Cost effective efficiency improvements possible for investment properties?

I’m looking at purchasing some single or small multi-family rental properties and possible an occasional rehab. I would love to do my part in helping to reduce the energy consumption of buildings and hopefully provide a point of differentiation in my properties. Much of the properties I’m looking at, the owner pays for electric/gas. Unfortunately, I don’t think the market is willing to pay a whole lot more for energy efficiency as they don’t consider (IMO) the total cost of ownership or rent. Because of this, it’s hard to justify as an investor the considerable expense of a full deep retrofit on these properties. So how can I help to improve our existing, aging housing stock in a cost effective way?
The homes I’m looking at are in northern 4A (Cincinnati). A typical property will probably be built in the early 1950’s to early 1970’s. Construction is typically wood framed, often with a mix of brick veneer and vinyl/aluminum. Stucco can also be common. Insulation is not likely installed until some of the later homes. Ideally, we would rip off the exterior detailing or gut the interior and add foam, cellulose and air seal. However, this is obviously a costly solution unless the condition of the home warranted the demolition otherwise.
Is it worth just to dense pack the walls with cellulose along with blowing cellulose into the attic. Included could be some minor air sealing details in the ceiling and basement rim joists if accessible. Would this be a risky assembly without applying foam and leaving the exterior brick/stucco/vinyl intact? What would you do (besides tear the home down and start over)?
GBA Detail Library
A collection of one thousand construction details organized by climate and house part
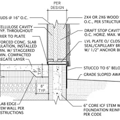
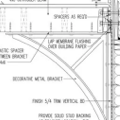
Replies
Brad,
Creating a list of cost-effective energy retrofit measures is a routine part of the job of any home energy rater. To determine the measures with the best payback, you should hire an energy rater certified by BPI or RESNET to perform an audit on the building. Your rater will present you with a list of measures that is specific to your building.
In most cases, the list will include air sealing measures and more attic insulation. In some cases, the list will include adding cellulose to the walls. In some cases, the list will include a new furnace or new storm windows.
You might want to talk to your local low-income weatherization agency. Here in Vermont, landlords can get free weatherization work on rental buildings if their tenants have low incomes. To be eligible for this program, the building has to be occupied so that the income levels of the tenants can be verified.
Retrofit insulating the stucco with cellulose can be risky or not depending on the stackup. Most of the time brick veneers will have a sufficient ventilation gap to limit the risk, but that too needs to be assessed on a case-by-case basis.
With vinyl or aluminum siding the risk is near-zero, since the siding itself won't hang onto moisture, and is inherently back-ventilated.
As a rule air sealing is beneficial and cost effective with or without insulating, and is an important first-step prior to insulating.
Thanks for the advice Martin. I'll check into local programs, but like you mentioned the eligibility will be dependent on my tent mix. I'll also consider utilizing raters in the rehab process.
Dana, thanks for the sound suggestions. It sounds like I should do some investigation of the wall construction if possible prior to purchase. If I understand you correctly:
- Aluminum/Vinyl - go ahead as there will be minimal risk of moisture problems.
- Brick or stucco- moderate-high risk depending on wall detail. Brick/stucco with airspace and a suitable barrier/sheathing shouldn't be a problem. Brick/Stucco without airspace could lead to problems.
So if the above has sheathing (with an air gap) is the sheathing at risk for moisture/mold problems with cellulose due to the dew point being focused there?
As long as there is a reasonably ventilated gap the sheathing is protected from moisture accumulation. If there isn't a sufficiently vented air gap, the fact that the masonry stores moisture (from both dew & rain) then releases it in both directions when it warms up is a problem.
It was pretty common in the 1950s to apply stucco to lath directly on the outside of studs, with zero insulation in the studs, with the empty stud bay serving as the ventilation space. Insulating one of those with cellulose would be a disaster, since the cellulose would continuously wick up the moisture from the stucco/lath until it saturates, putting the structural timbers at risk. Insulating those cavities with ANYTHING without creating a ventilation gap would put it at considerable risk. If the assembly has plywood sheathing, felt (1 or 2 layers) and at least 3/4" of air between the felt and lath, with vents at both the bottom and the top of the stucco stuffing the stud bays with cellulose is fine. If it's plank sheathing, ship-lap, or t & g there's some risk of cellulose getting into the vent bay in sufficient quantity to block convective drying, particularly when dense-packed.