Commercial garage conversion

MishaB
| Posted in Energy Efficiency and Durability on
Hi everyone,
I hope you and your families are safe.
Here’s the project:
Context:
Location – Toronto area.
The project is within a low-rise apartment building complex. We are converting an attached 2-car garage into a small office space for staff, and it will be used by two people. It will be heated and cooled by a mini-split.
I attached a sketch plan showing the existing and the initial plan.
The garage is attached to apartment buildings on two sides with a firewall.
The garage is the second storey of a two-storey structure – it is located over another garage that is accessed through a lower grade on the opposite side, so the floor is not on grade but it will need to be insulated.
The floor is concrete slab; the walls that are shared with the buildings are concrete block, and the exterior walls are concrete block with a brick face. The roof is 2x4s 16″ OC with plank sheathing and a flat roof. There are no known water penetration issues.
The existing openings are the garage door and two windows at the back.
Since this a renovation and not new construction, we won’t need (or be able to) meet code requirements for new construction. The intent is to get the best performance given the limitations and minimize the risk for building failures.
These were the major considerations for the current design:
- The insulation will be done on the inside for continuity, simplicity and speed (which is critical here).
- The garage door will be replaced with a storefront system – this is mainly a consideration of speed and simplicity. The glazing will be fit into the existing wood frame of the garage opening.
- Since the storefront glazing will occupy a large portion of the building envelope and limit the overall energy performance, the level of insulation in the opaque parts will quickly reach diminishing returns.
The big questions (and I also welcome any other comments you may have):
- Do the proposed assemblies make sense in terms of preventing condensation and water damage?
- Do the proposed insulation levels make sense?
- In the walls, how much should the insulation continue from the exterior walls?
- In the ceiling, is it safe to cover the existing joists with spray foam, or would it prevent any moisture that penetrates the assembly from drying to the inside?
- Should the existing windows be replaced and lined up with the new insulation?
- Any recommendations for storefront systems that have a good performance/price ratio?
Your help is greatly appreciated!
GBA Detail Library
A collection of one thousand construction details organized by climate and house part
Search and download construction details
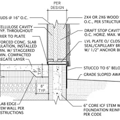
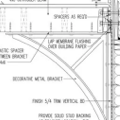
Replies
There should be no problems with covering your celing with 3 1/2 of SPF. Anything more than 2" is a true vapor barrier, the only moisture that could get in there is from roof leaks.
You get somewhere around an R14 roof, which is not the greatest.
I would be temped to cross strap the ceiling with 2x3 and spray closer to 4.5" of foam to cover the rafters (spraying 2" of closed cell followed by 3" of open cell would be much better but your installer might not want to do this). This would be a much higher assembly as there is now a thermal break over the rafters.
For the metal stud walls, make sure to space them off and only spray foam into the gap. With the thermal bridging of the metal studs you loose something like 60% of the R value of the foam. It is a slight loss of interior space but much higher performance.
Will all the SPF and new glazing, this will be a pretty well sealed building, make sure to get an ERV/HRV in there as well.
With an unconditioned garage bellow, the floor in there will always be a bit cold. If people are working in there is shoes, it should not be an issue, but if you want barefoot comfort, I would bump up the floor insulation or add in some floor heat.
Thank Akos, that is very helpful!
If covering the rafters should not be an issue then the cross strapping sounds like a good strategy. Btw, what would be the advantage of 2" closed cell + 3" open-cell over 5" closed-cell (besides materials cost)?
For the walls, yes, the studs will come over a continuous layer of insulation.
The floor insulation probably could use some improvements. I'll look more into it to figure out if we can add another 2" EPS board without running into issues with clearances.
Do you have a recommendation on how to decide how far to continue the insulation where the wall transitions from exterior to interior? I want to avoid thermal bridging, but insulating too much of the interior wall would be wasteful.
Brick is around 0.8R/inch. So if you have an R15 exterior wall, insulating back to about 2' should cover any losses through the brick. Don't know what the interior walls are like on the other side side of the brick, but if is an unheated/partially heated building, I would continue the insulation.
The the ccSPF/openSPF combo is mostly for cost, plus more enviromentally friendly. Since the spray foam is applied against wood, the R value of both assemblies is the same.
For the floor, I would use roofing plyiso. This is usually 20PSI and a bit higher R value per inch than EPS.
For the amount of floor insulation. The horizontal air film above a floor is around R1. So the the floor temperature is the ratio of the air film and flooring R value.
For example when it is -10C bellow and 20C room. With R10 the floor would be about 3C bellow room temperature. With R20 about 1.5C. The best would be to get some fluffy insulation bellow the floor and stick to 2" above.
Thank you!