Conversion of crawl space into conditioned space.

I am involved in an Energy Performance Contract with a Housing Authority. In a 1960’s development of 20 town house type apartment buildings (4-6, 1 and 2 story units in each each building) we have up-graded to high efficiency natural gas boilers using the existing hydronic baseboard system, added insulation to the attic, replaced doors and windows and now are facing the problem of what to do in the vented crawl spaces which contain the heat and hot water distribution systems.
The building inspector is looking at the development as one entity of over 35,000 cu ft and wants the permit application signed off on by an architect or engineer. My company had an architect with no particular experience with this issue come up with a set of recommendations. Her focus was code compliance and has called for a high performance vapor barrier (Tu-Tif membrane) taped and mastic sealed on the floors (rat slabs w/ 2″ concrete), R-13 foil faced polyiso on the interior walls, air sealing the floor above and sealing off the 500+ vents and insulating the box sills in which the the vents are located.
The problem is that that this has become too expensive. The quote is 5X the gas company’s incentive and 2.5X the total available funds.
If the vapor barrier component could be demonstrated to be unnecessary the project could become possible. The buildings are located on a well drained gravelly soil and the slabs are observed to be dusty dry indicating that we are dealing with a limited amount of diffuse vapor entering the spaces from the ground. Can anyone help with a method of analysis to determine the safety of sealing up this space without providing the class 1 vapor barrier on the slab?
GBA Detail Library
A collection of one thousand construction details organized by climate and house part
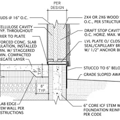
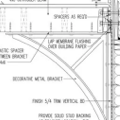
Replies
Jonathan,
My first reaction is: that's false economy. You can't afford to install a vapor retarder on the crawl space floor?
You could always save a few bucks by switching from Tu-Tuff to 6-mil poly.
Switching to 6 mill poly does make it a lot less expensive but not enough to allow us to do the project. Bottom line is that if there is a moisture problem there to deal with we will have to forgo the Gas Co's incentive walk away from addressing this measure and invest in another ECM in at this or another of the Housing Authorities Properties. If a vapor barrier is needed the measure is not cost effective.