Confusion about exterior vapor impermeable foam

I know this has been discussed and written about many, many times. I have read and re-read the articles and talked to builders in my area. I think I know the answer but I have heard enough dissention that I want to ask this again here:
What is the risk of vapor impermeable foam on the exterior of a home?
I live in zone 6. All of the readily available foam, except for XPS is faced (even the one place that carries EPS only carries faced EPS. The general consensus seems to be “Stick a thick layer of foam on the outside, vapor retarder on the inside and it’s fine. The assembly dries to the inside and the sheathing stays above dew point.
A builder in my area keeps insisting this is a bad idea and that the only way to go is to be able to dry to both the inside and the outside.
Is this guy just being overly cautious or stuck in his perspective? I know that no matter what all of this comes down to having really good air sealing.
Thanks.
GBA Detail Library
A collection of one thousand construction details organized by climate and house part
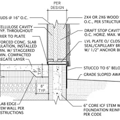
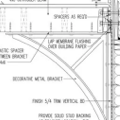
Replies
It doesn't hurt to be able to dry in both ways, and assemblies that can are more robust. It is NOT necassary to be able to dry to both sides though -- as long as you can dry to ONE side, you should be fine. It IS important to use AT LEAST the minimum thickness rigid foam for your climate zone though, which will ensure that you don't get too much moisture into the assembly during the colder months. An interior side smart vapor retarder then buys you some extra insurance by helping to keep moisture from getting in, while allowing for any moisture that does find a way to get in to dry out (polyethylene vapor retarders don't allow for any drying, which is why smart vapor retarders are better in most cases).
Your builder is probably one of the "houses need to breath" people, and that's old school thinking and not entirely correct. As long as you build one of the recommended assemblies as described on GBA, you'll be fine. If you want an extra margin of safety, do either or both of the following:
1- Use thicker exterior rigid foam (more R value) than the tables show. This will keep the interior of the wall warmer, which means less moisture will get in.
2- Use a smart vapor retarder on the interior, which will help to keep moisture from getting into the wall, while still letting any that does get in get back out.
Bill
Thanks Bill. Your advice makes sense. I just finished reading the "Foam Board on Double Stud Walls Is A No-No" article which has a handy chart for ratio of foam on the outside and the amount of foam I would need to add is not unreasonable. Being able to breathe in both directions does have an intuitive appeal but from everything I am reading and hearing, foam on the outside is becoming/is a common practice. Plus the idea of moving the frost line out the foam as a lot of appeal. Part of my wall stack up needs to use fiberglass because of some odd voids I need to fill and wet fiberglass is terrible.
The wildcard in this design is an approximately 1" wide lattice that runs around the perimeter of my home (I live in a yurt - I think you saw pictures of this in another post). I've been concerned about the gap the lattice makes - it's a 2-D structure with voids that are not easily filled. My current plan is to compress fiberglass on either side so it will "smoosh" into the voids of the lattice and reduce any air gaps. However, if I have a couple of inches of foam on the outside, could I safely ignore having to fill this void space? I would still fill the wall cavity between the studs with 3.5" of rockwool so that there is insulation all the way from my drywall to the innermost face of the lattice.