Commercial application of Larsen Truss system?

Has anyone seen an application of the Larsen Truss system in a large scale commercial setting? Is it called something else?
I’ve had great success using the system in smallish multi-family settings but I’m not sure how well it scales up.
Ive been asked to informally consult on a proposed high efficiency hog barn build.
High moisture and high air turnover.
Proposed wall system is 2X6 structure with plywood sheathing on the interior with a thick coating of spray-on air sealer. Larsen trusses applied to the exterior with dense pack cellulose, horizontal strapping, house wrap, 3/4” vertical strapping and the steel siding.
The competing conventional system is a 2X6 structure with spray foam in the cavities and poly panels on the interior.
VERY short structural life with LOTS of moisture problems.
GBA Detail Library
A collection of one thousand construction details organized by climate and house part
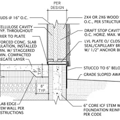
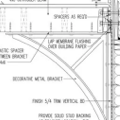
Replies
What exactly does 'high efficiency' mean when you have as a requirement 'high air turnover'?
What climate zone / location is this?
Have you done the math to see, given your required ventilation rates, whether heat loss through the walls is significant or negligible by comparison? Typically in residential building, we are examining systems where interior body-heat and moisture is trivial compared to the impact of outside weather (with brief periods of bathroom usage or reducing cooking stock being the exception); That may not be the case here.
What's the packing density of the hogs, and how much body heat and moisture and CO2 and odors are they producing, and what sort of ventilation rate does that lead to? This is going to be partly dependent on your chosen manure handling system, I think - which bottlenecking variable actually sets the requirement?
How big is the building?
I assume given typical butchering sizes that one head of swine will approximate the body heat & moisture production of one human being.
As you scale up a building and the walls/ceiling enclose a larger and more useful volume, even fairly silly possibilities start to become practical about the perimeter walls & roof because of the square to cube ratio. If you're dealing with extreme moisture issues, for example, building a double wall with vapor barriers on both sides and conditioning an air gap between them for dehumidification, might end up a feasible tradeoff.
If you're looking at severe winter temperatures, given high ventilation requirements, the first thing I would ask is - have you examined ERV/HRV options? A heat exchanger pumping exhaust-air-heat back into a heat exchanger at the intake fans, for example, would let you save a significant fraction of your energy requirements.
We’re in central Canada. VERY cold winters.
There will be a lot of engineering to determine the optimal air changes with the biggest factor being the ammonia off gassing.
My understanding of the shortcomings of the conventional 2X6 and sprayfoam construction is that faults in the foam will concentrate the moisture load in the framing members and lead to a cascading cycle of further failures in the foam and greater concentrations of moisture, etc, etc.
I think the savings in heating costs will be important but the bigger advantage could be the longevity of the structure. When the inevitable penetration or imperfection in the air sealing occurs, the cellulose will pull the moisture away from the structural members instead of concentrating it there.
There should be a thorough round of modeling to compare the options but even that is a hard sell out here. With electricity rates at 3-4 cents/ kWh for large customers we are behind the curve on efficiency.