Conditioned attic issues: Closed-cell spray foam in humid North Carolina
I recently bought an oceanfront house in North Carolina that was retrofitted from a unconditioned attic to a conditioned attic by the previous owner. (We get lots of humidity, wind and moisture being on the water). They used closed cell spray foam under the roof deck and nothing else. I’m having issues with humidity and some mildew. The ‘conditioned’ space is very hot in the summertime and cold in the winter time. (My top floor smells like an attic when it’s hot outside) My HVAC equipment is located in the space as well. The attic has three separate areas that each have thier own access with living space in between. The rest of the house is insulated with cotton insulation. The roof line is a bit complicated and the house was built to be vented. It has a finished living space between attics with tongue and groove ceiling. I’m not sure if that’s sealed from the soffits or not. I do know it’s sprayed foamed.
Here is what I found: The spray foam installers did not properly seal off the eaves. They shoved batt insulation in the eaves and sprayed around it to try and seal it. It looks sealed, but is it? I was able to pull out the insulation/foam at the eaves and see daylight and soffit vents. (picture attached) They also left the old fiberglass batt insulation on the attic floor.
I had SPF insulation company come out and they recommended pulling out the batt insulation, sealing it with rigid foam board then spray foaming the entire attic again with open cell on top of the closed cell to seal it properly.
Here are my concerns/questions:
Access to fix the eaves is difficult with all of the HVAC equipment and ducts in the way. I’m afraid they won’t be able to get a good seal. See pics.
Can you spray open cell on top of closed cell?
I don’t love the idea of SPF and more chemicals in my house and the off chance it doesn’t cure correctly. Can I fix this without using spray foam?
How do I get fresh air in my attic?
Can I leave the closed cell foam under the roof deck and go back to a vented roof? Open back up the eaves and install vents. This seems like the easiest option at this point, but not sure if that’s possible. I’d be willing to sacrifice HVAC efficiency for clean air in my living space.
What do you recommend I do?
Thanks!
MG
GBA Detail Library
A collection of one thousand construction details organized by climate and house part
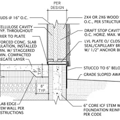
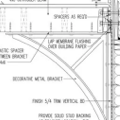
Replies
MG,
I am confident some of GBA's more knowledgeable members will advise you on what might be going on with your attic. In the meantime, you can learn more about this issue by reading this article: https://www.greenbuildingadvisor.com/article/high-humidity-in-unvented-conditioned-attics
Sounds like the primary issue is air sealing. That is best fixed and verified with the help of a blower door.
A remote humidity meter/hygrometer would be useful.
Open cell foam sticks to closed cell just fine, if that's the way you choose to go about it.
It's probably possible to air seal the soffit vent openings from the exterior- shoot us a picture from the exterior.
In less accessible areas you might be able to tighten it up a lot (though not fully air seal) by dense packing some cellulose in from the exterior.
It doesn't look like a whole lot of closed cell foam, and quite a lot of empty rafter bay. Filling those bays with well fitted rock wool batts would improve thermal performance by quite a bit while protecting the foam from igniting in the event of an attic fire. Roughly how much rafter depth is exposed?
Keeping the batts in place with perforated fabric type radiant barrier stapled to the rafter edges would pretty much eliminate stray fiber from getting into the attic space air (not that it's a big issue with rock wool, unlike fiberglass) without creating a moisture trap, as long as it's the perforated type. (The perforations increase it from being a true vapor barrier to roughly the same vapor permeance of standard latex paint on wallboard.) While not a true air barrier, perforated RB taped & stapled to framing on all seams & edges is VERY air retardent.
Dana- I'm going with your approach. Can fiberglass batts be used in stead of the rock wool batts? My contractor wants to use fiberglass.
If you can see daylight at the eaves, it seems like your humidity problems are the result of outdoor air infiltrating your "conditioned attic." I don't think that reverting to a vented attic is your best option. Though it is possible, it seems likely to be as much work as it will be to finish the job of bringing the attic into the conditioned space, which will yield a much more efficient home, considering the location of your HVAC equipment. Are you hoping to do this work yourself? Otherwise, this is something pretty straightforward that a good contractor should be able to help you with.
