Condensation between fiberglass and closed cell foam. Should I wait for it to dry out before drywalling?

I recently insulated the second floor of my renovated Cape Cod to create a conditioned attic. My house is in Maryland (climate zone 4a). The roof is a flash-and-batt job: about 2″ of closed cell spray foam applied directly to the underside of the roof sheathing and R-30 fiberglass batts between the rafter bays. Most of the walls have R-5 closed cell insulated sheathing on the exterior and R-15 fiberglass between the studs.
I was getting ready for the drywallers to show up this week by going around fluffing the fiberglass when I noticed that the back (cold) side of many of the fiberglass batts are wet! I pulled a few out of the rafter and stud bays and there’s visible condensation on the foam. It’s my understanding that the foam is supposed to ensure that the inside air doesn’t reach dew point but I’m starting to doubt that now. Of course, I also understand that the insulation is supposed to be protected by an air barrier and since the drywall isn’t yet installed, inside air is able to sneak between the batts and carry lots of moisture to the cold spots.
My questions are:
1. Will the same thing happen every winter once the drywall is up? I imagine the answer is, “do a good job of preventing air from leaking past the drywall layer but know that some inside air is going to get through and could condense on cold spots.” I figured I’d ask anyway.
2. Why isn’t the foam preventing dew point? The back of the fiberglass was cold when I took it off. It it possible not enough heat gets through the fiberglass to warm the foam enough to prevent dew point?
3. Since things are currently wet, should I wait until spring weather to arrive to dry everything out and then drywall? If I drywall now, will all that moisture definitely dry to the inside by next winter?
4. Finally, there are a few spots where the spray foam thickness on the roof is as thin as 1 1/4″. Most of it seems to be around 2″ but I’ve read here that average thickness doesn’t matter; everything should be at least the minimum required thickness. Should I actually get my insulation contractor back out to take down all the fiberglass, spray more foam, and reinstall the fiberglass? He’d hate me, I’m sure, but it may be worth it if the thin spots are the reason for condensation and if it’s too wet to dry out in warmer seasons.
Thanks in advance GBA geniuses!
GBA Detail Library
A collection of one thousand construction details organized by climate and house part
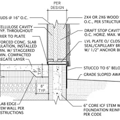
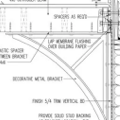
Replies
Mark,
In your climate zone (Zone 4a), building codes require (and building scientists recommend) that a flash-and-batt job for an insulated roof assembly have a spray foam layer with a minimum R-value of R-15. Here is a link to an article that explains the principles and code requirements: How to Build an Insulated Cathedral Ceiling.
"About 2 inches" of closed-cell spray foam is probably rated at R-12 if the layer is really 2 inches thick. Clearly, that's not enough. In the thin areas that you describe -- the areas where the foam insulation is only 1.25 inch thick -- the foam is only rated at R-7 or R-8. So the condensation is no mystery. Your spray foam layer is too thin -- it doesn't meet code, and its thinness is contributing to the condensation problem that you are observing.
If I were you, I would call the flash-and-batt contractor and explain these facts to him or her, and request more spray foam.
That said, the addition of drywall will reduce the amount of condensation you are observing.
Here is a link to an article about this type of roof assembly: Flash-and-Batt Insulation.
There's no such thing as "preventing a dew point". Dew point refers to the saturation temperature of a body of air. The relevant body of air is the interior air. You can raise or lower the dew point of your interior air to adjust the moisture content to dry it out.
The moisture accumulation is due to the lack of an interior side air barrier with the air-permeable and highly vapor permeable batt insulation, giving free access to the cooler foam/fiber layer. The wall foam is plenty thick enough- the IRC code prescribes a minimum of R5 on the exterior of 2x4 framed walls even for zone 5, and you're in zone 4. But the code prescriptives also presume a vapor retardency of less than 10 perms, the maximum defined permeance of Class-III vapor retardency. A single layer of latex paint on wallboard is about 5 perms, but the vapor permeance of naked batts is north of 50 perm, an order of magnitude difference. That means in just one week of cold weather as much moisture gets in through the batts that it would take a whole winter to accumulate through a layer of paint on wallboard.
http://publicecodes.cyberregs.com/icod/irc/2012/icod_irc_2012_7_sec002_par025.htm
It'll dry out even in winter if you ventilate or dehumidify down to 15% RH @ 70F (= 21F dew point), and / or heat the place to 80F for several days before closing it in. If you want to speed it up, pull the batts and re-install them the day before you put up the wallboard.
At the roof deck you have about R12-R13 out of a total R of R42-R43, or about 28-30% of the total. IRC chapter 8 prescribes R15 minimum, out of a presumptive R49 total, which is a bit over 30% of the total. Fiber insulation is also presumed to have an interior side air barrier (which you apparently don't yet have?), but not necessarily a vapor retarder. That means that at the full 2" you'll be marginal but OK after you dry it out, especially if you paint the ceiling to lower it's vapor permeance to ~5 perms. But thin spots would still get damp even with 5 perm paint.
http://publicecodes.cyberregs.com/icod/irc/2012/icod_irc_2012_8_sec006.htm
To fully meet code for total R-value you'd need at least 2.5" of closed cell foam + R30 to hit the R49-ish range, not just 2", and that would also improve your dew point margins to something more like the code prescriptives for 4A.