Condensation Issues with Flash and Batt Insulation

I got a big condensation problem at the moment and need any and all advice I can get.
Building a home in Southern MN. Zone 6. 2×6 wall cavity. 1/2 OBS sheeting on outside. 1.5″ closed cell foam R-10.5 and R13 unfaced fiberglass.
Inside is all rocked, and was on the last coat of mud, and we have had a cold snap over the last week bringing temps down to -10 or more. About 2 days into this cold snap on the coldest to date we noticed moisture at the bottom of the drywall between some stud cavities. This continued to get worse through out the day and in more locations.
House as being warmed to ~62 degrees, and sadly the humidity levels were around 60%. I cranked the temp to 70, and got two dehumidifiers going. I also didn’t have the house isolated from the garage at them time. Both were kept at the same temp. The following day I returned and Humidity was down to 52%. Condensation issues appeared the same or worse. I sealed the house off from the garage and today the humidity was down to 47%. I now have 2 more dehumidifiers (4 total) as I type this.
I had some exposed studs still and put fiberglass over them to see if things would condensate behind them, and although I’m not really seeing or feeling moister it feels borderline damp. I cut open 2 different spots in places that were wet, and to no surprise there was plenty of water at the bottom and the fiberglass was wet. (I cut about 3 inches up from the bottom).
We were very meticulous about caulking all framing, double, triple, top, bottom plates ect. Even caulked around ~1-4″ of each stud where the 1.5″ of foam stopped. So I really don’t think there is air leaks. Although I don’t see condensation or water at the bottom of each stud bay. That being said I got a good feeling if I cut into a dry one there would be.
This is my personal home. I’ve worked endlessly, and so has family. This obviously is very disheartening. I realize now I should of kept moisture levels under control without a doubt to start with, but I cant go back in time. I also now have concerns whether that would of been enough to begin with.
At this point here are my main questions that I’m hoping someone has stuck around long enough to answer.
1) What steps or suggestions should I immediately be doing. Example: Tomorrow morning do a, b, c, d, etc.
2) Is 1.5″ of closed cell enough for my zone and these temperatures?
3) If I had the RH in the house at 40% and walls painted. House at 70. Am I going to see these issues in the future with the setup I have. If we have cold snaps of -10 degree weeks?
4) I ask these questions because I understand or at least I think I do its because the temp of the foam is colder than the dew temp based on the RH and internal temp of the home. I’m also concerned because if I understand it correctly in theory with 70 degree interior temp and 35% RH I’m left with a dew point of 41 degrees and at 17 degrees outside the foam would reach 40.85 degrees which is less that the 41 degrees. I assume the drywall being painted helps helps reduce the amount of RH in the air in the wall cavity which further drops the dew point but I guess I dont know how much and its all got me extremely concerned at this point as anyone might imagine with it being my first home build and my own on top of it.
Thanks for taking the time to read everything. If you have any questions or important details that I overlooked please ask. I’ll respond asap.
GBA Detail Library
A collection of one thousand construction details organized by climate and house part
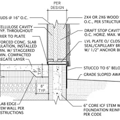
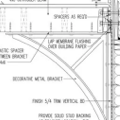
Replies
How long has it been since the basement slab was poured? This can be a major source of humidity for the first months. You are also adding moisture with the drywall compound. Open some windows slightly and let the super dry outside air help to dehumidify the house. This MN cold tests everything, tires, batteries, garage door openers.
Slab on grade home. Poured concrete about 8 months ago. Have the air exchanger, having HVAC guy actually hook it up asap to try and help as well.
Martin has an article here about flash and batt that might be helpful: https://www.greenbuildingadvisor.com/article/flash-and-batt-insulation. In it, he recommends at least 2 inches of closed cell in Zone 6.
You installed a vapor barrier under the slab and a capillary break on top of the footings, correct?
My eye was drawn to the sill plate in photo #2. It looks wet but maybe that's just an artifact of the image.
Your HVAC does not include a humidifier, correct?
