Cost-effective insulation approach for unvented attic retrofit?

Looking for the most cost effective way to increase the insulation in my attic.
Some info on the house:
-Single family ranch approx 2500SF, built in 1970s, upstate NY CZ 5A
-Vented attic with fiberglass ceiling insulation approx R-30
-Central air handler and ductwork located in attic
-Stick framed roof
I’m thinking of possibly fastening foil-faced rigid foam to the rafters. Preferably do not want to deal with cellulose or anything messy as there is no real air barrier and the attic is used partially for storage.
Any feedback would be greatly appreciated!! Thank you in advance
GBA Detail Library
A collection of one thousand construction details organized by climate and house part
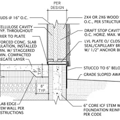
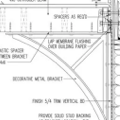
Replies
For that to work it has to be air-tight and there needs to be soffit to ridge venting. If attic air can convect around your rigid foam, it will.
How deep are the rafters?
Thats a good point, thanks. I believe they are 2x8
User-7166101,
First of all, can you tell us your name? (I'm Martin.)
For a thorough discussion of this issue, see "Creating a Conditioned Attic."
Note that the most cost-effective solution to your dilemma may be to abandon the attic air handler and the attic ductwork, and to replace them with one or more ductless minisplits.
To adequately insulate a 2500' rancher at the roof deck is likely to run north of 20 grand if you hire a contractor, and the better part of 10 grand of that is going to be re-roofing.
But if you're ready to re-roof and it's a fairly simple roof design such as a simple gable, without many valleys, installing 3.5-4" of reclaimed roofing polyiso and a nailer deck atop the roof deck, and R28-R30 Rock wool batts in the 2x8 bays might come in cheap enough. That's going to take about 80-90 sheets of 3.5-4" foam, but to make the math easy let's call it 100 sheets which would cover scrap and damaged/unusable sheets. In my area used roofing polyiso that thick runs $20-25/sheet, so it's something like $2500 in foam (instead of $7500 or more, if virgin-stock). Add to that 100 sheets of OSB or plywood, for the nailer deck, and budget for about 1000 4.5-5" pancake head timber screws at about 50 cents each, something for facia boards & drip edge, perhaps some extensions & boots for plumbing stacks & flues, etc. At box store pricing R30 rock wool is going to run about $1.50 per square foot so for a 2500' attic it'll be about $4K. (You can probably find it cheaper through distributors.) Add it all up and you're probably looking at ~$10K in material cost, give or take.
A tight 2500' house 2x4 framed with an insulated basement would usually come in with a heat load of under 40,000 BTU/hr @ 0F. If your 99% outside design temp is within a few degrees of 0F that's going to take about 3-3.5 tons of ductless or ducted cold climate mini-split to cover the load. At about $3.5-4K/ton for ductless, and $5-6K/ton for mini-ducted it's probably going to come in slightly north of $10K for an all-ductless solution in competitive bidding, but probably less than $15K even with one of the mini-splits being a mini-ducted version. If contemplating that as a solution (definitely a good idea, if heating with propane or oil) the first and most important thing to do is to get a handle on both the whole-house and room-by-room heating & cooling loads.
If you have a heating history on the place you can put a firm stake in the ground on the whole-house load with a fuel-use based load calculation, which uses the existing heating system as the measuring instrument, as outlined here:
https://www.greenbuildingadvisor.com/blogs/dept/guest-blogs/out-old-new
[edited to add]
With 3.5-4" of foam above the roof deck, you can save some money by taking the R30s off the attic floor and putting them between the rafters. A fiberglass R30 compressed in to a 2x8 cavity would still perform at R25. If you held them in place with PERFORATED aluminized fabric radiant barrier stapled to the rafters they'd pillow out a bit, and probably run in R27-R28-ish range, which is fine.
The radiant barrier will keep the fiberglass from shedding airborne glass shards, and would add about R1 to the total performance of the roof, and is cheaper than using gypum board or OSB/plywood as the interior side air barrier. Perforated radiant barrier runs about 5 perms, a Class III vapor retarder- it's not going to create a moisture trap.