Cold living room floor

So, like many people, I have a cold living room floor above my garage. I have begun to pinpoint several areas of major air leakage to address (thanks to renting a thermal camera from Home Depot). One major issue that I discovered (and already suspected) was that the garage ceiling has very poor insulation. I have a second story bay window cantilevered above the garage door (garage townhome). This past summer I had to have the bottom paneling replaced due to wood rot. While the contractor has the old wood off, I was able to peek into the framing (also discovered no insulation in the bay window floor and a squashed flex duct feeding the vent in the bay window floor – both issues rectified before closing it up). As suspected, I could see over top the minimal fiberglass insulation all the way to the back wall of the garage (open web truss system). Could see the whole living room subfloor!
Anyway, so now to fix the issue. I would prefer not to have to rip out the garage ceiling drywall, foam (if I can find a contractor to do that small of a foam job – 12’x18′ garage), then re-drywall. I was thinking of cutting out the first bay (trusses run parallel to front wall) of drywall, air sealing the rim, and putting in Roxul ComforBatt (I think I can get R30 in there max). For the remaining bays (although not really bays since the trusses are open), I was going to drill holes in each bay in the ceiling and blow in as much cellulose as I could over the existing batt insulation.
Two questions:
1) I have a flex duct running the length of the garage to the furnace that is in a HVAC closet in the interior. Will blowing in cellulose potentially crush or squash this duct? Should I drill a hole on either side of the duct and blow away from it to at least get as much insulation in there as possible?
2) I am assuming (and will verify when the weather warms up) that the batt insulation installed is kraft faced and was just stapled to the bottom side of the trusses. What do I need to do (if anything) in terms of a vapor barrier? From what I have been able to research, if it is kraft faced, it is on the wrong (cold) side anyway. I don’t want to create a mold issue in the floor system.
3) Any idea if the bay I plan to install Roxul in would need a vapor barrier given the planned thickness? I couldn’t find anything definitive on their website.
You may ask why I am installing Roxul only in the first bay. I figure since I need to open up the ceiling there anyway to air seal the rim, I would put Roxul in while I have the ceiling open. Hopefully that sounds like a good idea….
Any help is appreciated.
Thank you,
Neil
GBA Detail Library
A collection of one thousand construction details organized by climate and house part
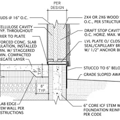
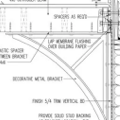
Replies
Neil,
It's going to be tough to do a good job without ripping out everything.
Ideally:
1. Your existing flex duct will be replaced with rigid galvanized ductwork, installed as close to the subfloor as possible.
2. The rim joists on all four sides of your garage will be carefully air sealed with closed-cell spray polyurethane foam.
3. Additional insulation meeting minimum R-value requirements for floor assemblies will be installed under the subfloor and in contact with the subfloor. It's important to get enough R-value under your duct, too.
4. A continuous layer of rigid foam insulation, at least 2 inches thick, should be installed on the underside of the floor joists, followed by new drywall, to address thermal bridging.
5. The new drywall should be installed with attention to airtightness, especially if your ceiling has any electrical boxes or other penetrations.
You can try halfway measures, but they are unlikely to have satisfying results.
For more information, see How to Insulate a Cold Floor.
Martin,
Thank you very much for the quick reply. I have read the "How To Insulate a Cold Floor" and totally agree with everything in there, if I could do it....
A couple of items that I (probably) couldn't do as per that article or per your suggestions are:
1) Rigid HVAC pipe. I doubt (but not verified) that all the holes in the trusses line up to allow a rigid pipe to go the whole length of the garage in a straight line. I presume they are not perfectly lines up so installing rigid pipe may be problematic, possible requiring a lot of fittings for slight angles to get from one truss opening to the next. The HVAC is perpendicular to the trusses.
2) HVAC pipe close to the floor. The closest I could get would be limited by the top member of the truss. I think they are just made of 2x4's, so that might work based on the detail in the article which shows rigid foam board above the duct work. Again though, it would be a lot of small pieces fit between trusses since the duct runs perpendicular to them.
3) R value under duct. I think I can get the required R value for the floor (looks like R25 to R30 required for Zone 4 in floors). The trusses appear to be about 8 inches or so deep. Roxul would meet this requirement if I have a full 8 inches, or using their R-24 batts plus rigid foam as you mention in Item 4 should get me there too. Again, requires full ceiling gut though and reducing ceiling height, which is not generous to begin with (maybe 9 foot height max).
I'll have to evaluate how far I want to take this. Right now, the floor is cold. Getting a contractor out for this small of a job will be next to impossible (it took me 3 years to find a contractor to replace the rotted wood on my bay window I mentioned, most said it was too small a job and they were too busy...).