Did you tape the seams on the OSB?
Vapor barrier under the slab yes. I installed sill sealer between concrete and bottom plate. Plate is wet but I think it's just the face and top there where the moisture had run to and sat.
No dehumidifier in HVAC went with just the air exchanger. Not opposed to spending the money on one if it's needed.
I sadly didn't tape the seams of the osb or caulk top or bottom. Had I learned that would of been a great idea before it was to late I definitely would have.
My membership expired so I can't see the whole article but the worst part is I could of sworn I used it as a reference when coming up with a game plan.
Any advice or knowledge on how I should proceed from here?
Edit not sure whether it matters or not but I am hearing via radiant heat through the concrete.
Doesn't the code call for 50% R-value outside the building envelope. The interior side of the sheathing is getting cold enough to have condensation.
It sounds like almost all the R-value is inboard.
A vapor barrier might have been helpful but none of them are ever perfect so something will get through.
Good luck. I hope you're able to sort this out.
There have been a bunch of similar questions lately, so please search the Q+A section for additional information.
62° air at 60% RH, when raised to 70°, will be about 45% RH, due to warm air being able to hold more moisture than cool air. But most hygrometers are calibrated to 68° so you probably started with even higher RH.
70° air at 52% RH will condense on surfaces cooler than about 51°. 70° air at 40% RH will condense on surfaces cooler than about 45°.
In climate zone 6, the IRC allows a class 3 vapor retarder (i.e., painted drywall) at the interior if you have at least 33% of the total wall R-value in the foam. (They state it differently but that's what it works out to.) They still require a vapor retarder, which should also be a reasonably good air barrier, because you can't have the room air freely circulating to the foam; you need to slow it down or you will get a lot of moisture accumulation. A bit of moisture can accumulate even if you follow the IRC guidelines but it should be minimal and not cause problems. The higher percentage of you insulation in the foam, the lower the risk of condensation, because the batts keep the interior warmth from reaching the foam, keeping the surface cool.
You can approximate what the temperature of the foam will be using percentages. You have about 40% of the R-value in the foam. That means, in a steady-state condition with 70° interior and it's -10° outside for an extended period, the face of the foam will be about 40% of the temperature difference, or 22°. 70° air would have to have only 15% RH to not condense at that temperature. Fortunately it's rare to have extended periods that cold; if a more typical extended low average temperature is 10°, the face of your foam will be about 34°F. To get the face of the foam up to 45°, which would need 70° air to be over 40% for condensation to form--generally a good threshold to plan for--either the outdoor temperature would need to average no less than about 28°, or you would need a higher percentage of foam in your assembly. Painted drywall installed in a reasonably airtight manner (assuming there is another air control layer in your assembly) and keeping the indoor RH on the low side should be enough to keep your condensation to a minimum.
Hey Mike thank you for response. I did actually read 1 or 2 other similar posts that had responses from you and were very helpful. It allowed me to much better understand how and when to expect condensation but I unfortunately just wasn't 100% sure I was understanding, and I had some more questions as well.
It seems as though my assembly meets code based on what your saying, or at least if it was painted it would. I actually used the vapor retarder electrical boxes on the exterior walls and for all intents and purposes planned on the painted sheetrock as a second air barrier. So I've stayed meticulous.
All that being said I guess I'm still unsure of whether my wall assembly will be successful or not despite it meeting code. In an ideal world the house would probably be at 68°F and if we go with 40% RH I should expect condensation on a surface of 42°F. If understand correctly the lowest the average temp outside could average no less than 25°F otherwise in theory it would condensate.
Does the painted drywall affect these numbers, and if so how?
Weather averages say MN Jan average temps between 7°F and 24°F all of which is below that 25°F.
Based on what your saying and the code says it appears as though I should be alright. If I stay on top of the RH in the house and its temperature correct?
