds, water never really touches the brick much.
I dont think that putting house wrap inside the stud cavities would do much good. Between stabilized cellulose and open cell foam, which would be the better choice? The cellulose is obviously cheaper but I am more concerned with possible moisture problems so I wouldnt mind paying more for the better option.