Cold in Canada

Hi all, came across this site a few days ago and haven’t stopped reading.
I think I “over did it”, too much info. 🥴
Now to my question… after you learn about my home.
Edit: north of Toronto
Zone 5b
1970’s house single pane windows
2×4 stud wall
Basement not insulated, but has paneling on walls
First floor drywall
2nd floor paneling
To my surprise r-10 Kraft faced fiberglass insulation and 4 mill vapor barrier behind walls and ceiling.
**Not sure what I have for sheathing, I haven’t removed any poly or insulation..I think it’s going to be that black tar impregnated board.
Wood siding
Asphalt shingles-**hoping to install metal roofing
Forced gas furnace.., adding A/c soon.
I have new double pane and triple pane windows (most- casement some sliders, some all aluminum, some vinyl) that I will be installing
I would like to add exterior insulation and new siding
*I feel confident in my window and siding installation (flashing, rain screen, backer rod and caulk)
so here are my question (s)
1. If I install my new drywall as an AIR BARRIER, do I need to remove the Kraft paper from the current existing insulation.
2. Do I reinstall the existing 4 mil poly.
**code is 6 mil**
2a. Do I replace walls and ceiling with 6 mil or Certainteed MemBrain?
Edit: after sleeping on this, I don’t think I can put a vapor barrier can I.? (How will the drywall seal to the framing. )
Edit: I need to use a “paint on” vapor barrier…. right?
3. When I complete the exterior insulation (not 100% sure with what-eps,xps,rockwool) (probably 3″ of eps) / siding WITH a sealed wrb, will it be ok having (2) both the inside air barrier AND the exterior.
And lastly, would it make sense to take the existing r-10 fiberglass
and move it to the attic
(Do I leave the Kraft paper on?) And replace the walls with Rockwool.
(If your recommendation is to remove Kraft paper for question 1, than this for sure makes sense. )
Attic currently has r-10, Kraft faced towards the heated space. This would get me closer to a code compliant attic,
then top it off later.
Thanks everyone!!
… ok back to bed.. … .
GBA Detail Library
A collection of one thousand construction details organized by climate and house part
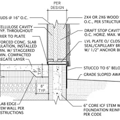
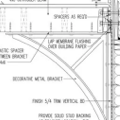
Replies
There's a lot to unpack there, but I'll try to start.
First, you should understand the difference between air barriers, vapor barriers and water resistant barriers. They each do different things, as their names imply. All are required parts of a wall assembly. Certain materials can perform more than one of these functions. The locations of these "barriers" is also important, and sometimes changes a bit depending on the wall design.
Bulk water tends to work from the outside in, because the bulk water that we usually care most about is from rain. We want to stop that before it gets inside the wall, so we put the WRB as close to the exterior as possible. We usually cover it with cladding (siding) to protect it from the weather, and also to make the houses look better.
Water vapor generally moves from warm to cold. In zone 5a, it's colder outside than inside for more of the year, so we try to put the vapor "barrier" closer to the inside. This one is more complicated, because even in your area, air conditioning is convenient in summer and when the A/C is on the inside is cooler than the outside and the vapor drive reverses. So, it might be better to have the vapor barrier closer to the middle of the wall. Certain wall designs do this. It might also be better to not have a vapor "barrier," but instead a vapor "retarder," and in fact, "Vapor Retarder" is currently the preferred description for this layer. We see this in the different classes of vapor retarders discussed in the codes and the literature, from Class I (basically, a barrier), to Class III (relatively vapor-open). Membrain is a synthetic "smart" vapor retarder that changes its vapor permeance based on conditions. If the wall is wet, it becomes more vapor-open so that things can dry out. When the wall is dry, it is relatively vapor-tight so that moisture does not move through it to places where condensation might occur.
Finally, we have the air barrier. It doesn't matter much where in the wall the air barrier is located, and multiple air barriers are just fine. We want to stop air movement through any part of our building envelope.
So where does this bring us with regards to your questions?
1. You do not need to remove the kraft paper from the insulation. Asphalt-saturated kraft paper is already a somewhat "smart" vapor retarder, and the way it is typically installed it is only somewhat effective anyhow. If you seal the drywall to top and bottom plates, seal the plates themselves, and seal all of your outlets and penetrations, you can make the drywall a reasonably effective interior air barrier.
2. Remove the 4 mil poly, and don't install any new poly. We generally recommend against Class I air barriers, except in really cold (Zone 8) climates.
3. If you install a sealed WRB on top of your sheathing and behind 2"-3" of insulation, you've got your primary air barrier, water barrier, and vapor retarder right in the middle of your thermal envelope, and that's a good thing. The asphalt-saturated fiber sheathing is also a somewhat "smart" vapor retarder. With R15 or so insulation on the outside of the wall, and R-10 or so inside, the temperature of the sheathing will rarely approach the dewpoint of the interior air and will generally stay dry. If you do get some condensation during extreme weather events, your walls can dry to both the inside and the outside. All is well.
For extra protection, you could install a vapor-retarder latex paint to the interiors, but it's probably not necessary.
>"Edit: north of Toronto
Zone 5b"
Toronto is on the cold edge of zone 5A, pretty close to the warm edge of zone 6A.
>"To my surprise r-10 Kraft faced fiberglass insulation and 4 mill vapor barrier behind walls and ceiling. "
If it between the gyprock and insulation + studs layer on the above grade walls it's fine to leave it in place. But for a studwall in the basement that would creates a moisture trap, keeping the studs & insulation susceptible to ground moisture.
>"Edit: I need to use a “paint on” vapor barrier…. right?"
Air tightness is far more important than tightness to vapor diffusion. In many ways it's easier to detail broad-sheet plastic such as MemBrain or polyethylene as an air barrier than gypsum board. An even more robust primary air barrier would be to detail the structural sheathing as an air barrier, which is easy to do if plywood, hard to do without spray foam if plank. A fully-adhered vapor permeable WRB on the exterior (eg BlueSkin VP100, VYCOR enV-S) will go a long way toward tightening up any type of sheathing.
With 3" of EPS (R12+) of exterior foam the IRC would allow using plain old standard interior latex paint on gypsum board as the interior vapor retarder for a 2x4 wall in ANY climate with huge margin for a zone 5A/6A climate, no need for vapor barrier paints:
https://up.codes/viewer/connecticut/irc-2015/chapter/7/wall-covering#R702.7.1
>"3. When I complete the exterior insulation (not 100% sure with what-eps,xps,rockwool) (probably 3″ of eps)".
XPS is an environmental disaster due to the extreme CO2e footprint of the HFC-soup blowing agents used for all XPS in North America. All HFCs are powerful greenhouse gases- the largest component used in XPS is HFC134a, which clocks in at about 1400x CO2 @ 100 years. As the HFCs diffuse out over the decades it's performance drops to that of EPS of similar density. The fine print of the warranty for XPS is only good for 90% of the labeled R @ 20 years.
EPS is blown with variants pentane (~7x CO2 @100 years), most of which escapes the foam at the factory where it is recaptured, not vented to the atmosphere. The performance of EPS is stable for many decades.
Deleted