Do I need to cut drywall open and try to help dry everything out first? I guess I'd love to get texture on and start painting asap like you mentioned, but I unfortunately have no idea whether or not my walls will fix themselves now that I'm starting to take control of the air like I should of or if I need to take a hands on approach to getting them completely dry first.
Thanks you for all the help so far and the information you have provided here and in the other posts.
Parker, you're welcome. Painting the drywall (or adding other vapor retarders) does not change the relationship of temperature, humidity and condensation. It just slows vapor from diffusing into the wall cavity. Drywall alone is a good air barrier but it does little to slow vapor movement. Air movement is a bigger risk, but over time vapor will diffuse through solid materials and eventually accumulate. How much vapor gets through depends on the material's permeability and other factors.
Calculating how much will get through is beyond my current skillset; it's best with any questionable assembly to run a hygrothermal analysis using software such as WUFI but you need an experienced person running it to get the inputs right.
Your assembly seems to be code-compliant but it would be safer to add a variable permeance membrane, which slows vapor transmission more than painted drywall but in the event there is moisture accumulation, the permeability increases to allow drying to the interior. I'm sure you don't want to tear off your freshly completed drywall, though. Alternatively, you could use a vapor-retarding paint instead of standard latex paint, to further slow vapor diffusion while still allowing some drying.
The wall won't dry to the interior when it's cold out, though; vapor is relentless in wanting to get out to that cold, dry air. Fortunately closed cell foam is somewhat vapor permeable so as long as you have a rain screen or your siding is permeable then the framing cavities will eventually dry to the exterior. (Hopefully you didn't wrap the exterior in an impermeable membrane or install impermeable cladding?) Meanwhile, keep running your dehumidifiers to slow the continued moisture-loading of high RH air, and keep the temperature turned up to help push the moisture in the wall through to the exterior and get paint on the drywall. My best guess is that those efforts will be enough but of course there are no guarantees.
Outside is wrapped in Tyvak and LP smart side siding. Do I need to be concerned about the OSB and siding?
Warm summer days are a ways away. I've obviously got no power to holding it against you, but it sounds like keep things going at this point. Keep RH as low as I can get it with temps at 70 or so, and everything should dry out appropriately all on its own in due time without permeant damage or mold growth?
I will look into the vapor retardant paint. I'm assume I can prime as normal. Apply a layer of this special paint and then go with our final preferred paint choice?
I unfortunately know we have another cold snap coming this weekend with lows of -20 and highs of 0. So that isn't going to help and is for me all the more concerned.
Parker, this is not something I assess closely every day so I'm mostly talking theory here, and can't predict exactly what will happen in your situation. That would require WUFI or at least someone who is more dialed into hygro-thermal action at low outdoor temperatures.
That said, your lack of a rain screen and a relatively low-permeance cladding are not ideal, but there should be at least some drying to the exterior through your siding. I have not applied or spec'd vapor-barrier paint so I don't know the specifics, I just know it exists. I imagine you can paint over it with something else.
I'm also not a mold expert, but I do know that the kinds that tend to grow in and on houses typically likes temperatures between 40-50° and 80-90°. I believe the interior side of your cavities will dry first, and as you get closer to the exterior it will be wetter, but also colder, probably too low for mold to grow.
Although warm air can hold more moisture than cold air, if you aren't introducing new moisture into the air, which you aren't, I think you can crank up the heat even higher than 70°--the warmer the interior, the faster the heat will push moisture through the wall.
Hey Sorry Mike have to respond up a couple replies as it looks like we maxed out the number.
Again cant thank you enough. Just playing with the dew point calculator it seems as though my only option to actually get things to dry out at this point due to temperatures outside is to potentially increase the heat like you mention but it seems like that kind of plateaus in regards to lowing my dew point vs getting RH lower by really hammering the place with maybe even more dehumidifiers or bigger ones. Raising the temp unfortunately doesn't raise the temp of my foam enough vs directly trying to lower the moister via dehumidifiers.
Still not sure whether my best bet would be to cut open the bottom of the sheet rock where base would cover it all anyway or leave it sealed is better either.
