Critique this approach to insulating and heating, please

I was hoping to get some input on the attached plans, with regard to the building envelope and best approach to heating/cooling.I am building in Morris County, NJ. zone 5a
I like the philosophy of building the tightest envelope and keeping the heating/cooling loads low.I plan on doing a blower door test after framing and before the window/door sheathing is removed for maximum tightness.
Initially I thought of Insulating with 2″ of rigid board on the exterior of the sheathing, from the footings on up, and bat in the cavities (2×6) framing. I spec’d the house out at either 16 or 24″ o.c. 2×6 framing. My thought was the board and 24″ spacing would provide a thermal break and cut down on thermal bridging allowing the bats to bring up the R value.
The question is, From a performance/cost perspective: Should I just go with spray foam? What about just under the roof?
I would be sub-contracting the spray foam out to a separate installer, but would be running the rigid board install myself.
For heating I’m leaning toward a two zone heat pump with furnace back up (gas is available in the street). Admittedly the plethora of options and numerous opinions of have left me confused as to the best way to go.
One more thing: the attached plans went thru one more round of revisions, mostly for exterior aesthetics (although you may catch a ceiling insulation of R30 instead of R38). Also The foundation is being poured not blocked, with 9′ ceilings. Walk out still remains.
Looking forward to you input
Brian
GBA Detail Library
A collection of one thousand construction details organized by climate and house part
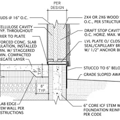
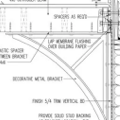
Replies
Brian,
1. Dense-packed cellulose insulation between your studs will usually result in better performance than fiberglass batts.
2. You asked "Should I just go with spray foam? What about just under the roof?" Spray polyurethane foam insulation between wall studs or rafters is usually a waste of money, because thermal bridging through the framing reduces the performance of the assembly. If your plans include an insulated cathedral ceiling, consider installing rigid foam above the roof sheathing. For more information on these topics, see:
How to Build an Insulated Cathedral Ceiling
How to Install Rigid Foam On Top of Roof Sheathing
3. You wrote, "For heating I'm leaning toward a two-zone heat pump with furnace back up (gas is available in the street)." Here's my advice: it doesn't make any sense to install two heating systems. Choose one. Air-source heat pumps are available that can heat your home in cold temperatures without using a furnace for backup; consider using ductless minisplits or ducted minisplits. Alternatively, you can install a gas furnace. Either way will work, but you don't need both.
I would offer that if you're going to install gas furnace as a backup to just get an air handler . A hot water coil could then use a high efficiency water heater as the source . It will cost much less than any high efficiency furnace and the temp of the fluid can be varied based on outdoor temp .
Martin and Richard:
thanks for the quick reply. I attached the plan to this post I'm not sure if the size of the house will change any of the advice given so far.
I am getting a quote on dense-packed cellulose.
There is a small cathedral ceiling on the first floor. I will include rigid foam above the ceiling as suggested. Thanks for the link.
I take note on not installing two systems. don't know why i would want to install two systems?
I will look further into the air-source heat pumps and the air handler.
i like the idea of mini-splits, but can't get my wife to get past the sticking point of their aesthetic in each room...maybe the ducted-minisplts will.
Q: If hydronic heating is used, what is the gba preferred method of cooling? Hydronic cooling?
Brian,
In areas of the country that require air conditioning -- most of the country -- hydronic systems don't make much sense, because it's complicated or impossible to cool a house with hydronic fluid unless your climate is very dry.
The usual heating and cooling systems for areas that need both are:
1. A system using forced-air ductwork (usually a furnace or air-source heat pump for heating, and an air conditioner or air-source heat pump for cooling), or
2. A system using ductless minisplits or ducted minisplits for heating and cooling.
The shape of the footprint of this house has several inefficiencies due to the large number of corners from multiple bump-outs. Assuming 16" on center framing the corners increase the average framing fraction to over the average-home's ~25%, maybe even over 30%, which cuts into the "whole-wall R" performance. Having multiple bump outs also increases exterior surface area (where all of the heat loss is happening) to conditioned space floor area. You'd literally have a lower heat load with a bigger house if you pushed out the other walls to match the planes of the bump-outs, since that would lower the exterior surface area, as well as reduce the thermal bridging of the framing.
Having multiple heating systems as backup is a bit silly. From a marginal heating cost point of view better-class modulating air source heat pumps are comparable to condensing gas, and if your heat load is within the output range of mini-ducted cold-climate mini-splits (probably is) one or two ducted mini-splits (one per zone) rather than a 2-zoned larger single heat pump would probably be the best compromise on cost/efficiency. The reason you would install two systems (assuming they can be right-sized for the zones), is that controlling zones with duct dampers increases the air-handler driven air infiltration cutting into overall net efficiency, and that mult-zoned mini-split technology has mini-mum load issues for the compressor, making the compressors oversized and less efficient when serving just one zone. Right-sized modulating systems would be running in modulating part-load condition throughout the middle of the heating season, and have minimal on/off cycling during the shoulder seasons. It's often cheaper to go with two smaller mini-splits than a 2-zone multi-split too. The latter may make sense when the smaller zone's heat load is well under that of the smallest single-zone mini-splits.
