Condensation on windows with steel SIP home

We built a steel SIP house this summer near Hannibal, MO. We’ve been very happy with the results with one exception. The builders used steel L-angle to wrap the windows on the outside in order to better square the openings before installing the windows. They also installed the windows. This steel angle is not thermally broken at all. One part of the angle lays against the steel panel skin on the outside, and the other angle extends past the window into the living area about 2″.
We do not have siding on the home. We have left the exterior steel exposed.
So we have major condensation when the temp of the steel drops (see attached pic). Water pools on the metal. We are unable to trim out our windows until this is solved. Since the builders traveled in from 1500 miles away, they have had me attempt to fix it.
We’ve attempted wrapping the steel in fan-fold, with sill sealer foam, with Norton CST tape (and silicone sealing all the edges – see attached), even with 1/2″ rigid foam. None worked. The Norton CST tape was the best seal, but water still condensed on top of the tape because cold still transferred through. Their latest solution is to go ahead and trim out the window with PVC moulding, siliconing all edges to attempt to seal it from the air completely.
Unfortunately, to confirm it’s working, I’ll have to remove the moulding to see if water is underneath. I’ll also need to wait until temperatures reach near zero to know if this would work in our climate. Meanwhile the remainder of my windows have towels at the bottom, and on cold days we’re wiping down the metal every few hours.
Our interior humidity is between 45-52 percent. Our interior temperature is 67 degrees.
So I have two questions:
1) Would anyone have a suggestion that wouldn’t involve taking out all the windows?
1) Are all these attempts, other than removing the metal, misguided? From what I’ve read about dew point and condensation, especially in our climate zone, I have serious doubts.
Thanks for any advice. We have a wonderful home if we can just fix this issue.
GBA Detail Library
A collection of one thousand construction details organized by climate and house part
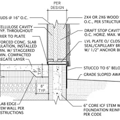
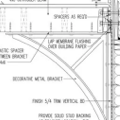
Replies
How did your builder trim out the windows in the other dozens of homes he built?
In the same manner, but they build in the southeast where this is not an issue.
Seems like you're going to need to place a fairly large piece of rigid foam over the steel, encapsulating it. I can't tell how much room you have to work with, but what about a piece of 1-1/2" thick x 3" wide XPS with a "rabbet" in one of the 3" faces to accommodate the steel? Attach that over the steel and seal it to the frame, then install trim over that. Tape/foam/sealant etc. to air-seal it.
Either that or pull the windows, cut back the steel angle, and re-install the windows.
It would help to see a section drawing showing the framing/SIPS, the angle, the window, etc., so we know what you have to work with.
Jeff,
David is certainly correct about the two ways you might fix this. The odd thing is, how can the builders have been so negligent? And are they willing to take responsibility for the cost to fix their error?
Jeff,
I'm afraid I don't have any helpful suggestions on your problem, but i'm intrigued by your description of the SIPs with integral siding. Could you maybe post a picture?
David, Martin,
Thank you. That's what I considered, also, but I am glad to hear it seconded. Unfortunately, I don't have that much room .We have a number of casement windows, and the handles sit only 1" inside the window frame, so, including trim, I only have 1" of space for a solution. I tried 0.5" rigid foam, but that wasn't enough R-value. And we have only been just below freezing this year. We'll go below zero later in the winter.
So far the builders are claiming that this is how they have handled refrigeration/cooling rooms in the past, and they have not had condensation issues. It's challenging to argue against that. They are builders, talking with a home-owner, so they are arguing their experience against what I have read. Having the opinions of others like yourselves is helpful.
They haven't completely refused to fix it, but they also haven't offered to come back to the home to repair it. They've given me suggestions over the phone of things to try. So we've spent 2 months now with towels at the bottom of our windows. Patience is waning.
Malcom,
Here's some pics of our home. Those are the metal SIPs, each 46" wide with a primer paint on them. Since metal SIPs are structural, they run the full height of the house, forming the outside of the shell. Interior floors are then balloon-framed inside. No rim joists--just continuous insulation from top to bottom. We planned to paint the outside, but once we saw the color we decided to leave it for a while. When it fades, we'll paint.
Picture 1 is of the house right after construction. The roof panels are still the bare SIPs.
Picture 2 is of the house with metal roofing.
Picture 3 is of the inside walls of the home. You can see some of the windows, and how they are trimmed.