MG,
Although you wrote, "How do I get fresh air in my attic?", I think you're on the wrong track. What you want is less fresh air in your attic. The outdoor air is bringing in the humidity and causing the problem.
What you need is careful air sealing work to exclude the entry of outdoor air. The only way to make sure that this work is effective is to verify the work with a blower door test after the work is completed. For more information, see "Blower-Door-Directed Air Sealing."
Thank you for the replies.
Questions: If I keep it conditioned and fix and leaks form the outside:
1.) Should I have the attic floor insulation removed? It seems the attic would need to breath if it's completely sealed, correct? Remember, I have living space between my attics, I don't want stale air leaking into my master bedroom from the attic access doors.
2.) The closed cell foam is about 2 inches thick. My SPF contractor suggested blowing open cell on top to achieve a higher R value. Is this necessary and if so do I need to cover it with drywall for fire code? The attic will only be used to repair and service HVAC equipment. OR should I try getting a better seal at the eaves and remove the attic fllor insulation first to see if that solves my humidity and heat problems?
Thanks in advance. Iv'e learned a ton from this website. The only problem now is I know too much! Ignorance is bliss :)
All the best and thanks in advance for the help.
MG
1> It's fine to leave the floor insulation in place- just pull it back away from eaves or wherever you need to air seal. The floor insulation's R value no longer counts toward code insulation requirements, but that's not to say it'd not doing at least some good. In most cases it's fine to let the attic air stagnate, but a tiny amount of exhaust-only ventilation depressurizing it relative to the fully build out rooms would prevent potentially contaminated air from getting into the living space.
Removing the floor insulation will not change the humidity conditions in the attic, but air sealing it well from the exterior will, and is critical to getting the full benefit out of your roof insulation.
2> At 2" you don't have sufficient R value at the roof deck to meet code requirements, but it's plenty of R for dew point control on air-permeable insulation below it. Open cell foam is useful for air sealing, but 2" of closed cell foam has already sealed most of it. Filling the space with rock wool would be both higher-R and cheaper than doing it with open cell foam, and reduces the fire risk. Local codes may or may not require covering exposed foam with a timed thermal barrier or ignition barrier, but as little as 3.5" of rock wool is a HUGE improvement, and doesn't have the outgassing risk that mis-installed open cell foam can have. It takes a lot less foam to just fix the air leaks than it takes to fully insulate the roof to code.
IRC's code minimum for climate zone 3 (all of coastal NC) is R38. The 2" of closed cell is good for R12-R14. Installing 5.5" rock wool batts would add another R23, bringing pretty close to code-min at R36-R37 total. If the batts are held in place with perforated aluminized fabric radiant barrier stapled to the underside of the rafters it adds another R1, so it's really pretty much "there".
In my area 5.5" of half pound open cell foam costs about $1.75 per square foot, and is only R20. R23 rock wool costs about a buck a square foot for the material even at box store pricing (in case you're considering a DIY), and usually no more than $1.25 per square foot installed. (YMMV- if it's in a cramped difficult area to work it could be more.) Perforated radiant barrier runs about $0.15 per square foot for the material, not sure what the installed cost might be in cramped kneewall attic spaces. It should pretty cheap in open attics, but I've never had it quoted- it's not commonly used in my area.
I think you need to decide if you want a conditioning attic or not. Currently you seem to be stuck in the middle.
I think you should fully condition the attic by fully sealing the attic to outdoors and opening the attic to the indoors, then tested the house with a blower door pressurizing the house using a fog machine in the attic and look for smoke exiting the attic outdoors. Fix the leaks and retest. After you have a sealed attic only then insulate the roof to R38 inside or out whatever makes more since. If the roof is old outside is not a bad idea. Then add supply or return ducts so the attic air is not stagnant and is almost the same temperature as rest of the house. You can abandon the insulation on the attic floor as long as its R value is less than half of what you now have on the roof.
Or you could go the other way, remove enough foam to vent the roof then air seal the attic from the house tested with a blower door finally insulate the attic floor to twice the R value if the abandoned insulation on the roof.
Walta