Convert Florida Attic from vented to unvented

I have a house in Florida (ASHRAE 1/99 temp range, 46-92 F) that previously had a ventilated attic. I had plans to turn it into a sealed attic with spray foam and when replacing the roof and siding I choose to get rid of the soffit vents and ridge vents and the attic is now unvented but I am not sure I still want spray foam. I am leaning towards using rockwool or bibs against the roof deck but have concerns about air sealing the roof deck itself.
Reasons I wanted a sealed attic.
1. Better HVAC performance since ductwork is in the attic
2. Better hurricane performance from wind driven rain in the ridge vents and soffit collapse causing roof failure. Soffits are solid plywood with unvented vinyl over them.
Concerns I have with using spray foam
1. This is my main concern as it saves $1000$ a year on insurance. Hurricane clips and roof sheathing nailing schedule inspections that must be done each time insurance is renewed(roof deck and rafter ends access is required)
2. I’ve heard remodeling after spray foam is installed is a pain. Not sure it matters in an attic?
3. Cost of closed cell or open cell foam is expensive.
Concerns I have with air permeable insulation (rockwool, bibs, open cell spray foam)
1. I don’t have a vapor diffusion port and I’m not sure if it’s even needed in my climate as our 1% temperature is 46 degrees and code requires insulation or vapor diffusion barriers if the roof deck is below 45 degrees.
2. Air sealing of the attic. I have air sealing from the soffit to the roof deck with rigid insulation. I don’t know how to air seal the roof deck, is the synthetic underlayment (not peel and stick, not taped at seems) under asphalt shingles sufficient to air seal? Or do I need spray foam here?
3. I didn’t know about vapor diffusion ports and insulation installers and builders in the area didn’t mention it when I asked about ridge rot. They said they didn’t experience ridge rot. I do not currently have a vapor diffusion port.
This is a 4/12 roof made with trusses and dimension lumber sheathing. Walls are air sealed with zip and seams taped as well taped to the soffits. Bottom of zip is liquid flashed to the concrete block wall below. Ask windows and doors have been replaced and caulked.
TLDR; I’d like to air seal and insulate my attic to make it unventilated with my ductwork inside. I desire to leave the end of my rafters and rafters exposed for inspections and spray foam doesn’t allow for this. I’m ok with peeling back batt insulation for inspections.
GBA Detail Library
A collection of one thousand construction details organized by climate and house part
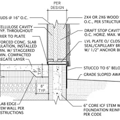
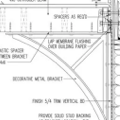
Replies
sdpo7d,
If you want to convert to an un-vented attic I would either use one of these assemblies
https://www.greenbuildingadvisor.com/article/five-cathedral-ceilings-that-work
Or for projects in climate zones 1,2 and 3, much easier would be to use a vapour-diffusion port. It may not be required, but using permeable insulation without a way to exhaust moisture is asking for trouble.
https://buildingscience.com/documents/guides-and-manuals/gm-2101-guide-building-conditioned-unvented-attics-and-unconditioned
I'm in zone 2. That second project is what I am thinking of doing to avoid spray foam. My concern with that method is, what do I need.to do to the roof deck to make it air tight? Do I just assume the synthetic underlayment is acceptable. I think I can have a roofer retrofit the vapor diffusion port.
sdpo7d,
This is a good opportunity to clarify how these attics should be built - something I don't know much about as I live too far north to use vapour-diffusion ports. Hopefully others will contribute to the discussion.
Unlike most vented and un-vented roof assemblies, the ones shown in Joe L's article don't appear to have an air-barrier under the insulation to stop moist attic air from reaching the sheathing. I'd be interested in an explanation as to why that isn't necessary, and how they are detailed.
Bump.
"2. Air sealing of the attic. I have air sealing from the soffit to the roof deck with rigid insulation."
Please explain this further - do you have exterior rigid insulation on the outside of the sheathing, underneath the underlayment and shingles?
Using permeable insulation, like Malcolm mentioned, will allow interior moisture to migrate through it and possibly condense on the underside of the roof decking. The fact that you have an impermeable underlayment on TOP of the roof decking does not prevent rot on the underside since the humidity is coming from the living areas of the house, not the outdoor air in this case.
Since it would be expensive to add a vapor diffusion port, you can do something really simple like install a plug-in dehumidifier and a floor drain somewhere in your attic space to keep RH down and prevent condensation. Maybe install a humidity sensor near the roofline and monitor it if you want to be extra safe. The one plus of having the permeable insulation is that you should be able to identify moisture problems more quickly than if you have something like open-cell spray foam.
matthew,
I'm not at all familiar with Florida codes. Is there a code compliant un-vented roof with interior permeable insulation? I thought you needed a vapour diffusion port?
That's why I asked if he has exterior insulation or not. 2023 Florida Building Code, Chapter 8 Section 806.5 (https://codes.iccsafe.org/content/FLRC2023P1/chapter-8-roof-ceiling-construction):
"In addition to the air-permeable insulation installed directly below the structural sheathing, rigid board or sheet insulation shall be installed directly above the structural roof sheathing in accordance with the R-values in Table R806.5 for condensation control."
but then it also gives an alternative:
"Alternatively, sufficient rigid board or sheet insulation shall be installed directly above the structural roof sheathing to maintain the monthly average temperature of the underside of the structural roof sheathing above 45°F (7°C). For calculation purposes, an interior air temperature of 68°F (20°C) is assumed and the exterior air temperature is assumed to be the monthly average outside air temperature of the three coldest months."