It's a saltbox style, with a cathedral ceiling in the front living room, and open spaces throughout. The knowledge from GBA helped considerably during our design process. We're thankful.
David,
I don't have any section drawings, but these are pictures of a window. The metal angle protrudes in 1.25", the exposed foam after that is 3", for a total of 4.25" between the window edge and interior wall edge. Total wall thickness is 6". Casement handles are 1" above the frame.
Thanks Jeff, that's pretty neat. Good luck with the window problem.
Very cool, Jeff. What company made the SIPs, if you don't mind my asking? PermaTherm?
As for the windows, I imagine this problem will solve itself once you trim them and cover up the exposed metal. This condensation is caused by humid interior air touching the cold metal; once air can't touch it, water con't condense there anymore. Just take care with your air sealing while you're installing the trim, whatever you choose for it.
Nate, you're right that the condensation at this point is caused by humid interior air touching the metal, but if he doesn't put enough R value over the metal, or remove it entirely, the material that he puts over it could easily condense too. He has said that 1/2" foam is not enough. With a max of 1" where the latches are, his options to get more R are limited.
I would be concerned that even cutting back the metal to the face of the window unit might not work. What if the remaining metal condenses even though it's covered by the window unit and whatever trim he installs? Will that drain to the exterior? It's tempting to say that you could cut the metal back, apply sealant to completely encapsulate the exposed edge of it, and then trim it out... but would you sign a guarantee that it will work?
I'm not sure what effort would be involved in pulling the windows and removing the angle, but that's the direction I'm leaning. Hard to tell from the pic, but is there any exterior trim on the units yet? Unless there's something making this horrifically difficult, it's what I would do. It appears to be a one-story house with no difficulty getting to the exteriors. It might allow him to add sill pans at the same time.
As a stopgap measure, you might consider plastic window film over the interior of the whole opening, to stop moist air from getting to the metal. You could consider interior storms as part of a long-term solution.
The refrigeration units they make might have that metal completely bridging inside skin to outside skin, which would make the heat loss through the thermal bridge worse, but the condensation better. I don't recommend that, but it could help to explain the different experiences.
There's a super high density polystyrene foam available from 475. You can think of it as halfway between the strength of wood and XPS. It's similar or a little worse than EPS on R value. But it might help you fit more insulation below the handle, if you can then use a thinner finish over it. Wood veneer? Maybe just paint? I have not yet seen the stuff in person, so I am not sure it would work as a finished surface with just paint.
OK, one more idea, which might be the best. If you put in 0.5” XPS, the full depth of the opening, not just over the metal, and then put a layer of metal over that, ideally aluminum, the new metal might spread out the heat flow over a wider area so that none of the surface was as cold. That would work even better with the existing metal trimmed closer to the window.
I'm with David. For just a few easy-to-access windows, pull them and re-install them properly. Shouldn't be more than a day's work, maybe two.
Charlie, Nate, thanks again.
I am concerned about just cutting the metal back, too. There is window tape on the outside stopping the water from drying/draining to the outside. Combined with the seal on the inside, any condensation would remain in the space and encourage mold. If my seal is not perfect (and what ones are?), air gets in and problems start, but are hidden.
I haven't trimmed the outside of the windows yet, just in case they need to be pulled.
Interesting idea about the high density XPS. I hope to avoid a complex solution if a simple one is what is needed, but if I must fix it instead of pulling it out, that's something to try. There is thin PVC that I could place over it. We've kept our house industrial looking, so that type of trim would not be out of place.
I've spoken to the builders about dew point, and that a material that sits on the metal and becomes just as cold will also have condensation, so it's not just air transfer, but I'm not sure that they agree with me. I'm new to this, so I'm not sure that I'm right either. We'll see how the PVC performs. It's a relatively poor insulator.
Nate, it's not Permatherm, though I did speak with them, and the panels that we've used are near-identical to their panels. I hesitate to name the builder. I hope you understand. It would seem too much like calling them out for the issue instead of working to solve the problem.
I don't want to know who the builder is, I want to know where you can get steel SIPs that have built-in roofing like that! I assume the builders bought them from someone else and I'd love to talk to them.
Nate,
Ah, no problem. That's not built-in roofing, though. We installed metal roofing on top of the panels. The seams, if caulked, can be waterproof, but we didn't want to risk it. The panels were manufactured by Precision Foam Fabricators.
