Cost effective exterior wall construction.

In exploring options for a cost effective R-40 exterior wall in a cold climate (Western Massachusetts), I am left scratching my head. As a residential designer, I have researched Building Science’s website and their High R wall systems, where multiple layers of rigid insulation and a thermal break is their obvious choice. However, when clients want shingled siding and decorative trim, I want the sheathing on the exterior face of the rigid for consistent nailing. In addition, my structural engineer wants the sheathing directly nailed to the studs for shear (100 mph wind speed).
That being said, I was planning a double 2 x 4 wall filled with dens-pack cellulose. However, I just witnessed a hybrid wall, framed with 2 x 6’s (or 2 x 8’s) at two feet centers and rigid insulation spacers on the inside face each stud with horizontal interior nailers. This provided a thermal break, increased the bay depth and was cost effective. Any ideas on the pro’s and con’s of each?
GBA Detail Library
A collection of one thousand construction details organized by climate and house part
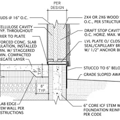
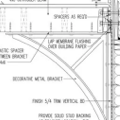
Replies
Jon,
I think the question you're asking is a great one, double wall with it's built in thermal break for the framing or standard stud construction coupled with a foam thermal break. I think the last option you describe is a strapped wall system, this has been around as long as the double wall. The problem I have with a strapped wall is the horizontal strapping can make for difficulties when hanging cabinets and the like. Tradespeople look for vertical connection surfaces most oftem at 16" oc and you may have a lot of holes where you do't want them.
Where are you thinking about placing the primary air barrier?, sounds like you are planning on OSB or plywood sheathing for a continuous nailing surface for the siding. I think the placement of the air barrier and the ramifications of it due to thermal bridging is the question of the day.
I am a warm sider when it comes to air barriers but I live and build in MN. My wall dries to the outside and this works well for me. There has been some concern here in MN about the use of a low perm (OSB) exterior sheathing which places the primary air barrier on the cold side allowing only for the drying to occur to the warm side, opposite the typical warm to cold heat flow. I use a fiberboard sheathing coupled with housewrap, but this would not provide the nailing surface you are after and may not be suitable for your climatic location.
The primary air barrier for both systems would be as housewrap under a layer of Homeslicker as a drainage plane. Building Science's double stud wall shows the vapor barrier on the outside face of the interior wall - something very difficult to construct, since the interior double wall (non-bearing) will go up after the shell is completed. As for the strapped wall, I would specify the airtight drywall approach.
In response to your horizontal strapping comment, I have seen installed 2 x 8 horizontal nailers with vertical blocking over the rigid all the way to the floor.
Jon,
My first double wall was built the same way you have described the BSC method, the vapor barrier was on the outward surface of the inner (warm side) wall. This is to provide a wiring chase I presume but is a pain to carry out and I have since gone to a warm side air barrier. The important thing is to follow through with all details and strive for maximum airtightness, encapsulate the insulation.
Jon,
I've built a number of double wall homes and a couple of Larsen Truss or modified Larsen Truss houses in Western Ma (Plainfield and Charlemont). I find the modified Larsen Truss superior to double wall in many ways, but your engineer might not be happy with the shear bracing.
I think you'll find that a double 2x4 stud wall is simpler than the stud-foam-strapping-blocking option. You still have to deal with thermal bridging at the floor and ceiling decks and the challenges of continuity of air barrier, as well as the ambiguity of load paths with an interior wall. But you will get a better thermal break with a wide space between inner and outer studs - you can also stagger the studs to keep them o.c. with both inside and outside corners for minimal waste of sheathing and drywall.
If you're interested, this is my modified Larsen Truss wall system with interior load-bearing wall, almost no thermal bridging, and R-45 whole wall value. http://www.builditsolar.com/Projects/SolarHomes/LarsenTruss/LarsenTruss.htm
Thanks for the responses. I am leaning toward the double wall with exterior wall sitting on the foundation and floor framing inset to deal with the thermal break problem. My cost comparisons show the double wall to be most cost effective and workable by builders.
