Countersink 1×4 strapping

Hello,
I am building my rain-screen with 1×4 strappings to support 1 1/2″ foam and James Hardie sidings. I will be using FastenMaster Headlock 6″.
The screws need to be countersink into the strapping. The head is 5/8″. I can not find a countersink drill bit set that is over 1/2″…
I can use a 14 drill bit with a countersink in 1/2″, then finish with a countersink in 5/8″, but this is really time consuming.
How are you guys preparing your strappings?
Thanks
GBA Detail Library
A collection of one thousand construction details organized by climate and house part
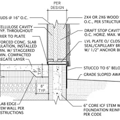
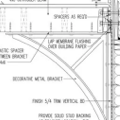
Replies
Maybe just a forstner drill bit slightly larger than the head size? or even a spade bit?
I am going to reply to myself. I have watched a video and the person is using spade bits only. Is that enough?
I thought the screws needed to be countersink to avoid cracking because of the tension of the screws and nails of the siding....
You can get bigger countersinks, you just have to get them from machinist supply places. I really like the zero flute countersinks since they don't chatter. I have a nice set from MA Ford. There are other manufacturers. Here is a 3/4" diameter zero flute countersink:
https://www.amazon.com/KEO-53514-Single-End-Countersink-Uncoated/dp/B00947BSQ0/ref=sr_1_16?crid=145IRYEO7RAK8&dchild=1&keywords=zero%2Bflute%2Bcountersink%2B13%2F16&qid=1635373289&sprefix=zero%2Bflute%2Bcountersink%2B13%2F16%2Caps%2C110&sr=8-16&th=1
Make sure the cutting angle of the countersink matches the angle of the head of the screw you're using.
Bill
Thank you all.
It seems I mixed up pilot hole and countersink hole. Pretty sure I read pilot holes were necessary to avoid the strapping cracking under the force of the structure screws and nails, can't find this article anymore...
It seems everyone is doing countersink hole only. I will be using a spade bit for this project.
Cheers
I've never countersunk strapping screws.
Get roofing deck screws (used to attach rigid insulation for a flat roof), these have a flat head and will get sucked into the strapping enough to be flush provided you hit your studs. They are also WAY cheaper than any of the fancy screws.
https://www.iko.com/innovi/document/6300002-013-pds-iko-innovifast-ap-fasteners-en.pdf
If you're using 1x4 spruce for strapping, those heads will pull flush or close to flush.
But honestly, why do they even need to be countersunk? This is the sort of fussy detail that makes people abandon things like rain screens.
They'll sunk flush if you're using XPS, Polyiso, or EPS, in clear wood without a knot, and driven straight.
With mineral wool this isn't the case. Using a bugel headed screw that self countersinks works there, but sucking a huge washer head flush will pull in the furring strip enough to see light under a straight edge.
For others reading this, consider plywood strips to avoid any splitting. Or maybe AdvanTech for increased rot resistance?
Do some testing (make a test buck out of some lumber scraps) to see if the heads will actually pull flush, or close enough to not matter.
I would try to avoid having to make a counterbore if possible, because that's a lot of extra work.
My experience is that a pilot hole helps to aim the screw so as to hit the stud. Especially important if you're anywhere near a knot. I was using 3" of insulation so just a little angle and I was off. The pilot holes also keep me on an even pattern. Perhaps a spade bit with a long pilot tang would be sufficient.