CMU Ranch Renovation

I am working on the design/budget phase of renovating a 2100 SQ FT ranch, in the Baltimore area (zone 5?). The original construction is CMU walls with stucco on the exterior. Wood framed floor over unconditioned crawls space (joists in CMU pockets and completely rotted out!) and stick framed roof bearing on the CMU walls.
My intention is to remove the entire wood floor system. New floor system will be 3″ slab over 10 mil poly, over R10 foam insulation, over 5″ compacted gravel with drain tile. CMU walls will remain and be insulated from the exterior. I plan to frame a 2×6 wall with 4″ air gap in front of the CMU (12″ above grade), then zip sheath, WRB, rain screen and clad the framed wall. Rigid insulation and parging will start below the framed wall and continue into the ground. Framed wall, outside of CMU to be insulated with dense pack cellulose to R-40. Roof system will be I-Joists bearing on CMU and cut flush with exterior 2×6 framed wall and zip sheathed as well, continuous sheathing plane around the entire wall and roof system and insulated with cellulose to R-60. Sleepers, additional roof sheathing, metal roof and overhangs built on top of zip sheathed walls/roof with 1.5″ air gap.
So basically I am trying bring the CMU walls inside of the insulation envelope. They remain, along with original footers, that they sit on, for structural use only. My main question, among many, is where the air barrier should be, so that it is as continuous as possible. I am leaning towards the air barrier being inside of the insulation envelop and the CMU walls. I could use the 10 mil poly under the new slab and bring it up the CMU walls then………. I would need to continue the air barrier up the walls and along the ceiling plane under the rafters with continuous 5/8 sheetrock. But what material should I use on the CMU walls for the air barrier? Or should my air barrier remain at the exterior along the sheathing plane? My only hesitation with that is it would be hard to integrate the air barrier into slab with the existing CMU walls and foundation in place. The air barrier would just run into the ground. Is this a problem? Any ideas or issues with the general plan otherwise?
GBA Detail Library
A collection of one thousand construction details organized by climate and house part
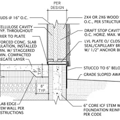
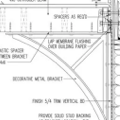
Replies
Charles,
You are probably overthinking this.
Concrete is an air barrier, so your new slab will be your air barrier at your floor. I presume that the CMU walls will be finished on the interior with plaster or drywall; if you pay attention to sealing any wall penetrations, the plaster or drywall can be your wall air barrier. You are already planning for your drywall ceiling to be your ceiling air barrier.
All you have to do is seal the gap between the slab and the bottom of the drywall on your wall with caulk or a gasket.
Martin,
Thank you very much for the feedback. Maybe I am over-thinking more than just the air barrier.....
For budget reasons I would love to have my insulation inside of the CMU wall as well. With a 10 1/2" framed wall cavity on top of the slab, insulated with cellulose. Then I could put a WRB outside of the existing stucco, rainscreen and clad. This would all save me a fair amount of time and material.
Could this assembly work as well?
Charles,
Yes, you could probably come up with details for interior insulation. The down side is the loss of interior space.
FWIW: Baltimore is the cool edge of zone 4, not zone 5.
There's no real advantage (and some disadvantage) to adding even more insulation on the interior side of the CMU. CMU has a substantial thermal mass, which moderates the temperature fluctations from solar gains through windows. This is beneficial for reducing both the peak and average heating & cooling loads. With R40 on the exterior, or even R20, isolating the thermal mass from the interior with even R5 would very likely INCREASE your annual energy use rather than decrease it, in a zone 4 location. (Model it with DOE2 or BEOpt, if you like.)
This is a primary criticism of the insulated concrete form approach when vendors begin gushing a bit too much about the thermal mass benefit. The mass benefit while still real, is largely wasted- a fraction of what it COULD be due to the interior side insulation. With an R40 nominal exterior you have sufficient R to take great advantage of the thermal mass of the CMU, unless you shoot yourself in the foot by isolating that mass from the conditioned space.
In a zone 4 climate putting 3-4" of rigid roofing polyiso (R18-R24) on the exterior of a CMU wall under the new siding would give it near-superinsulation performance due to the thermal mass advantage. Then concentrate on all of the thermal bridging points- it may be worth digging down and putting an equal thickness of rigid rock wool or EPS on the exterior to reduce the thermal bridging to the exterior, as well as 2" of EPS down to the footing between your new interior slab and the CMU.
Dana,
Thanks so much for the feedback.
So you are proposing 3-4" of polyiso on the exterior from grade level up walls and over roof (eliminate original overhangs, etc...) continuous and 2" EPS below grade to the footer elevation?
Wall assembly from exterior to interior: cladding, rain screen, WRB, (2) layers of 2" polyiso staggered and seams taped, CMU wall, interior framed wall (uninsulated), sheetrock, paint.
This would be more budget friendly than my original proposal. Not excited about attaching furring strip to CMU through 4" of foam but there is probably a long enough masonry screw out there
That stackup works fine- you might want to match thicknesses on the EPS with the polyiso a little better to avoid the 2" step back at that level.
Standard 1/4" TapCon hex heads come in lengths as long as 6" (p/n ) which should be fine for 4" foam, giving you 1.25" of penetration into the CMU if using 1x furring for establishing the rainscreen, and with 3" foam you'd have over 2" of penetration. If that feels too sketchy, put them 16" o.c. instead of 24" or go to a fatter screw. At 7-inches & longer the diameters start at 3/16", but they're available.