Craning an Assembled Roof Onto Walls

Location: Nova Scotia, Canada (Zone 6 lite). Building dimensions: 22′ x 32′. Roof: 7:12 Gable
Has anyone partially / fully built a trussed roof on the ground and hoisted it onto the walls? Any learnings that you’d like to share? I’m considering this for a current build as I have plenty of flat space and an aversion to being up 25′ in the winter. The truss manufacturer will not comment on the best pick points for such a lift, unfortunately.
Specifically, I’m curious where and how to best hoist this roof. The interior vaulted ceiling is a 3:12 pitch. In an ideal world, I can sheath and (mostly) install the metal roofing, leaving only the ridge exposed for strapping to be lowered to the bottom cord.
Any feedback is greatly appreciated. It seems that this is common practice for some folks, but there is not too much online in terms of best practices.
GBA Detail Library
A collection of one thousand construction details organized by climate and house part
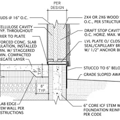
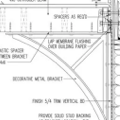
Replies
I've done what you're describing... I would just throw a couple 2x10 on either side of your middle king post on your truss tight to the top and lots of 2x4 bracing. The tricky part is going to be making sure you measure and square everything pretty close to perfect. I would build my floor and then build the roof on the floor, then crane it off, build the rest of the house before craning it back on. I've done this and know others who have as well and it worked great. It ensures your roof will fit. Talk to your crane operator beforehand, they usually have experience with it, plus you want to make sure you're OK on weight. Good luck!
Thanks, ashleighsell. This is a two story build, so framing it on the floor has a bunch of issues. But, I can see why that would be a great move on a 1 story house. Good to know I'm not alone in doing this!
Deleted
Habitat for Humanity has done this a few times at the Jimmy Carter Work Project blitz builds where volunteers build the houses in a week. It allows them to put one group of volunteers on the wall framing, and another group next door on the roof, and keeps the roof group from having to work so far from the ground - safer for volunteers. You need a flat place to assemble the roof, so they often do it on an adjacent slab for the next house.
I'm sure you can find some videos around of the cranes lifting the roofs. [ETA: Here is one link - there are dozens of others https://www.southbendtribune.com/story/news/local/2017/11/10/roof-raised-on-first-carter-work-project-home-in-mishawaka/45805977/ ] I seem to recall them saying the truss mfg took the hoisting loads into account when designing the trusses. I recall they mark 4 leave outs - 2 on each side about 1/3 of the way down from the ridge and each about 1/3 of the way from each end. Otherwise the roof gets finished on the ground, all the way up to and including the ridge vent.
Thanks user-5946022. I have seen a few videos with the leave outs like you describe. Makes sense. Makes more sense for shingles. Since we're going with metal roofing I'd prefer to send the rigging down through the ridge vent, if possible.
You should look for "Ontarioframing"
He posted a story a few weeks ago framing a whole garage on the ground in about a day and lifting it up the following day, pretty wild.
https://www.instagram.com/reel/CzXa9QmrUgS/?igshid=ZWQ3ODFjY2VlOQ==
Very cool. If we were on one story I'd probably copy this assembly exactly. Unfortunately we're two stories so that changes the calculus.
I'm very curious about your plan, but I don't have much to offer you other than a few non-expert comments:
I like the post #1 idea for building the roof on the floor and then craning it off. This makes a lot of sense, but you would need a crane twice. This still may be cheaper than finding a way to build the roof elsewhere... just need to weigh the costs and other aspects.
Maybe look into a different truss manufacturer? Maybe the trusses need to be engineered slightly different for such an application? I'm sure there is a liability for the truss manufacturer but this sort of thing is done quite often (modular homes). Maybe they can provide pick points / lift recommendations with a waiver?
Perhaps call around to a few crane / rigging companies to see what they need and get some estimates? Run some quick calcs for your estimated roof weight beforehand. They may have some max lift #'s and rigging requirements that need consideration. They may be able to steer you to an engineer or truss manufacturer that they have worked with previously.
Good luck! - post updates
Edit: Found this great thread from JLC. Lots of good info.
https://forums.jlconline.com/forums/forum/jlc-online-expert-forums/rough-framing/45435-planning-a-craned-in-roof
Excellent thread! Good to know I'm not alone in wanting to do this.
I thought there was a clever and non-obvious comment by ChrisInman in that thread:
"My plan is to basically build a raised platform about two feet high as a mirror image of the top plate just next to the building. Assemble the roof right on top of that platform, as though it were the actual top plate."
I think by "platform" he just means a supported 2x6 following the perimeter of the building. If you think about it, that's all you need to assemble the roof.
Usually when I've seen this done they use prefabricated components. They don't build the roof from sticks, but from pieces. There may be some assembly on the ground but they're starting with a house that was designed to be craned together. So the crane does all the walls and then the roof, usually in one day.
Take a look at FHB editor Brian Pontolilo's build, which he describes in his post, Thoughts for Owner-High-Performance Builders. His assembly provided a place to stand when setting the craned trusses into place.
Thanks all for the good feedback. I'm feeling better about going with this approach. It helps that I've found a crane operator who has done this several times. Will post back updates when it comes time to lift.
Latest lift / rigging design. I welcome any feedback.
Ry_Buc,
The trusses are engineered to bear on their raised heels. I think the the closer you can get to mimicking that the better.
Thanks, Malcolm. I'll have a think about how we might accomplish that. Leave outs likely, which negates some of the value of doing it on the ground. But maybe a more structurally-sound approach.
Ry,Buc,
With a snap-lock metal roof you can still leave several panels screwed down but not snapped to their neighbor, which would provide access for lift points.
I wouldn't take advice from anyone here, I'd see if the truss company engineers can help.
It's possible to stress an assembly in such a way that it shows no visible damage but it's been weakened.
Fair point. I'm taking advice from a wide swath of folks to vet the idea. Unfortunately, the truss manufacturer won't say a word on the matter. Liability.
Seems reasonable, but the only reliable way to determine the suitability/safety of the rigging plan is with engineering analysis.
Otherwise my $.02: for extra safety, maybe find a way to attach some high tensile steel strapping from one eave to the other over the peak to better counter the vertical forces at the ridge. (basically extend the blue strapping you have sketched)
What's the estimated weight of the roof assembly?
Conservatively 5500 lbs.
Maybe the pictures here help a bit:
https://bygghouse.com/wp-content/uploads/2017/02/Summary-of-Swedish-Wall-Element-Construction.pdf
We just did this last week! We are on a hillside and the roof is quite tall, so nobody wanted to work at this height. It was built on the ground raised up as someone described above. Hoisted up in 2 halves.
I am not an expert but what they did for ours was strap around the piggyback portion of the engineered trusses, and they left the ridge vent cap off so the strap could come through the top. Seemed to work pretty well and after a couple hours - there is a roof! I trust that it was all fine because our project manager is technically a structural engineer, but you should definitely talk to your engineer about this.