Confused about new roof / decking / insulation job

Hi, my name is Todd and I’m very confused about what to do. My insurance company has agreed to replace the roof, including the decking (sheathing), and ventilation, in my cape cod home in Dayton, Ohio. I have a refinished, vaulted second floor, with a small attic peak. All of this was there when I bought the home 3 years ago (I think it was done in 1998). Thinking this would be a chance to improve the insulation I began to investigate what to do. Now I am completely baffled, both online sources and contractors have given me such divergent advise.
This is what I know of my houses structure.
I have asphalt shingles
I have no soffit vents.
I have turtle vents and gable vents.
Rafters are 2 by 6.
I have R-19 batts crammed in the rafter along with styrofoam baffles (approximately 2 inches in depth). Thus the batts are compressed to roughly 3.5 in. This material runs from the knee wall top to the small attic floor and peak area (3 ft or so triangle).
I appear to have more substantial loose insulation on the floor rafters below the kneewall and assume I do in the small attic (I have no access to it).
I have no idea what to do. Thanks for any advice.
Thanks,
Todd
GBA Detail Library
A collection of one thousand construction details organized by climate and house part
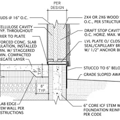
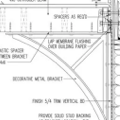
Replies
R19 is pretty crummy-R and sub-code R for OH.
The "right" thing to do would be to close up the venting, blow cellulose into the vent channels from the exterior when the new roof deck goes down filling the (2x6?) rafter bays completely, which would bring the center-bay R up to about R20. Then above the roof deck apply the appropriate slip-surface material on the new roof deck for 3.25" (R20) fiber-faced roofing polyiso, held in place with an exterior OSB nailer deck through-screwed to the rafters with pancake-head timber screws 24" o.c., with #30 felt and shingles or whatever applied to the nailer deck.
Alternatively (but more expensive), the foam could be held in place with 2x furring through-screwed to the rafters 24" o.c. with timber screws, with the nailer deck screwed or nailed to the furring, using a soffit-to-ridge venting system on the nailer deck. If there are many hips/valleys it's worth segmenting the furring to allow full cross ventilation too. This has the advantage of lowering the nailer deck temp in winter cutting down on ice-dam potential, as well as a drying path for any future leaks that develop in the finish roofing. Without the vented nailer deck any undetected leaks would likely ruin the nailer panel, maybe even saturate a foam panel. But it's done both ways.
The material cost adder for R20 iso is about $2 per square foot, but you'd then have a center-cavity R of about R40, but since the rafters are thermally broken by the exterior foam, the performance would be equivalent to something like R45-R50 applied between floor joists, which is more like code. With R20 above the roof deck you don't need interior vapor barriers to protect the deck from interior moisture drives, and it's fully IRC 2012 compliant for US climate zone 5 (Dayton is in zone 5):
http://publicecodes.cyberregs.com/icod/irc/2012/icod_irc_2012_8_sec006.htm
The air leakage behind & through kneewall attics is usually atrocious, and by making the roof deck the primary air barrier and blocking the vents, it brings those mini-attics fully within conditioned space, and your whole-house air tightness numbers will be much improved, and with the roof deck now partially inside the insulation layer, it runs much warmer, and minor air leaks from the interior into the attic space through those kneewalls don't turn into a moisture & mold problem.
In some locations (like mine) there are companies that reclaim roofing foam from commercial building demolition, which cuts 2/3-3/4 off the material price. If you need a truckload, insulationdepot.com delivers, for a price. They have a facility in WV, not sure about OH. In my neighborhood I have multiple vendors pf reclaimed foam, some of whom advertise on craigslist. YMMV
Unless it's marked otherwise, assume reclaimed fiber faced roofing iso to be ~R5.5/inch of thickness, so 3.5" would be the minimum thickness, even if most virgin stock goods are R20 @ 3.25". (R6/inch). It never hurts to put more, but at 6" or more the screw lengths get a bit unwieldy, especially if you go with the vented nailer deck approach.
Hi Dana, thanks for the detailed response, this is very, very helpful. I'm looking into details to get this done. Very much appreciated.
best Todd
James,
You have two choices: you can build an unvented roof assembly or a vented roof assembly. Either approach can work, as long as you get the details right.
At a minimum, you have to make sure that your insulation is thick enough to meet code requirements. You can't do that with 2x6 rafters, so you will have to make your roof thicker -- either by adding insulation on top of your roof sheathing, or by building down your ceiling to provide more room for insulation.
All of the options are clearly explained in this article: How to Build an Insulated Cathedral Ceiling.