Robert, in your Plainfield and Charlemont houses, did you locate a vapor barrier on the exterior face of the interior wall? Interesting - both towns are within 20 miles from me.
Jon,
For my first Larsen Truss house in Plainfield, I built a conventional 2x4 platform frame (but with rough-sawn), sheathed it with diagonal RS boards, installed 8 mil Tenoarm Swedish UV-stabilized virgin polyethylene vapor barrier (far better than conventional poly) on the outside like housewrap with one horizontal taped seam, and then added the 8" parallel-chord trusses on an extended grade beam. This put the vapor barrier at the 1/3 R-value point. But, because I used no secondary sheathing on the exoskeleton, I had to drill holes through the inner frame sheathing AND the VB in order to blow cellulose in the truss cavities. That required patching each VB hole before installing fiberglass batts in the interior frame cavities.
Because of the problems with a 2-cavity wall system, and because I moved away from using plastic vapor barriers in favor of the Air-Tight Drywall System, my Charlemont house was a modified Larsen Truss (Riversong Truss) system, also built entirely with rough-sawn lumber. This house also began with a conventional 2x4 platform frame to get it under roof quickly and easily, but it used the primary frame as the inner chord of the truss by adding a "half-truss" (pre-assembled RS 2x3 with 1x4 gussets 24" oc). I eliminated sheathing entirely, using Simpson TWB let-in metal bracing (code approved) in the structural frame. The exoskeleton was simply tipped up on the extended concrete grade beam and tied to the studs (aligned floor-to-floor) from the inside with no ladder work required (even the gables could be done from inside the attic).
This resulted in an incredibly simple and easy-to-build double wall with almost no thermal bridging and a "quilt" of dense-pack cellulose that wrapped the entire building uninterrupted. The thicker we make our walls, the more problematic a vapor barrier becomes. And, as we should all know by now, it's an air barrier that prevents inside moisture from entering the thermal envelope. Vapor retarder primer is all that code and building science requires.
Jon,
On another topic, I understand you've been talking to Dennis Purinton about the Thermomass foundation system (I just got off the phone with him). Do you have any experience with Thermomass and what is your take on it? Do you plan to use it and, if so, with what thickness of foam core?
Robert,
I have investigated the Thermomass system, and find it very interesting. Dennis has been very helpful.
The pro's have to do with a durable, insulated exterior and interior wall surface which will allow for a spray waterproofing system in a high water table condition. Also, you have a thermal break with rigid insulation centered in the wall. To achieve an R-20 wall, I would specify 4", resulting in a 12" thick pour.
The con's that I see have to do with cost and availability with contractors in my area. I have reviewed the system with two concrete contractors, been given estimates and am finding the cost to be similar to ICF's (for 2" rigid). Both require a concrete pump, but I like the Thermomass for waterproofing detailing. There is also added steel reinforcing in the Thermomass wall, compared to a standard 8" or 10" pour. I also like the Thermomass for the above grade exposed portion of the foundation.
As you have described above, the least expensive way is a standard foundation with exterior insulation, parged above grade. With 4" rigid on the exterior, the floor framing would have to cantilever over the face of the foundation with standard or double wall framing.
Jon,
One of the reasons I like the ThermoMass system is that, with 4" of foam, the foundation thickness will match my mofidied Larsen Truss wall thickness. But with a conventional 8" foundation and 4" exterior foam, the Larsen Truss with interior load-bearing wall doesn't require cantilevering the floor deck since only the non-bearing trusses are over the foam. I install a 3/4" CDX secondary sill (and metal insect flashing) to cover the exterior foam. The floor deck sits on the inboard part of the CDX and supports the cantilever for the outer truss chords, maintaining the thermal break at the floor framing. In fact, by running the exterior foam right up to the CDX 2nd sill, there is a thermal break outboard of the PT sill as well.