Thanks again, this is obviously all been very helpful for me and in the future for others or maybe even now as well.
Parker, in the short term, raising the indoor temperature is solely to push the moisture that's in the wall through faster, not to raise the temperature of the foam. Once you get a vapor retarder the cavity should start to dry out, because the rate of drying will exceed the rate of wetting.
I had a similar question once, with a double-stud wall with cellulose but the same moisture accumulation problem. I was trying to figure out if it was better to keep the walls open to allow drying to the interior, or close them up. I called Bill Rose, esteemed author of Water in Buildings (an excellent book that it sounds like you could handle--it's not for the light of heart) and asked his opinion. He did not equivocate; he said that moisture always moves toward the lower dewpoint. In your case, that will be outdoors. I asked if the cellulose is saturated, wouldn't at least the surface evaporate toward the interior? His response: "Always to the lower dewpoint." He might have said vapor pressure but it's basically the same thing in this case. That's when it gelled for me that if you're insulating in winter, you need to get the insulation covered as quickly as possible, because it will only dry toward the exterior--unless you can somehow get the interior dewpoint lower than the exterior dewpoint.
You're welcome, again--I wish I had more specific advice; I still consider myself a student of building science, even though GBA gave me the expert tag.
Parker, I may have lost this in all the numbers, but what temp is the face of your foam running (either measured or calculated)?
I'm curious what interior conditions you would need to get any inward drying. It is theoretically possible to dry to the inside if the inside reached a low enough dewpoint (lower than the foam temp), but I'm guessing that is unrealistic (you mentioned playing with a dew-point calc, did you come up with some numbers?)
I believe snap cold is more likely to cause condensation issues because it doesn't allow time for the interior air dewpoint to fall with the outdoor temp drop. In your case, you also have residual construction moisture, so that may not matter much.
The takeaway there being that if you bring outdoor air in, like Doug says, and then heat it up, you'll lower your RH pretty effectively. (Throw energy at it!)
The other takeaway perhaps being that RH controlled environments (specifically humidified) present unique challenges for this reason (no chance for interior dewpoint to naturally fall with the outdoor temps if higher humidity is imposed on it).
So Mike, are you saying that Parker needs to get the indoor (70 degree) humidity to below 40 percent?
Steve, I got wordy there, thinking "out loud," but yes, a 40% indoor RH is what I feel comfortable with. He also needs to install and paint the drywall. You essentially can't get the indoor RH low enough to prevent condensation when it's cold out, so the sooner it's covered, the better.
Parker,
The lack of interior drywall is probably contributing to this problem. More information here: "Condensation on Wall Sheathing During Construction."
Hey Martin we have all the drywall up and I used air sealing boxes on the outside walls. We are pretty much done mudding, except for spraying texture.
Only noticed the issue because water was soaking into and through the bottom of the sheetrock.
In your Flash and Batt article you recommended 2" I some how overlooked that number when originally deciding on the thickness of foam otherwise I certainly would of sprayed 2" instead of 1.5" Unfortunately my sprayfoamer also said 1.5" was enough and that was what I believe I'd found under my own investigation and didn't think twice.
Do you think if I proceed with caution from here on out. Get it textured, painted, air flowing, heat up for now, RH down as much as possible that in the future I shouldn't expect to see any issues, along with that my forever home isn't going to fail, have indoor air quality issues, etc?
Not sure if you read all of Mike and I's conversation but is there any additional or other advice you could suggest in how I proceed from here?
Thanks
Tyler I slightly overlooked Dougs thought of cracking the windows. Knowing what I know now I would of done that I think to help bring the RH down. That being said now I've the the air exchanger running consistently so at the point I am bring in that cold dry air to help.
I hadn't actually measured the temp of the foam. I will do that just so I have some real data numbers rather than theory.
Like you and Mike have mentioned and I agree I don't think its going to dry from the inside based on what Mike said.
