Condensation in the seams.

So I was working with a client last year to remodel their attic space. So we took the strategy to insulate the knee wall by using 2″ foil faced polyiso foam board on the attic side, R-15 batt with a kraft paper face in the cavities and drywall on the conditioned side.
The homeowner is just getting around to sealing the seams in the foam board and is noticing condensation in between the pieces of foam. It is 30 degrees out today in zone 5a. So I am trying to assure the client that he is seeing this condensation because the seams have not been sealed and he should not have a problem once they are sealed. He is primarily worried because a contractor told him with the foil facing he will get condensation on the foam board. Any advise on how to put the customer at ease?
GBA Detail Library
A collection of one thousand construction details organized by climate and house part
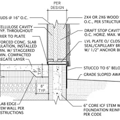
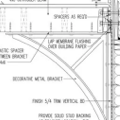
Replies
Condensation is occurring because warm air is meeting the cold air through the seams. It would be my guess that the wall isn't fully air-sealed, possibly from under the floor or other gaps as per AJ.
Joshua, All I know is I would not put together your exact detail without getting one of the building science pros to detail it properly for your climate and exact build.
Where is your moisture coming from, inside warm air leaking past unsealed outlets in the knee wall? Seal up your drywall much better is what you should do. Then you could make the knee wall deeper by extending the studs, net it and dense pack cellulose.
If you stick with the situation you have, tape it and caulk it perfectly and if you can add another layer of foam over it and do the same, tape and caulk it perfectly. And no matter what you have, do go in the room and caulk and seal the bottom edge of all wall drywall, and get all your outlet penetrations sealed, etc.
If the homeowners are using a humidifier, they may need to use it less or not at all. If they don't run properly installed bath fans always and for enough time via a timer switch after they use showers, then that needs to be addressed.
Making a home tighter, adds other items that must be addressed, If not there is a large chance that you are causing more harm than good.
Shane, that is my guess because the gaps are anywhere between an 1/8" to 1/4". So the cold air is just getting into those cracks, mixing with the warm air moving outward and condensing. So filling the gaps with foam is the first step to stop this.
Is the polyiso foamed or taped together to be monolithic? Is the drywall installed and taped?
The drywall is taped and with first coat of primer. And no, the polyiso is not currently foamed and taped together. It is the gaps where the condensation is forming.
So this condensation can be seen from inside the side attic spaces? Did you blower door test this house, and if so, how well isolated are the side attics?
Yes, the condensation can be seen from in the attic in the gaps between the pieces of polyiso. And this is just a remodel/design client. So no blower door, it was just design work. But I guess the last time I visited the progress they just had a piece of batt insulation covering the knee wall hatch. So that could be letting in a lot of unnecessary moisture into the knee wall space. So to answer your question, currently they are not very isolated.
By the way, thank you David! Based on your question I just remembered that besides no real attic hatch, the client has been painting and laying tile. So this activity is increasing the moisture levels in the new master suite that is causing the condensation. So I will get them to run the bath fan while working and make sure they seal up the gaps.
Mr. LLOYD,
I am pretty sure that if you seal all of the foam with a urethane caulk and then tape, that your problem will be solved. It's not that bad. Maybe figure a better way to seal the door as well.
Thank You
The end result of the work is hopefully that the attic spaces are outside the thermal and pressure boundaries of the house. They need to be cold and dry. If they are connected to any significant degree to the interior of the house, then humidity will migrate in there and condense during cold weather. Right now the moisture you see is probably just leaking thru the big holes from the interior, and once that stops you need to look again and see what is happening. I have seen fantastically expensive homes where the attic doors were leaky plywood or drywall panels with no weatherstripping or insulation. A piece of batt insulation is worthless as a side attic door. A typical panel with some air leakage around it is questionable if you have a cold space behind it. Someone needs to remember to check in there later and make sure out-of-sight/out-of-mind is not funky and damp.
I understand that you are the designer and not the contractor, but IMO there are many times that a blower door and other test tools are just about mandatory. If I were remodeling that house I would run a blower door test (or more than one) to make sure the side attics were well isolated from the house, and I would probably leave dataloggers in the side attics for a week or two during different seasons to make sure that RH was low and the spaces were dry. If you can get clients to hire contractors who understand this stuff and have the right tools... then you can avoid worrying about it.
Zone 5A is heating climate, so the vapour barrier should be room side. From your description it's unclear to me that this is the as-built. Foil face will act as a vapour barrier if the seams are sealed. In a normal wall build, the GWB would be room side of the vapour barrier , which is over studs and insulation. Is this what you have Joshua?
Joshua,
1. Foil-faced foam is OK in your climate in this position.
2. The main problem is that the installer forgot to use canned spray foam to seal the seams between the sheets of polyiso. It's also possible to use caulk plus tape, but gaps are a no-no. Two layers of polyiso with staggered seams are always better than one layer -- but if you have only one layer, you had better pay attention to sealing the seams well.
3. As several posters have suggested, the problems may be exacerbated by high indoor humidity and a bad air barrier at the drywall level.
Since the moisture is at the seams it is telling you the walls are leaking air. As it passes through the wall and out the crack the air is leaving its vapor behind. Seal and then double check and seal again.
How was the attic floor sealed. Was the air barrier along the floor and up the wall made continuous? Was the floor insulated? Is there attic venting?
Robert H,
Clearly, the moisture is coming from the heated side of the drywall, not the attic side. That's why it's condensing at the foam seams -- the first cold location.
If the moisture were coming from the cold (attic) side, there would be many other places for the condensation to occur first. In any case, cold air isn't very humid.
If there are air leaks, they are likely at the drywall on the warm side of the kneewall, or through penetrations in the kneewall bottom plate.
Well it was just confirmed today that right now the knee wall hatch is only a piece of batt insulation stuck in the hole and the homeowner keeps the relative humidity in the home between 50-65%. So pretty elevated.
So it has been advised that they foam the seams and add foil tape over that and to get a proper insulated hatch with weather stripping.
And just to answer Roberts question. The knee wall floor (attic floor) has 15" of cellulose. And the knee wall slope does have a 1" air space and insulated baffles were used, made out of the same 2" foil faced foam. So under the finished floor there is not insulation, and the cavities were suppose to blocked off.