Compressive Strength of XPS for Steel Building

I will try to keep this brief, but I wanted to explain a bit of the process in hopes it may help someone else, or someone can poke holes in the design.
I am in the process of building a steel building. The building has steel girts and purlins. I wanted to do something to remove the thermal bridge between the outside metal panels, and the steel girts. To do so, I want to sheath the building with 1″ foam board and then put the metal paneling on top. To achieve this with less hassle, I am planning on building “foam panels”. I found some second-hand house wrap, so i plan to lay the wrap down, then (lightly) glue 4×8 sheets of foam down to the house wrap, sealing each joint between boards, making an 8′ wide panel the exact height needed for a wall (18′ in this case). I can the set the panel up against the wall, put up some temporary support, and then screw wall panels on top. I will leave house wrap on either side of the panel to allow overlap with the next panel. After the panels have been assembled, I can go back from the inside and seal between the panels with can foam.
Next, i wanted to do something similar with the roof. I figured it may be beneficial to go with something a little thicker, so I decided I would do the same thing only use 2 layers of 1″ foam, staggering the joints in my “panels”.
Finally, (but chronologically, first), I have made glued 2′ tall 16′ long panels out of 2 layers of reclaimed 1″ foam to insulate the buildings footing/stem wall (I am not putting foam under the floor, just insulating the perimeter with 2″ foam).
Everything I have done has been with Foamular 150 (15PSI) insulation so far. However, I got to thinking, will this lower compressive strength foam be a problem in any of these applications?
In my head, it seems that I don’t need a ton of compressive strength for the walls of the workshop. Guys regularly use those rolls of fiberglass batts and double bubble, both of which I consider “squishy”. I am hoping the 15PSI foam works better without oil canning the panels.
The foundation lining seemed okay as it is not underneath any of the load bearing surfaces, it simply lines the sides of the foundation. Documentation online seemed to make me thinking 15PSI was sufficient.
Perhaps my bigger concern, is the roof. Is 15PSI foam okay for this application? Keep in mind, the foam panels will sit directly on the purlins, then the metal panels on top. Do I need to put some kind of support board in my panels to sit against the purlins and distribute the load?
I’d be interested to hear peoples perspective on this plan.
GBA Detail Library
A collection of one thousand construction details organized by climate and house part
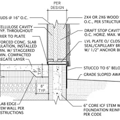
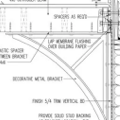
Replies
Midwayman,
Aside from the question of what your climate zone is, my first question would be "has an engineer approved this idea?"
What you are attempting is rather like imitating ZipR panels which are subject to strict fastener requirements to ensure racking control for wind loads. I am not remotely qualified to say if steel buildings get all or most of their wind resistance from the purlins or girts, but I suspect the panels play a significant part in making the building wind resistant. You are drastically altering the construction detail as designed.
An 18' high wall infers a sizable building with lots of wind exposure. A barn structure quite near to me went down thanks to winds and improper bracing of the trusses. Not even very high winds. I would urge you to contact the steel building company immediately as both they and your current insurance company will very likely not pay out any claims if you get creative without certified plans.
You may also be creating moisture issues for yourself depending on your local temps and humidity.
Yes, the steel building company engineered this building with the 1" foam in walls and 2" in the roof. I am unsure what that did in terms of changes to the design, but the drawings are stamped with this information included.
I am curious, however, how this would be different, than say, the fiberglass roll insulation you see regularly. These products also space the exterior panels away from the framing material (to some degree).
I am curious why you suggest moisture issues? I am using housewrap (air barrier, not vapor barrier) on top, then foam (moisture barrier - mostly), then fiberglass batts (no kraft paper). The vapor barrier would be on the outside only.
I'd like to hear if there are reasons to reconsider.
Midwayman,
I would be concerned about the compression on the roof purlins too. We don't put foam down directly on rafters or trusses without a layer of sheathing, and Huber acknowledges the possible problem by not certifying Zip for use on roofs. What I don't know is what spacing of purlins would mitigate the concern.
Midwayman,
Good thing to know engineering has been done for the thickness. Even Foamular 150 would compress far less than fiberglass roll. The fasteners will act more like trees the thicker the insulation, so the bending and flexing goes up unless engineered for. The thinness of the insulation suggests you are in a mild climate with lows typically above freezing. If that is not the case, your humidity concerns will be driven by local weather and whatever activities you plan for inside the building. Working on tractors and trucks doesn't usually generate a lot of excess moisture though the air can get a bit heated up when one drops a wrench or worse.
The roof can still get plenty cool on the underside of your 2" foam layer if it is down to 30. Unfaced fiberglass batts are quite vapor open so interior moisture will pass through and condense on the back side of the foam. You will have a high potential for results similar to basements with batts against concrete. Soggy batts over time. The foam will behave as a barrier going outward and if taped off properly a bulk water barrier for anything getting past the metal siding. The purlins and girts will be at risk if covered with batts and no moisture control.
If you are housing animals or growing plants your interior moisture loads will tend to the high side even if ventilated. If comfortable temperatures inside the structure are not the goal you can go the path of many farm structures that first protect against rain and wind and only temper the summer sun a little bit. A few drips off the underside of the roof spring and fall would be the trade off.
The details you provided about the foundation suggest you are aiming at establishing comfort for year round occupancy by people. I am sure others could weigh in more effectively if your climate and occupancy goals are made clear.
It sounds like you're taking a bit of a DIY approach to the insulation, but if you want to get a thermally broken system that is more typical for metal buildings, I believe you want a "liner system" with "thermal blocks". Here's an example: http://therm-all.com/optiliner-banded-liner-system-ls/
Edit: here's a slightly fancier system that has a believable air barrier! Rare in a metal building! http://therm-all.com/max-tight/
Yes, this is definitely a DIY approach to the insulation.
I am in Missouri, and we see freezing winters and hot summers. My goal for the foam is not to be my insulation exclusively, but more as a thermal break and bulk water barrier for the exterior panels as well as a moderate exterior vapor/air barrier.
There seems to be some concern about the vapor barrier on the exterior of the building. It was my understanding that more modern approaches to insulation, in areas such as mine, mitigate the need for a vapor barrier as the reversal of the "vapor side" of the wall changes with the seasons (in an area such as mine).
I have seen similar (nearly identical) wall stackups for wet basements.
concrete wall (wet) | foam board | framing + batts | drywall
Is this not advisable?
I want to be able to climate control this like a home, and want to put all the pieces in place to make it as efficient as possible. There will be months a time this building will be used all day during the summer and winter.
Thanks for the information so far.