So given his 1% design temp is already above 45 degF I see no reason why he can't use air-permeable insulation according to the code.
Insulation
I do not have exterior insulation on the roof deck. I understand there is that exception in the building code which makes me feel ok about not having a vapor port but it also adds additional cost if I need one.
Air sealing
I have walls below my roof built with zip sheathing that's been air sealed and insulated with rockwool inside. At the transition from my zip sheathing to the plywood on the underside of my soffit, it is taped with zip tape to make that air barrier continuous. From inside the attic, there is rigid foam between the soffit (that's sealed to the walls) and roof deck. I plan to seal the edges of this rigid foam to make it air tight. My roof deck has no air sealing. Is that needed anywhere other than around penetrations? I have dimensional lumber sheathing there so, large gaps covered between boards covered with synthetic underlayment.
I think I have decided to go with open cell spray foam. I found an installer that has experience removing the spray foam for inspection of hurricane clips. Builders in the area don't use vapor diffusion ports it seems. I am leaning towards installing one, but I wasn't sure if I should install it before spray foam. Will the foam adhere and make it vapor impermeable? If installed after spray foam, I'll have to cut/ pull some decking off to create a vent which will damage the foam.
I am not an expert, but I don't see a way using section R806..5 that you can have an unvented roof with permeable open-cell insulation sprayed along the roof deck. If you had some exterior insulation then it would be fine. Maybe talk to your inspector before you do this.
Matthew,
I don't see anything in R806.5 that would preclude it in climate zones 1, 2 and 3. Where do you see the interdiction against it?
The section also specifically allows air-permeable insulation as the only insulation in an un-vented assembly as long as there is a vapor-diffusion port.
Again, not an expert, but I see this at the top:
5.Insulation shall comply with Item 5.3 and Item 5.1
Within 5.1 I don't see how the OP is satisfying this requirement in 5.1.2:
"In addition to the air-permeable insulation installed directly below the structural sheathing, rigid board or sheet insulation shall be installed directly above the structural roof sheathing in accordance with the R-values in Table R806.5 for condensation control."
5.2 doesn't really seem to apply since he is not installing it along the floor, but rather on the underside of the roof sheathing. And 5.3 doesn't apply since he is not using rigid foam boards. How is he able to get around 5.1.2?
Edit: perhaps we are disagreeing on if OC SPF counts as air-impermeable or not. I am saying it is air-permeable, hence 5.1.2 would apply. If you think is it impermeable then I think only 5.1.1 would apply and he would meet that criteria. How thick does the OP plan on installing the open cell foam?
Matthew,
Yes, I was assuming that if open cell foam was the only insulation used it would be applied thick enough to be air impermeable.
For permeable insulation I was going by this: https://buildingscience.com/documents/guides-and-manuals/gm-2101-guide-building-conditioned-unvented-attics-and-unconditioned which has 5.2.8, that doesn't seem to have made it into the Florida code you posted.
I see. I think the OP has some homework to do. Looking at the 2021 IRC (not Florida amended version), 5.2.10 is pretty clear that they need supply air in that conditioned attic space when using "air-permeable" insulation against the underside of the roof sheathing - it also seems like a vapor diffusion port might be required in this case. I think at a certain thickness of open-cell foam it becomes vapor-closed, so that needs to be investigated too.
Using exterior insulation would allow you to avoid section 5.2 altogether since you would be covered by 5.1.4.
Matthew,
I don't know why I stray down the path of trying to understand other building codes. Our own is challenging enough.
I made a mistake in my original post that may have misled you and others. I incorrectly called open cell spray foam air permeable. I believe it is moisture permeable (<15 perms) and I mixed that up with air. The foam will be installed at 5.5" for an r value is R20. It is considered as air impermeable at this thickness so I think I can skip over 5.2.1.
Link to foam: https://huntsmanbuildingsolutions.com/en-US/products/open-cell-insulation/foam-lok-500
But, if it was considered air permeable, I could get around that with the vapor diffusion port since I am in climate zone 2. Also, since my 99% temp is 46 degrees, I think I can use 5.1.4 to get around any exterior insulation above the roof sheathing.
I want to avoid the vapor diffusion port since vapor drive here is to the inside of the building some humidity outside is at 80% much of the year.
sdpo7d,
Your post didn't mislead me, I just don't have a good enough understanding of either building in a warm, humid climate, or your code to comment usefully. I probably shouldn't have weighed in.
In California climate zone 3, some jurisdictions allow tile roof with air permeable insulation. Presumably having a vapor permeable underlayment and venting through the tiles allows enough drying to the outside. Assuming you don’t have a vapor permeable underlayment and a tile roof, your next best option is a vapor diffusion port.
Why not just have a roofer peel back some roofing at the ridge, drill some holes or cut a strip equal to 1/150 of the roof area, cover it with a vapor permeable underlayment and install a vented roof cap?
To Malcom’s point however, it’s a little gray regarding air barrier location but one would assume it’s importance either at the attic floor or the underside of the trusses.
Or if you’re really feeling adventurous and you don’t have a north facing roof you could just install the insulation and monitor the roof deck, primarily near the ridge for moisture accumulation. This is obviously not to code but you’d be surprised how many people get away with it with no damage…until they don’t.