Crawlspace Vapor Barrier

Hi.
I have a crawlspace that’s attached to the part of the house from 1900s. There are two access to it, one from the basement and the other from the outside. The outside access used to be a vent. Couple of years ago, we laid down a thin layer of concrete on the floor and close the outside access. I was thinking of laying a 6 mil vapor barrier down. Based on the pictures attached, how far up should the concrete blocks should I go?
As you can see in the pictures, on the cinder blocks, there are cores (open holes), should those be covered so there’s no vapor transfer?
How should these be filled or covered?
Thank you!
GBA Detail Library
A collection of one thousand construction details organized by climate and house part
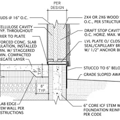
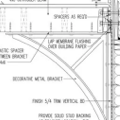
Replies
If you have untreated wood touching concrete, be very cautious about making the concrete wetter. Some good info here.
Gentlemen, any advice would be appreciated regarding the filling of the cores. Maybe pour sand down there or just foam it up?
Hi all, I was going to fill the cores (open holes) of the blocks with sand. The sand is a little wet from being outside in the rain. Do you think it'll be okay? At least, it will help to stop the vapor transfer.
Thank you in advance for your input.
I recommend this article:
https://www.buildingscience.com/documents/insights/bsi-009-new-light-in-crawlspaces
Basically he recommends that crawlspaces should be fully open or fully closed. Fully open means no more than half of the side walls covered. Fully closed means sealed and insulated like the rest of the house. If they are partially open they will be damp, as they won't have enough airflow to warm up in summer but there will be enough airflow for humid air to get in and cause condensation.
If it must be partially open then the wooden parts need to be protected against moisture. He recommends foam board below the joists but spray foam works too.
You have to figure out what you are trying to achieve, and why. Sealing the floor will stop the ingress of soil gas and water vapour, for health and building longevity reasons. It looks like this will be a difficult task in your situation.
The moisture that is wicking up your concrete blocks is not water vapour, it is liquid water moving by capillary action. You will not be able to stop this by pouring sand into the cores because sand is vapour open, and also great at moving water by capillary action.
Thank you for your advice. I got 40 lbs of sand for nothing..ahh.
How about filling the cores with great stuff spray foam?
What is your desired outcome? Is there a specific problem you are trying to fix?
Well. I was trying to lay a vapor barrier down in the crawlspace to the side of the cinder blocks. But wasn't sure what to do about the open cores of the cinder blocks.
So is great stuff can a good option?
Looking at the pictures, water is wicking into the wood framing. Unless that framing is all pressure treated* you need to keep that from happening. What you need is called a "capillary break" -- wicking is technically "capillary action." Something like this:
https://www.homedepot.com/p/Owens-Corning-FoamSealR-3-1-2-in-x-50-ft-Multi-Use-Ridged-Sill-Plate-Gasket-1FS/202084452?source=shoppingads&locale=en-US&&mtc=Shopping-B-F_D22-G-D22-022_004_INSULATION-NA-NA-Feed-SMART-NA-NA-New_Engen&cm_mmc=Shopping-B-F_D22-G-D22-022_004_INSULATION-NA-NA-Feed-SMART-NA-NA-New_Engen-71700000076017798-58700006490415250-92700066966870867&gclid=CjwKCAiAh_GNBhAHEiwAjOh3ZCftp17Fl_lvNPoLaq2KnZunWzVW1rEKxS73GEqShM1ImsmXFeTUGBoCm5IQAvD_BwE&gclsrc=aw.ds
Now here's the hard part: you need to get it between the masonry and the wood. Which means you need to jack up the side of the house, just a tiny bit, maybe a quarter of an inch, to slide it in. Which isn't actually that hard, you just need to have some house jacks. Which around me can be rented for around $10 a day, each.
I can't tell from the pictures how the sills are sitting on the block but it doesn't really matter, the capillary break just needs to keep the wood from touching the block.
Vapor barrier does absolutely nothing to help with capillary action. There's no cure other than getting a barrier between the block and the wood.
*(And maybe even if it is all pressure treated).
Hi. Thank you for your reply.
I think that little condensation spot you see there has been since the blocks were laid there about 100 years ago. The wood is not pressure treated. The rim joist are actually higher up. The wooden sheathing you see there is actually for the siding. There's stucco on the outside.
Please see the picture of the inside and the outside.
If the stucco runs continuously from the block up across the kneewall, then getting a capillary break in there will be very hard. If the stucco is only on the block, then jacking the wall and inserting a capillary break will work just fine. Someone on this list has been recommending .060" thick HDPE. I have not tried it yet, but I love the idea. HDPE is tough, slippery and vapor-proof. You cut it to the width of the block, and work with sections about 4' long or so to make it manageable. Your floor vapor barrier can then run up the block wall right to the HDPE sheet and the two can be taped together with one of the super-sticky European tapes.
I'm not sure why you want to fill those holes. Sand isn't really going to do anything, and it would take a LOT of canned foam to completely fill them. If you just want to block off airflow, stuff a little mineral wool or some chunks of rigid foam in there as a backer, then put some canned foam over that to seal it. I wouldn't try to completely fill the cavities in the block with canned foam.
I'm the one that always recommends HDPE sheet, and I like it because it's still and slippery, which makes it easy to slide in. I like to use 1/32" (0.032") sheet though, which is a little cheaper than 0.060" sheet and works just as well.
What I like to do is to have the platic supply house cut the HDPE shet into 4' long strips for me the width of the top of the block plus 1/2", then form the 1/2" extra over to make a 90 degree lip. This makes the installation very easy -- jack things up to open about a 1/8" gap between the sill plate and the top of the masonry wall, slide the HDPE sheet in until the lip is evenly against the block (facing down) along the entire length. Move over and repeat the process for the next 4 foot strip, leaving about a 1 or 2 inch overlap between sheets. The lip makes sure that you can get things installed all the way evenly down the entire length of the wall with no need to measure or do anything with precision while you're crawling around in a crawl space or other not-so-nice place to be working.
BTW, I prefer to use black HDPE since it's more UV resistant, and it's usually less visible in any gaps. Standard sheets are 4x8 feet just like plywood, but ask your supplier if they have any leftover that they can let go cheap. They love selling "drops" that are oddball sizes, so you can often get a better price on those if they're available. Most of the plastics supply houses can do limited fabrication too, such as shearing strips and often forming simple bends on a strip heater too.
Bill
Thank you so much Bill and Peter.
The stucco does run continuously from the block up across the kneewall. The real foundation for the floor joist is the higher brick wall in the picture.
I will definitely try the mineral wool and canned spray method. Thank you again. This was helpful.