Condensation under WRB during construction

Built a 2 story, 1300 SF addition on a house in Portland OR which got dried in in early December. The addition has no insulation yet and heat is inadequate and inconsistent via wood stove and the central natural gas furnace that serves only the first floor. The stairwell to the second floor is centrally located and the wood stove is on the first floor adjacent to the stairwell opening. Second floor heating will be a yet to be installed mini split system. A portion of the addition is an unheated garage. Currently running multiple fans and 2 dehumidifiers day and night. Interior surfaces are by and large very dry though there is consistently high humidity throughout.
Question: Installed Fortifiber commercial WRB over CDX sheathing with furring for the rain screen. I have noticed a substantial amount of condensation collecting under the WRB that has saturated the exterior surface of the sheathing. I’m looking for guidance on whether this is typical during rainy winter new construction and is only temporary until insulation, all permanent heat sources and interior finishes are installed?
Second question is how to go about properly drying out the moisture that is between the sheathing and the WRB?
Thank you for your collective wise advice!
GBA Detail Library
A collection of one thousand construction details organized by climate and house part
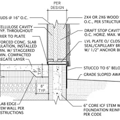
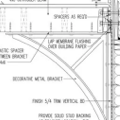
Replies
Robert,
Fortifiber WeatherSmart Commercial WRB has a vapor permeance of 14 perms, so it should allow outward drying. I'm rather surprised at the phenomenon you are describing.
The WRB is now cold -- a little colder than the plywood, which (since there is no insulation yet) is being warmed by the interior air. The vapor drive is clearly outward -- from the warm, moist interior toward the cold, dry exterior. The WRB is cold enough to provide a condensing surface, evidently, and isn't quite permeable enough for the drying rate to keep up with the rate of moisture accumulation.
My guess is that this problem will solve itself when the sun hits the WRB -- or when the sun hits the (not yet installed) siding. Still, it's odd.
We had a similar problem. I would suggest keeping the addition closed off from the existing structure, assuming that section is fully heated. E.g., with sealed plastic over doorways, to prevent moisture from the conditioned space getting in the addition. And pick a warm day to make a big fire in the stove to bake it out.
Thank you Martin. The record level rain fall over the past couple of months in these parts does make for the potential of overloading of the permeance performance of the Fortifiber. I've attached a couple of pictures to show you all what I'm seeing from the outside. The visible condensation on the surface of the WRB appears to be primarily at the thermal bridging wall structure.
Thank you Charlie. Got a fire going in there most everyday but we sized the stove on future needs and this little Morso 7110 isn't denting the chill in this big plywood box! The addition is completely separated from the main house with an insulated temp wall.
Glad to hear I'm not alone! The place looks like its bleeding water out there so from what Martin says the Fortifiber is doing its job but it's likely beyond its capacity through sheer volume. Need some sun for helping it along but that could be another month or two.
Sorry about the second picture being turned 90 degrees. The sharp break below the visible water is at the 2nd floor floor level. Below the water line is the rim joist space above the garage door opening.
.
Did the plywood get rained on before or after installation? If so, that's probably the moisture you're seeing. I wouldn't be concerned. At this point, moisture is leaving and not accumulating. The rainscreen gap is a big plus if you're installing the siding anytime soon.
Plywood was kept under wraps until installed but we finished framing in late November. early December when the rain switch was turned on. House has 3' eaves which helped keep things drier till the WRB went on. I would say the potential is there that the plywood went on at least damp in areas.
Good to confirm again that the WRB is working to remove the accumulated moisture.
Any other drying out tips out there? Looking at managing this condensation for another two months of lovely NW rain before the DIY roof, insulation and drywall install begins.
The roof system currently is 4x beams on 5' centers; 1-1/2" 2x6 decking; 3/8 plywood diaphragm (seams taped with 3M 3015 and 2 layers of Tribuilt HP also taped for air barrier). Final roof will be unvented. Adding 5-1/2" Raycore panels; 1/2" CDX and top it with another layer of Tribuilt HP and then metal roof.
Even though the 3/8" roof diaphragm, tape and Tribuilt HP went down dry I'm suspecting that I should pull the Tribuilt when the sun returns to ensure that this sub-assembly is 100% dry to build on. From what I'm seeing with the walls I imagine the same condensing issue is going on on top of the diaphragm. Thoughts on that? Thanks!