Construction sequence for mineral wool insulated double walls?

This concept is base on the assumption of a PWF with it’s top flush with the bottom of the sub-floor but may be adapted to other situations. My current plan is 2 ea 2×4 walls, both sheathed on their outer faces. Fiberboard on the outer and OSB on the inner. I I hope to use 3 layers of 3 1/2″ mineral wool bats. I’m thinking that it may be possible to build all 3 layers on the sub floor then erect all at once as an assembly. Here’s how: Key to the process is that the sub-floor has a joint under the inner face of the inner wall and is trimmed to that location before wall construction commences. The inner wall is framed first, then sheathed, taped (the OSB is my primary air barrier) then a strip of sub-floor material the width of the complete assembly before outer wall sheathing is nailed to the bottom plate of the inner wall, the sub-flolor material is taped to the OSB, this strip of sub-floor is the length of the outer wall minus outer sheathing, corner segments, without sheathing, of outer wall are built on the ends of the sub floor if needed. The inter wall insulation is placed then the bottom plate of the outer wall is nailed to the strip of sub-floor, temporary blocks connect the top of the inner wall to the outer wall studs and the outer wall is framed above the inter-wall insulation. the outer wall insulation is placed, last the outer wall is sheathed missing some corner bracing segments which are installed after all the exterior walls have been erected. For a little less thermal bridging and more cost the strip of sub-floor might be replaced by a 10 15/16: wide piece of 1/4″ plywood for the full width and an added strip 4 15/6″ wide layer just under the inner wall plate. The downside is added “joints” in the outer wall probably requiring more studs. FWIW I’m planning on the outer wall being 16″ OC as required for structural fiberboard with the inner wall @ 24″OC with every other inner wall stud aligning with an outer wall stud. Also the outer wall’s top will be higher to make a floored “attic” filled with cellulose under flat bottomed roof trusses.
Does it sound workable? Has anyone tried something similar?
GBA Detail Library
A collection of one thousand construction details organized by climate and house part
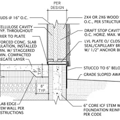
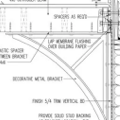
Replies
Jerry,
If I followed your description correctly, it might work, but it's complicated -- and that wouldn't be an easy wall to raise.
Your basic challenge is finding a way to insulate between the two 2x4 walls with mineral wool batts when you also have OSB sheathing on the exterior side of the inner wall. I think that the easiest solution is to install cellulose instead of mineral wool between the two 2x4 walls. It makes the assembly sequence a lot easier (although this approach has its own challenges, because it means that you will be installing the cellulose blind, with no ability to touch the InsulWeb membrane to verify insulation density).
I look forward to comments from other GBA readers.
Martin, THANK YOU! for the encouragement. I do understand and appreciate the difficulty of raising a heavy & big wall. Roughly 40 years ago (we moved in on DEC. 1 1976) I built, almost single-handedly, while employed full time,working 40 hour weeks at my "day job', with occasional volunteer help, a French colonial style house. The second story walls featured a steeply sloped roof and curved to a much wider less steep roof that "overhung" the floor framing. These walls were made of site built plywood gusseted trusses 16"OC. The inner wall was 8' tall & vertical the two top plates were touching at the top while the bottom plates were 2 feet apart the slope at the bottom was 12-12 and the overhang added another 2' of width at the bottom the first,and biggest wall, was 40 feet long and included three dormers (outer wall vertical) with curved tops that accommodated 48" wide windows the headers were doubled 2x12s , in both walls. The wall was fully sheathed with 1/2" plywood that was back scarfed and curved between the slopes, tar papered, AND shingled with 3 tab asphalt shingles while "on the deck". I and a crew of 5 voulenteers raised that puppy by hand and I ended up with a very painfull back injury that really slowed me down. After that I rented a pair of wall jacks and the rest were a "cakewalk" with one helper.