The high initial cost of a heat pump compared to condensing gas is real, but if you were planning separated air conditioning systems the combined costs of the mechanicals can still favor a mini-split approach (mini-ducted or ductless.)
It's premature to lock into any heating approach before carefully calculating the heat loads of the zones though, using realistic indoor & outdoor design temps. For higher-performance houses it's usually far better to let a qualified energy nerd architect/engineering company run the load calculations rather than contractors, since the latter have less experience with high-R houses, and have a lot of built-in presumptions and anxieties that inevitably causes them to oversize the equipment, often by more than a factor of three for a house like yours. When you run that heating load you'll probably find that the total load is less than the smallest-of-the line gas furnaces, in which case a hydro-air + water heater approach recommended by Richard might make sense, but you'd still be looking at finding the right air conditioning solution as well.
With a properly air-sealed & tested sheathing and 2" of exterior foam, damp spray cellulose has about the same thermal performance as dense packed, and is usually cheaper. Damp sprayed goods are lower density and thus less air-retardent than dense-packed, but it's still VERY air retardent compared to most batt-products, and won't have any compressions or voids for convection paths. A slightly higher-R alternative would be 1.8lb density damp sprayed Spider fiberglass, but that's usually a bit more expensive, and at YOUR framing fractions the improvement in whole-wall performance for that upgrade would be academic. (If you were doing 24" o.c. advanced framing with few corners it might add about R1.5 to the whole wall performance.) Open cell foam cavity fill would automatically air-seal the cavities, but not between doubled up framing or the seam at the bottom plate etc. If it comes in cheaper than cellulose (might be in some markets- I've seen it more than once) it's not terrible way to go for the wall insulation when performed by a competent installer. There is NO case to be made for closed cell foam anywhere in your stack up. A full cavity fill of closed cell foam would add maybe R2 to the stack up, at significant financial & environmental cost, a performance margin that could be exceeded with an additional 1/2" of exterior foam at a much lower initial cost (environmental & financial.)
Brian,
What kind of hydronic heating are you referring to ? I heard no mention of hydronic heating . Are you referring to the hydronic coil approach ? Do you plan on installing a DOAS system in this home ?
Please read the following , they will help you immensely and possibly explain some of the viewpoints of the many . i don't think anyone can downgrade Mr. Beans credentials . The most important question that you must ask yourself is , "what is important " , It's a question that is so often forgotten because some think they already know the answer . Out of fairness I will rebutt that hydronic cooling does not make sense . It has very successfully been done in the most MOIST regions on the planet . Look up VAV vs. Radiant , side by side comparison . This is a 3 year study which includes first cost performed by Infosys . They are now changing all their buildings since it makes the most financial SENSE tright down to first cost .
Taken From Healthy Heating
" The #1 message here is - if we begin with occupant needs underpinned by the unadulterated definition of sustainability, using indoor climate engineering to establish indoor environmental quality - then the end game will result in the coveted high performance building everyone is drooling over. Even though this approach has immense benefits for contractors, designers and consumers alike it is not a trivial undertaking because it involves the busting up of egos and tradition.
So let’s first establish, by ethical requirements professionals must agree buildings at a minimum should limit the probability for occupants to become an OSHA statistic; this includes undesirable effects due in part to poor quality of air, lighting, sound, odor, vibration and thermal comfort. [2]
Secondly, the combined building, mechanical and electrical systems should meet or exceed those efficiency standards which are mandatory at the time of construction (or heaven forbid to a higher standard on a voluntary basis - he said somewhat sarcastically). Look it’s a good thing if the architect and her/his client have an obligation to the principles of earth stewardship and if so, then the principles of efficacy[3], entropy[4] and exergy[5] must then be included alongside the evaluation of energy efficiency; a principle I have labeled as an E5evaluation[6].
http://www.healthyheating.com/Begin-with-the-end-in-mind.htm#.VVDR0ZMQjm4
http://www.healthyheating.com/DOAS/DOAS_Introduction.htm#.VVDSPZMQjm4
http://www.healthyheating.com/
As a new member I have to first say that the response time and quality of writing is tremendous!
Dana-I understand footprint negatively effects heat load, However lot requirements and occupant design constraint dictated the shape of the structure, w/ the local real estate market influencing (increasing) the size. At this point it it what it is. Given the less then optimal footprint and sun orientation I am trying to create the highest performance house i can from here on out.
The house is spec'd out at 24" o.c w/2" of rigid board on the exterior. Hopefully this thermal break and reduction in thermal bridging combined with proper air sealant will raise the performance of the home.
With regard to the multi mini splits vs zoned. Thank you for the explanation.