Jeff,
You wrote, "The builders are claiming that this is how they have handled refrigeration/cooling rooms in the past, and they have not had condensation issues."
1. Walk-in refrigerators don't have windows.
2. Even if they had windows, the condensation would be on the exterior, not the interior.
3. The Delta-T would be different.
Thanks Martin (and everyone),
I have the PVC trim on now, so I'm gathering experiential data. I also read Martin's article on dew points and delta-t calcs, as well as the reference docs. It does not bode well for their solution. I'll ask where they've used this trim solution on those refrigeration units, and if they have specs or pics.
So a concern is that, if the seal is not airtight, or loses airtightness over time (as a double-paned window fails), then I'll get condensation. Since we've almost fully sealed the outside and inside, there will be no direction for this water to dry, so that water might sit at the bottom frame of the window. It won't hurt our building materials, but it could encourage mold.
The PVC trim might still have condensation, if the temperature drops enough. The dew point of my interior air is 48 degrees (67F and 50% humidity).
It was also pointed out to me that, even if the solution worked, the metal is still not insulated, and that is a major issue. There is 1.25" of steel x 164 linear feet jutting into my living space transferring cold (and heat) into that area. That's the equivalent of a 17 square foot hole in my house only insulated by PVC.
It does appear that the only true solution will be to remove the metal. Now to see if they'll do it.
"There is 1.25" of steel x 164 linear feet jutting into my living space transferring cold (and heat) into that area. That's the equivalent of a 17 square foot hole in my house only insulated by PVC."
Jeff, It's not quite that bad. Your math misses that the steel isn't very thick.
I understand what you mean, since only the edge crosses from interior to exterior, but since that 1.25" of steel is such a perfect conductor of temperature, there is very little difference along its width. So it acts as if the flat side is fully exposed to external air. A little hyperbolic, perhaps. :-)
Do you know, or can you measure, the thickness of the steel? With that, we could estimate the heat loss better.
It sounds like you understand what's going on better than the builders. But you need to let them get to the point where they understand that it's a real problem.
There's a calculator for pipe insulation thickness to prevent condensation here:
https://www.wbdg.org/design/midg_design_ccchp.php
It indicates that 0.75" thick insulation would work for you, although it seems a little overoptimistic compared to your results with 0.5" insulation and moderate outdoor temperatures.
As for mold issues, you might be fine--as long as there's nothing organic in there for the mold to eat, just being wet won't lead to mold growth. As long as it's clean metal and plastic, it can be wet and not grow mold. You just have to be sure it's well enough sealed not to get dust in there. You could end up with the metal rusting if it stays wet, but that could be a good thing--a way to remove the steel without taking the windows out! So if you end up putting foam over the steel rather than removing it, and do your best to seal it up, I wouldn't be too worried if you can't guarantee a perfect seal.
But I agree that removing the metal is the best solution.
Question just out of curiousity: does the interior eventually get drywall, or can the metal skin serve as the finished interior surface? I like the idea of being able to hang pictures on the wall with refrigerator magnets.
(P.S. to Martin: I've seen refrigerated rooms with windows--constructed for controlled temperature testing and lab experiments, not for food storage. But I agree with your broader point--that the company's experience might not be very relevant.)
Charlie,
The metal is about 2mm thick. It's a 3' by 3" piece of angle steel. After overnight temps of 38 degrees, it was dripping water onto the towels in the sills of every window. The metal maintains a temperature about 12 degrees above the outside temperature, so my interior dew point must be slightly higher than 47 degrees.
So far, the PVC moulding appears to be about 3-4 degrees above the metal on the 1.25" area where it overlaps the metal near the window. It did not condense on it last night. The vinyl edge on our windows also drops to that temperature since it touches the metal, too, but since that doesn't overlap, there is only a 0.5" edge that remains cold.
Thursday and Friday night the temperatures finally drop below freezing. I'll probably inspect underneath the moulding after that.
After two months of trying solutions, I'm becoming impatient for our builder to come to the conclusion on their own. If they were 10 miles away, I'm reasonably sure this would be fixed by now. But it's a less-common building solution, so there can be learning curves. I'm trying to remain reasonable.
