Closed cell foam in in vented roof

I have been able to avoid using spray foam up until now but with recent code changes in our area we are now forced to use it.
On a current job we are framing a new roof directly on top of the existing old roof sheathing because the owner wants to expose the hand hew beams of the original frame below. The new rafters are 2×8 and the plan is to spray the bays with closed cell foam on a warm day and then immediately sheath and roof.
I’m a concerned because the rafters will have no time to dry out before being foamed and I’m concerned about lumber shrinkage
I have been in the attic of several 3-5-year-old homes in our area that were sprayed with closed cell foam and I often see a 1/8” +/- gaps between the rafter and the edge of the foam. I’m assuming this is because the rafter has shrunk as it dried out over the years and would think that this gap will be a cold spot in the winter where condensation and eventually rot will form?
My concern is on this job that the gap will be even worse because we will be spraying up against the 2x8s that have not had any time out of the weather and they will also shrink as they dry?
Should I be concerned? Is there some way to prevent this?
Thanks.
Jud. Norwalk CT
GBA Detail Library
A collection of one thousand construction details organized by climate and house part
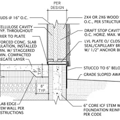
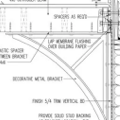
Replies
I meant to title it as "Closed cell foam in unvented roof"
Judson,
Are you available to talk about a high efficiency project in Redding?
Thanks
Andrea
I think a good option would to use taped and sealed rigid foam with staggered seams over the existing roof decking and then a new roof system. You could buy recycled polyiso to make it more affordable.
+1 for rigid foam above the roof deck. This is commonly done on commercial roofs, works well, and has no thermal bridges, which is an added bonus. Rigid foam can be applied under a wider range of conditions than spray foam, and your framing can still dry inwards if you use exterior insulation. I also recommend polyiso here, and you'd probably need at least 6" to meet code (but it depends what is code minimum in your area, and remember that with continuous insulation, you can go with U factor for the assembly which will mean a lower R value of insulation is needed compared to what would be required if you just insulated between rafters).
Excessive moisture content in the surface you're spraying against can be a problem with spray foam, although I have not seen serious problems myself. You can use a moisture meter to test though, and not apply spray foam if the moisture content exceeds the manufacturer's recomendations for application of their spray foam material. Trying to apply spray foam when things are too cold is also a problem, with 50F usually being the low limit (although this can vary a bit with different materials). My guess is the weather in your area is probably cold enough now that the temperature is also adding extra risk if you use spray foam.
Bill