I agree it is both "premature and best left to the pro's to lock myself into any heating approach at this point" i have reached out to a couple of company's and am awaiting contact from them. By posting the plans here (and reading pertinent articles) I was hoping to beef up my background info on the subject before sitting down with an expert. I have a solid background in the building trade, but freely admit I need more schooling in the building of a high performance home.
I will be testing and expect to have a properly sealed sheathing plus foam. I will look into the damp vs dense cellulose vs open cell cost/performance comparison.
Richard-sorry for the non-sequitur about hydronic heating. and Thank you for the links. The quotes you pulled ring true to me and i look forward to sitting down and reading the links you posted as well.
B~
Expert is a strange word Brian . Tread carefully up there in Morris County . Lots say they are experts , I follow up plenty of them . Call Reissmann in Chester . Derrick will know the real quality contractors up there .
Might be a good idea to contact David Butler from Optimal and investigate what he may help you with . He also vets your contractors for you to install his design .
Assuming the 24" o.c. stud spacing brings the framing fraction down to about 23% even with all the corners, with cellulose cavity fill you're looking at a whole-wall R of about R14.5 for whole-wall performance before adding in the exterior foam. (With a full on advanced framing design it would be about R16.5) Adding 2" of Type-II EPS (R 8.4, about a buck a square foot when you include the furring and fasteners) or 2" of rigid rock wool it brings that up to about R23 whole-wall, which isn't a bad wall for a zone-5 location. For running a quick & dirty spreadsheet heat load calc for equipment sizing purposes, use U0.042 to U0.045 for a U-factor for wall area for that non-standard stackup- it'll be somewhere between those numbers, and the window losses will probably exceed the wall losses, so the total error won't be large.
There's a long term rationale for maybe R30-ish whole wall performance, especially at the higher exterior surface area of the bump-outs which cold be had by going to 3" foam consisting of 1.5" polyiso (R9-ish nominal, but R8.3 after derating for winter temperature) next to the structural sheathing, and 1.5" of EPS (R6.3 nominal, R6.8 after uprating for winter temp) on the exterior of the polyiso layer.
The plans show no foundation insulation. IRC 2012 code-min is R15. (http://publicecodes.cyberregs.com/icod/irc/2012/icod_irc_2012_11_sec002.htm ) Since it's a poured foundation you might consider using insulated concrete forms and aligning the plane of the above grade wall foam with that of the ICF foam. With 1/2" sheathing and 2" of foam sheathing, with a 2.5" + 2.5" ICF (the smallest available from some vendors) that means putting the edge of the framing bottom plate directly at the edge of the foundation, with the 1/2" sheathing overhanging the ICF foam. This makes for a very good thermal break at the foundation sill, and you can skip the sub-floor insulation. To keep the basement slab dry enough to avoid summertime mold on anything put on the floor, adding 1.5-2" of EPS under the slab is also worth it. Put a 6 mil polyethylene slab vapor barrier on top of the slab foam, not under the foam. With an ICF wall the interior side EPS continuous with the slab EPS thermally breaks the slab from the footings as well, which keeps the slab edge warmer & drier year round.
For mechanical support reasons you won't be able to set the lally columns on top of the foam-insulated slab, so just extend the footings for the columns up to slab-level, and isolate them from the slab with an inch or two of vertical EPS to limit the thermal bridging there as well.
Brian
I noted a few things that need modification:
1. Add Insulation and vapor barrier under the cellar slab
2. Add Cellar wall foam insulation
3. Use Raised heel roof trusses
4. Be sure to eliminate thermal bridging at the floor, walls and roof of the bonus room over the garage - these spaces have six "outside" surfaces; more than any other space in the house so need a lot of detailing so they can be easily useable.
I've also found that the visual aspect of mini splits are the most controversial thing about them, but as a builder for several decades I've never seen any system that was as inconspicuous to use (very little noise, low air volume), as easy to use, and create as comfortable spaces as these. One of the many advantages is that unlike most furnaces and boilers their electronic motors can maintain the temperatures right around the set point rather than fluctuating high & low. I heated with my oil furnace and propane boilers last year, and my new mini splits this year and was more comfortable than ever. All of my clients, even those with initial misgivings love the steady, quiet heat & AC. The fact that we'll be able to make our own fuel and not be subject to fuel price increases is a huge bonus.
Here is a product that is very well suited to the application for the basement slab . Remember to do all the math and not just product cost . Plastic vapor barrier is not cheap and it's a PITA . Less seems is also a good thing .
http://thebarrier.com/pdf/brochure.pdf
Be careful when specifying insulation that comes in a roll. These thin products have a very low R-value. Barrier HL has an R-value of only R-1.1, and "The Barrier" has an R-value of only R-1.4.
I should have stated I was referring to X5 as part of a rated assembly similar to their tested spec . The X5 material alone is only R5 . The vapor barrier and lack of seams make this product a very good material to use under a slab .