Crawl Space coversion from vented to non-vented

I am getting ready to begin insulating, sealing, and encapsulating the crawlspace under my house that I am renovating. The current space is vented and I will be converting to unvented / conditioned space. I have already completed the roof side of my work to unvented.
The house is wrapped with 2″ of polyiso along with another 1/2″ layer to get a good air seal on overlaps. R15. I will be insulating with air permiable the interior stud walls according to code for a combined R30.
The polyiso and siding extend below the sill plate and cover about 2″ of the concrete foundation. The concrete extends down another 6 to 8 inches before there is dirt. See attached diagram.
I will be putting foam board along the concrete inside the crawlspace and then air sealing the entire space with 12mil vapor barrier. The crawlspace will be dehumidified as well as have vents to the main floor inside the house. I will also be adding a passive radon system for code purposes as part of the process. (in case someone comments on this).
My question:
Should I leave the space where the sill timber is alone and not put any insulation there to allow this to dry inward? My thought is not to seal this for that reason. If I want to insulate should I just put in some rockwool for added insulation?
I am zone 5, 2000ft, not a high snow area. High prairie in eastern WA.
Any thoughts will be helpful. I plan on starting this in a few weeks.
GBA Detail Library
A collection of one thousand construction details organized by climate and house part
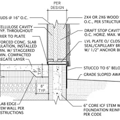
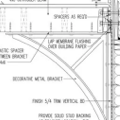
Replies
If you're in a termite zone, you'll want to leave an inspection gap at the top of the block, and just below the timber piece. That could double as a "drying area". I would still make sure to air seal the rim joist area, which in your case would include that timber piece. You could still insulate the timber/rim joist area though (see below).
If you're not in a termite zone, I'd be sure to insulate that area. Do you have a capillary break on top of the masonry under the timber? If you don't, I'd consider adding one. To add a capillary break, you need to jack up the wood structure a little (~1/8" or so), then slide in a material suitable for the purpose -- I like to use 1/32" HDPE sheet for this since it's fairly stiffed and slippery, so it's easy to slide into a small gap. A capillary break will greatly reduce the chances of moisture issues with the wood that you want to insulate.
The most vapor open way to insulate that timber and rim joist area is with EPS rigid foam panels, which is what I did in my own home since the exterior side is foil faced polyiso with zero drying ability. You can secure the EPS panels in place with canned foam around the edges, which will also help to get you a good air seal in this area. You do not want to use any type of fibrous insulation since you run the risk of moisture migrating through and condensing on the wood structure underneath, which will lead to rot and mold. Whatever type of insulation you choose needs to be something that will not allow for large amounts of moisture migration, which pretty much leaves rigid foam and spray foam as your only options. If code in your area requires some fire protection for the rim joist insulation, you can use mineral wool batts for that, and to also gain some R value, as long as you have a sufficiently thick layer of rigid foam against the rim joist itself. I usually use the slightly thinner (3") "Safe'n'Sound" mineral wool for this purpose.
Bill
Thanks Bill,
Not sure I can get a slip sheat under these timbers. Won't know for sure until I get into the project. The rest makes sense and I appreciate the suggestion to use EPS on this.
Ron