Another quick question in terms of rim joist sealing. Since I have open web trusses, parallel to the front of my townhouse, how can you seal them? From what I gather with solid joists, you spray foam or rigid foam board/spray foam in between the solid joists. Since mine are open, how would you seal the front truss that runs across the front of the house? It is a bunch of triangular spaces. Foam may be the only way to go I guess. Also, I believe the trusses just rest on the wall between the garage and entry hallway adjacent to the garage. Since they aren't solid, putting a foam board there might not work because of the opening in the trusses themselves. Lots of things for me to figure out....
Thanks again,
Neil
Neil: once you commit to cutting out a single bay of drywall and drilling holes all over the rest of the ceiling, you might as well follow Martin's advice and do it right. Rip off the whole ceiling, properly insulate it and hang the new drywall. It's only a garage ceiling, so it doesn't need to be perfect. I've been screwing around with my house built during the Washington administration for twenty years now and have finally realized that doing it right the first time is a better use of money and time. I'm the worst drywaller in the western hemisphere, but that's what I'd do.
Foam under the floor joists seems to be the preferred solution to deal with thermal bridging in these scenarios. I wonder if a rigid mineral wool could perform well in this location as well? Roxul comfortboard or equivalent?
Neil,
Life is full of compromises, so you should forge ahead with your halfway measures if that's what you want to do. You can buy a two-component spray foam kit to air seal and insulate your rim joist; these kits will perform better than an installation of rigid foam.
Darryl,
Yes, you can install semi-rigid mineral wool panels in a continuous layer under the floor joists above a garage.
The main disadvantage compared to rigid foam is that mineral wool is squishier. To install the drywall, you would need to install 1x4 furring strips under the mineral wool; you'd probably need to adjust the screws on these furring strips up and down until all of the furring strips were co-planar.
Martin,
Certainly not looking to do things halfway, but looking to see if there is more than one way to do things. I guess my original approach was based off of details provided by Joseph Lstiburek in some other postings I have read and that you had commented on and look like this below:
https://www.greenbuildingadvisor.com/sites/default/files/Joe%20L%20insulation%20does%20not%20touch.PNG
Would still have to deal with air sealing around the edge, but that might be simpler than ripping out an entire ceiling. come springtime I'll have a better idea of what the floor assembly looks like since I will be removing my small porch roof which is adjacent to the garage (and also has the living room above). The porch roof is actually siding laid horizontally, so looks pretty easy to remove and poke my head into. I have a feeling I will be looking across the entire subfloor above again....
A full tear out may still be the best and only option.
Thank You,
Neil
Neil, Joe has it right. Insulation does not need to be in contact with the floor above it. Fix the perimeter step one. Step two, add rigid foam to the entire garage ceiling. Step 3, add back a layer of drywall.
Just doing the perimeter well will give you the most results.
If you blew in cellulose without trying to dense pack, you would not damage the ducts. But, I would first rescrew off the existing drywall to make sure the sheets stay I place. This step is a must.
Another option is to add a layer of foam under the carpet in the room above.
Best to have built all right from the start but very few owners pay builders to do more than add some nice granite countertops.
Unfortunately AJ I am not the original owner and this is a typical big builder townhome. Believe me, if I could, I would have a nice (not so huge) single family house built to high energy standards rather than the production McMansions they build nowadays.
2 additional questions come to mind, and I only ask all of these questions because I am trying to learn (not be difficult to anyone, I certainly appreciate everyones expertise):
1) Perimeter sealing. Since I am in an interior townhouse, only 1 out of the 4 walls are exposed to the outside. 1 wall is a shared party wall, 1 is the rear wall with stairway to second level behind it, and the last wall is a shared wall with my entry hallway (except a small portion which is shared to the front porch). Am I correct in that perimeter sealing is still a good idea around all 4 walls to make sure cold air does not enter from the garage, not just the outside? Just trying to figure out that when people reference rim joist sealing, it is generally assumed that they are talking about exterior walls resting on foundations, which is not quite my case since I have 3 interior walls.
2) You mention the rigid foam (which is shown in both Joe's and Martin's details). Can that be added below the existing drywall, then a new drywall layer installed? I am guessing no, but just checking. Also, am I correct in that the rigid foam is more to combat thermal bridging of the joists? Since I don't have solid joists but rather open web truss, are they less susceptible to thermal bridging? That is something that I have also begun to research.
Thank you again Martin and AJ for your input. As I mentioned earlier, I may have a better idea of what is truly going on in the floor system this spring when I look in the porch roof. Depending on what I see, I may have limited options anyway.
Thank You,
Neil
Another quick question as I keep reading up on this more.
The layer of rigid foam (1-1/2" to 2" suggested depending on whose detail you look at) under the joists is mentioned. What I don't see is what type of rigid foam, EPS, XPS, or foil faced iso. Since they each have different levels of permeance, and I believe it is generally accepted that most standard OSB used in subfloors is a vapor retarder, is it important which type of board to use? Would you want less permeance in the board to allow drying to the garage becuase of the OSB above? Just curious.