It seems as though no one is overly concerned that the water that is in the walls will reck things before it was to say dry out once things start warming up, but as a home owner, building my first home, it being the forever home, and not knowing all that water in there just makes me so nervous my walls are gonna mold and fall apart lol. When you dont know you fear the worst, or at least I can tell you I certainly do.
Parker, wood is a resilient material. It can get wet and as long as it dries before wood-eating fungus takes hold, there will be no lasting damage. Framing is often rained on for months during construction. Fiberglass doesn't mind water. Foam obviously doesn't care. Drywall can get wet and dry; in fact that's how you make it conform to curves. While you do have a problem, as long as you get it dried out soon I really don't think you need to worry. Cracking a window is an excellent idea--this isn't a time to worry above saving energy.
Hey Mike what would your definition of soon be in this case? As based on the theory here it seems as though it could take a while (months). Basically until I start getting some warmer weather out which most likely wont start until late March maybe early May?
Is that to long? or do you think it will dry out sooner if I keep with the plan we have described above even with the cold temps?
Parker, I'd need to "level up" to be able to calculate how fast your wall will dry. I believe that if you crank up the heat, open windows and/or run a dehumidifier that your wall will dry before damage can occur or mold can take hold. The colder it is outside and the warmer and dryer it is inside, the faster it will dry. (Assuming a vapor retarder of some sort on the drywall--at least standard latex paint, and preferably vapor-retarding paint.) I'd guess it would dry in a month or less but I could be off.
Haha well by the sounds of it when you've reached your level those level up's take some time :P when you young and got so much to learn like me the amount needed is very little to take care of these early levels.
Well unless someone comes in with different advice I'll look to get the rest of the mud on, get the walls textured, and painted. Obvious all of which are going to induce more moister but I'm thinking it should all be okay with the heat, air exchanger, and dehumidifiers going and at which point when its done things will hopefully dry out even quicker. Doing it all myself with the help of my dad mostly so we are a little slower that a full crew doing it day in and day out but we should be able to get it done here in the next 2 weeks or so.
If you got any final advice or if anything I just stated sounds bad let me know. Again and again. Cant thank you enough for the time, knowledge, and advice you have bestowed on me.
Parker
Whether its worth mentioning or not this is happening on the North facing walls. Dont see water at the bottom of the walls on the South, East, and only one spot on the West. If I had to guess there is moisture and condensation on all the walls but the North side seems to have the most or enough that that the fiberglass is wet/soaked enough its letting some run down between it and the foam, and exposing itself at the bottom.
I think the moisture issues are temporary and will go away once the indoor humidity level has been reduced. Fortunately we have had this cold weather in MN to test the systems once again. My indoor humidity is below 25% right now in MSP and this house is right at 3 ACH50. Construction moisture has kept the humidity level high, concrete takes a year or more to be fully cured if I remember correctly. You could be getting some condensation on the inner surface of the SPF due to the current outdoor temperature and the high indoor humidity. To hear most of the moisture is showing up on the north wall tells me you are right at margin of getting the indoor humidity level under control. We have had brilliant sunshine the past few days and that will warm the sun exposed walls slightly and short circuit what you are seeing on the north facing walls. You will not get much drying to the outside with the wall system you have used. OSB has a low perm rating and the SPF will add to that. Your drying surface will be the drywall so the choice of interior finishes should be thought out.
I use one of these to test moisture in native grass seed. It has a probe that could be inserted low in the wall where the base trim will go. You could monitor for a while the moisture level in the stud space to see what is happening. There may be a home performance specialist somewhere near by you that has one.
https://www.abqindustrial.net/store/moisture-meters-c-107/delmhorst-moisture-meters-c-107_113/delmhorst-f-2000-pkg-digital-moisture-meter-for-hay-deluxe-package-p-1704-op-2120_10220.html?gclid=Cj0KCQiAyJOBBhDCARIsAJG2h5f0U-sfGu3DReKhCNhgqLDhkUecF5zsCZ5onOT5CmkTGQYvoLGve3caAgxfEALw_wcB