To answer your question, we are leaving the interior walls and the ceilings exposed, and we're using magnets to hang clocks, kitchen utensils, pictures, and even curtains. That's surprisingly fun. I designed the plans to minimize the switches and lights in exterior panels. The only drawback is that rain sounds do transfer more through the material without the drywall attached. A heavy rain sounds like a white noise machine. Some may not like that. We do.
Jeff,
Speaking as a former builder who worked in a cold climate, I think you are being too charitable to your builder.
One reason that the problem you describe isn't very common is that most builders know better than to install a piece of angle iron that penetrates the building envelope.
Rough estimate--the R value between the surface of exposed metal in the inside air is something like R-1, maybe R-2 if you consider the fact that the unpainted metal might be low emissivity. Normalized to the same surface area, I calculate that the thermal resistance of the metal thermal bridge through to the outside is only about R-0.2. So it makes sense that the metal inside will be closer to the outdoor temperature than the indoor temperature.
So basically you have 17 square feet of, at best, R-2.2 equivalent. That's not a terrible heat loss--it's like having an old-fashioned double-pane window without low-e or argon, 3.2'x 5', or worst case, a single-pane window that size. Not terrible but not great either.
Martin, you are correct. I have been hesitant that they will just walk away from this issue.
One argument they continue to make is that doors trimmed out like this, with angle on the inside and outside, but broken in the middle, don't condense. And that's why they believe this solution will work. When I argue that it's not the same since the metal fully transitions into the living space, they disagree with me. All I need to do it cover the metal, and it will be just like those doors, they say. Charlie's explanation might help with that argument.
Charlie,
Thanks so much for those calcs and your explanation. No, not great, because I would never choose to have that type of window in our home. The physical metaphor will help when I explain why this is is an issue, even if we can somehow stop the condensation.
Details such as this help considerably. Thank you.
The solution is aerogel or similar products possibly.
http://www.aerogeltechnologies.com/aerogel-materials
idea #2- add evaporation materials to rehumidify the indoor environment.
idea #3- create mini ponds on the sills, add gold fish
idea #4- add a waterfall
idea #5- add hydropower to the waterfalls.
idea #6- bottle the water and sell as a natures drinking water
....
A,J,
I was reading a chapter on the history and making of aerogels the other night (in the book, "Stuff Matters"). Fascinating material. If they can get the costs of creation down, it would be a game-changer for insulation.
Results of the PVC trim solution (subtitle: well, that didn't work)
Temperature is currently 24 outside. Metal around windows is 34-36 at coldest. PVC trim is 42-46 at coldest.
There is a sheen of condensation on the PVC where it overlaps the metal, especially near the edges.
The vinyl around the edges of my windows also has condensation now where it touches the metal, so their PVC trim idea is definitely not a solution.
The casement handles have the most condensation. See attached picture. The bottom of the casement handle registers 44 degrees.
I've notified the builder that they need to remove the metal.
Thanks again for the discussion about our issue.
Followup:
The builders will be out in just over a week to remove all the metal from the windows. They admit it was their mistake so all costs are covered. I expected that, but glad to see it happening.
Glad to hear it. Not only do you get a better house out of it, but you've helped educate your builders.
Jeff, were you satisfied with the resolution of your condensation problem? What did they end up doing to fix it and did it work? I am thinking of metal SIPS myself. Thanks in advance.
Nina, they removed all of the metal around the windows and the condensation problems immediately stopped. No surprise to everyone here, I'm sure. Other than that installation issue, we've enjoyed metal SIPs. The span on our cathedral ceiling is dramatic, and it's comforting knowing that most of your house is resistance to water and insects.We have two Mitsubishi mini-splits in our home, but only the bottom floor 15K head ran this winter, The other never kicked on. It's upstairs, so it will likely carry the load this summer.
If you'd like to talk in more detail about it, please feel free to email me at [email protected]. After all of our research, I'd be happy if others benefit.
In your climate you must use thermally broken channels and if you remove the channels you have compromised the structural integrity of the window openings. Your base and top tracks if not thermally broken will telegraph the cold to the interior skins. The butt corner connections and the underside of the roof skins also need to be thermally cut to prevent the thermal bridge. If is was never done there is no way to alleviate the issue now. It may help to fur out with and airspace and apply drywall, technically the drywall is a code requirement anyway
I agree. The window openings, despite being reworked, do not have the integrity that they had initially. The base and top track are thermally broken so we have no impact there. The corner butt connections and the underside oft the roof panels also have cut, thermal breaks.