Condensation Between Perforated EPS and Rockwool

Hi all, I’ve run into an issue with my converted garage re-build. All walls are above grade block walls and there is another brick wall on the outside (not sure what is under the brick). I am in climate zone 6b, Southern Ontario.
My plan was:
A) 1.625″ Continuous SilvRboard graphite XS (perforated) on the block wall, glued and taped at the seams. (R 7.5)
B) 2×4 stud walls with R14 Rockwool.
C) Membrain smart vapour barrier.
I assembled the SilvRboard wall and the 2×4 stud walls and filled them with Rockwool; however, I didn’t get around to installing the vapour barrier right away as I was waiting for some trades to come in and do their thing.
As I was getting ready to install the smart vapour barrier, I removed a piece of the Rockwool and found that the EPS wall underneath the rockwool was absolutely DRIPPING with condensation. I removed a few more pieces and, long story short, all three exterior walls were soaked with condensation. Water was literally running down the walls ( except for the interior wall connected with the house).
Did I screw up by using the perforated EPS? I’ve done assemblies like this before, in basements, but I’ve always used XPS.
The other thing I’m wondering about… at one point the relative humidity in the converted garage unit was ~65%, largely due to, I think, some 1950’s single pane windows that I was waiting to get replaced. Since I’ve replaced the windows, I’ve managed to get the relatively humidity down to ~40% in the unit.
Was the humidity simply too high, causing this crazy condensation? Now that I’ve got the relative humidity under control, should I proceed with my plan of Rockwool + smart vapour barrier? Or should I forgo the Rockwool entirely and try and spray foam the SilvRboard?
Thank you for any help.
GBA Detail Library
A collection of one thousand construction details organized by climate and house part
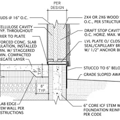
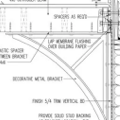
Replies
Are you SURE that water was condensation and not bulk water seeping through the foundation walls? Bulk water is an entirely different issue that has nothing to do with how you insulate.
I would expect the level of condensation you're experiencing, but if the conditions are right I suppose it's possible. I have used straight EPS insulation before, which is somewhat vapor open (at least compared to similar thicknesses of XPS or polyiso), and the "perforated" part is probably just a poly facer, so what you have is no more vapor open than regular EPS would be.
If this really is condensation, then the surface of that GPS you put up dropped below the dew point of the air in the basement. There is no other explanation, that's just physics at work. You have two solutions to that problem: either raise the temperature of the first condensing surface, or lower the humidity levels in the basement air. To do the first, you need to either get rid of the rockwool, or put up a thicker layer of GPS. The temperature at the surface of the GPS will be determined by the R value ratio and the temperatures on either side of the insulation stackup. In your situation, assuming a foundation wall temperature of 50F and 70F basement air temperature, that R7.5/R14 mix will put the inside surface of the gPS (the interface between the GPS and the rockwool) at just shy of 57F. If that's below the dew point of the basement air, you'll have condensation forming.
To do the second, you need a dehumidifier. That will take energy to run, so it will be an ongoing operating expense compared to the one-time expense of a thicker layer of GPS.
Bill
Hi Bill,
Thank you for the reply. That makes a lot of sense and it's very helpful to see the numbers written out like that.
As for the bulk water concern, I'm fairly certain it's not seeping through the walls. It's not a basement, but a converted garage, so all the walls are above grade. Also, when I removed all of the rockwool and wiped down the GPS and let it dry out, there has been no more water/condensation (the rockwool is currently sitting in a pile in the middle of the room).
So if I'm understanding this correctly, since I've replaced the windows in that room and lowered the relative humidity down to 40% (from 65%), I've also lowered the dew point. Before, it would have been ~13 degrees C and now it is closer to 6 degrees C.
I'm going to re-install a few sections of the rockwool and monitor for condensation now that I have reduced the RH of the room. Thank you again!
Take a look at table 2B here:
https://www.appliedbuildingtech.com/system/files/abtg_rr_1701-01_moisture_control_guidelines.pdf
In your case, you had an assembly with a mix of rigid and fluffy but no vapor barrier. Based on the table, for condensation control in Zone 5, you would have needed much more rigid insulation (ratio of 1.3 instead of 0.2).
In the case of R14 batts, that is 14*1.3=R18.2. Which is a lot of rigid insulation. Add in high humidity which just makes this even worse.
Your wall will work fine once you get a vapor barrier up.
I would try to get the moisture out of first and reduce your interior RH as low as you can get it. Assuming -10C outdoors, 20C inside, you want the RH to be around 30% to avoid further condensation.
Thank you for that link -- it looks like a great resource!
Good point! FYI - after a year in which I had added 6" of EPS to the exterior of a customer's 1920 house (real 2x4s and balloon framed which had cellulose blown into the walls in the 80s) I was asked to tear out a wall for some interior work. Once the plaster & lathe was removed I was able to look at our job from the inside. The cellulose and sheathing (1x8s) was bone dry. It had been below zero all week and the humidity in the house was about 60%. They love their big plants and making lots of pasta for the kids... Life is good when you do it right.