Thanks,
Neil
Neil,
There are many possible hidden chases in partitions that can create so-called thermal bypasses. For this reason, I strongly urge you to seal the rim joist on all four sides of your garage -- even the sides that face an adjacent unit or interior space.
It doesn't really matter whether you choose to use EPS, XPS, or polyiso to install on the underside of your floor joists. Any of these types of rigid foam will work. However, EPS and polyiso are more environmentally friendly than XPS.
Yes, you can install the new layer of rigid foam on the underside of the existing drywall ceiling if you want, as long as you install a new layer of drywall underneath the foam. Check with your local building department on drywall requirements for garages: in most jurisdictions, you need 5/8" drywall in this location.
The drywall that exists should be 5/8 fire rated drywall so the next layer added could be 1/2".
Get to work. For all of us... may this spring come sooner than later. This year seems like the longest sub 32 weather in years... decades... bring on the global warming.
Alright, so you guys have convinced me to undertake this. Just a couple final (hopefully) clarifications/details:
1. Martin, you stated that the type of foam under the floor joists doesn't matter. I just want to be sure I am not creating a condition for vapor issues (in case I don't seal realllly well around the rim joists although I'll do my best) since if I use foil faced polyiso I understand that is fairly vapor impermeable, as is the OSB subfloor above. Would I create a vapor inhibiting "sandwich" with vapor impermeable materials above and below? I only ask because EPS doesn't seem readily available in my area (except for the little 2'x4' project panels). Most everything is XPS (fairly vapor impermeable as I understand) and foil faced polyiso (nearly completely vapor impermeable as I understand). I guess the key is sealing really well so vapor can't enter the space at all, either through top, bottom, or sides?
2. I have the upper portion of a staircase that cuts into the corner of the garage. From my thermal imaging fun the other week, it is not very warm under the stairs. I am assuming it is not insulated, but just has drywall nailed to the stair stringers. Am I correct that I should rip off the drywall, put up some rigid foam (2" thick?) and re-drywall? And stuff the void between the stairs and rigid foam as best as possible? I may try to spray foam the underside of the stairs (since I am already going to do the rim joists), then do rigid foam board, then drywall.
3. I have also looked at the rear wall of the garage, accessible by a hatch in the wall. This goes under the lower portion of the stairs (the stairs go up about 3/4 of a level, then turn and go the rest of the way to the 2nd level). This just has drywall, then R13 fiberglass batts, then it is open to under the stairs. I would like to air seal/increase insulation in the area since the space under the stairs connects directly to my furnace/water heater closet in the room behind the garage. Any air leakage here also goes straight into the house. Thoughts on doing this and not creating a vapor issue?
4. As I mentioned before, I have a porch adjacent to the garage. I am assuming that the open web trusses goes across the entire width of the townhouse and simply rest on the wall between the porch and garage. Above the porch is the same living room space that is above the garage. Should the truss space between the porch roof and garage be separate and sealed similar to the rim sealing? Basically creating a rim at the wall and sealing on both sides, separating the space above the garage from the porch. Or would I rim seal continuously around the garage and porch, basically treating them as one continuous space?
Thank you again for all the help. It is rare that you can ask questions and get a true expert to provide responses.
Thank You,
Neil
To those with the know-how,
What happens with respect to XPS and polyiso offgassing if you completely encapsulate the XPS in the rim joist with closed cell spray foam? Does the offgassing migrate through the wood rim joist, to which it has been affixed, and then to the environment, or does the stable environment provided by encapsulation prevent the offgassing and thus preserve the insulative capacity of the XPS and polyiso?
I do this for a living... basic guidance I enjoy giving... detailing every exact detail down to minute to minute work details, I would rather you all hire me or another qualified contractor.
Anyway... moisture is not an issue when the sandwich has no moisture drive on either side... to do the work you have to understand the basics then dig in.
AJ,
Sorry if I overstepped any bounds.
-Neil
Neil,
1. Condensation on the foil-faced polyiso is highly unlikely, since there really isn't any scenario by which warm, humid air will come in contact with a cold surface. (In general, rigid foams are safer than polyethylene in this regard, because rigid foams have R-value.)
2. Yes, it makes sense to install an air barrier and insulation under the stairs.
3. In this (and other poorly insulated sections of your thermal envelope), it also makes sense to install an air barrier and insulation. Stop worrying about vapor diffusion; what you need to do is stop air movement, and make sure that you have a good insulation layer in contact with your air barrier. For more information, see Forget Vapor Diffusion — Stop the Air Leaks!
4. If floor joists penetrate your thermal envelope, then you need to install airtight blocking in each joist bay at the plane of the wall where the joists penetrate your thermal envelope. The usual blocking chosen for this purpose is rigid foam. Each rectangle of rigid foam should be sealed at its perimeter with canned spray foam or high quality tape.