Climate Zone 6 – Wall Assembly

Hi there,
We are building a 2 storey, 3000sq ft home in Toronto, with generous overhangs around the building.
The masonry veneer-clad wall assembly consists of 1” GPS R5 foam overtop Siga Majvest wrap over top ½” plywood sheathing. The exterior walls will be framed with 2×6 LSLs 24” OC and the cavity sprayed with 3.5 inches of CC spray foam. I know there are varying opinions on using spray at all, and how much to use for cost. In this case, we have an experienced family friend doing it for us, giving us a break on price.
My questions are:
1. Is using 1” of foam even worth it? I wanted to provide a thermal break for the studs. My concern about using thicker exterior insulation is increasing the overall thickness of the wall assembly on my 10” thick foundation. I don’t want to compromise the airgap for the brick veneer. I have read the article about how much exterior foam is needed for a given climate. However, I was wondering if the need for thicker exterior foam still applied with having so much CC spray foam? Will drying to the interior still occur?
2. Will the performance of a higher perm WRB (55 perms) like Majvest be impacted if covered with a low perm (0.5 perms) foam? Will it ‘suffocate’ the house wrap and prevent it from drying? Will it provide an adequate drainage plane for water that gets behind the foam?
3. What are peoples experiences with with 24” OC framing? With LSL studs? Are there other items to take into account for planning the framing going this route? Thicker plywood required? I am planning on 1/2”.
Using LSL studs should provide us with straight walls, and reassures me against the ‘wavy drywall’ concern. And our cladding – masonry veneer- is not ‘hanging’ off the sheathing to worry about wavy siding. However, feedback with real world experience would be appreciated.
Thank you in advance
GBA Detail Library
A collection of one thousand construction details organized by climate and house part
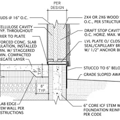
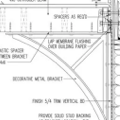
Replies
I'd adhere to your own code and the code here:
https://www.continuousinsulation.org/content/2021-ibc-and-irc-adopt-improved-vapor-retarder-requirements
Unfaced 1” GPS R5 should be more like 3 perms - which is reasonable drying to the exterior.
Thank you Jon for the input.
Here is the technical info for the foam I was looking at:
https://www.plastifab.com/products/durospan-gps-insulation/durospan-gps-r5.html
Should I look for something else with more permeability ?
reddoorbuild,
1. Yes I think the foam is worth it - especially in Toronto where contractors have experience with it.
2. Unless the cost difference was fairly inconsequential, I'd use a standard WRB like Tyvek.
3. 24" oc stud spacing is fine. There is nothing to worry about or adjust. 1/2" plywood is also fine.
Thank you Malcolm for the response.
1. There has been talk of a minimum thickness of foam depending on climate zone - as well as cautions against combining exterior foam with spray foams since it would prevent the wall from drying to the interior. What are your thoughts? According to this article the minimum foam thickness for my climate zone and wall assembly is R11.25.
2. Is this because the foam will take the ‘brunt’ of the bulk water that gets through the masonry veneer wall, and therefore the WRB doesn’t have to be ‘high performance’?
Thank you
redoorbuild,
1. The call to use thicker exterior foam is to keep the sheathing warm enough so it doesn't accumulate moisture, but in your stack-up the closed cell spray foam will stop moisture from getting to the sheathing so you won't have the problem. What are you planning on doing with the remaining 2" on the interior of each stud bay?
2. You shouldn't experience any bulk water getting into the wall. Any incidental leaks should drain down the back of the masonry and exit through the weep holes. The foam and any WRB is adequate to keep the all safe in that respect. More important is dealing with inward vapour-drive from the reservoir cladding, and again the combination of the foam and WRB will insure the wall doesn't take on the moisture. I understand the desirability of using a variable-perm membrane on the interior of walls over poly in many circumstances, but remain unconvinced there is much difference between the commonly used WRBs in most situations. My own preference would be Tyvek Commercial, or as Jon suggested Drainwrap.
Thanks again for your info.
1. Good to know that thin exterior foam plus thicker cc foam inside is a viable/safe combination for my climate zone.
To be honest, I have no current plans for the 2” space. I had considered adding in batts on top but the walls on main floor are 10’ and second floor are 9’, with the 24” OC, means there would be more labour since the typical fiberglass batts I have seen are either far too thick, or too narrow. Do you think that the cost and labour associated with it are worth it for? Do you have other suggestions for that space?
2. My thought of using the Siga product was overtop the plywood and under the foam. However, I would rather go with a wall assembly that has been field tested, and if Tyvek Commercial/DrainWrap under ext foam has been then I will go with that.
reddoorbuild,
I was more curious - I agree there isn't much point monkeying with those uneven voids in the stud bays.
The most common wall assembly in your area is now probably 2"x6" with fiberglass batt insulation, 1" exterior foam and a sheet WRB (Tyvek or equivalent). The wall breaks the rules around sufficient exterior insulation, but appears not to experience any moisture problems in large part due to the well sealed interior poly air/vapour barrier.
The advantages of going with that are:
- Familiarity of the trades.
- A proven track record.
- Cost.
Being fairly conservative, my rule of thumb for deviating from what is usually done is that it should yield an appreciable improvement. I'm not saying your proposed assembly won't work, or has any disadvantages, but I'm not sure it will be easier to build, or provides anything the more common one doesn't.
> poly, 2"x6" with fiberglass batt insulation, 1" exterior foam ... breaks the rules
Note that such a wall is OK per the 2021 IRC. And buried in the footnote is a restriction if the foam is a Class I vapor barrier (so avoid foil faced foam in such a design). With R5 foam and Z4-6, it's also OK with a smart Class II on the interior. Unfortunately there aren't smart Class I barriers - they would be useful in Z6-7.
+1 on considering more common designs. Like no CC spray foam and more exterior foam to get the same whole-wall R value.
I'd use > 2 perm exterior foam to maintain a better perm ratio and allow reasonable outward drying of the sheathing. And DrainWrap (or similar) WRB as cheap insurance if water ever made it that far.
Not sure that I'd trust spray foam as the only air barrier. Even if other gaps are caulked.
Thank you, I reached out to a local Tyvek supplier a while back and they were backordered on DrainWrap. I will look into it again.
Even with 24OC framing you still get a fair bit of thermal bridging through the studs. This means that even though you are putting in about R20 of SPF you are really only getting around an R15 assembly.
Switching to 5.5" open cell foam would use about 1/3 the polymer for a much lower environmental footprint plus give you a slightly higher assembly R value.
LSL are worth it for tall walls but could be harder to source. I would get the engineer to spec both LSL and 2x on the drawings in case there is a shortage.
I'm with Malcon on the WRB, I don't see the benefit of any high performance housewraps here. There is no benefit for the overall assembly, standard housewrap is good enough. Jon R's suggestion of permeable foam is the way to go, spec unfaced EPS/GPS or permeable polyiso.
Continuous insulation does make a big difference on the overall assembly R value, at the current lumber costs it also doesn't add that much to the overall cost, well worth the money.
Spray foam will also not do a great job of sealing around any double studs, complicated framing or floor wall transitions. For an air tight assembly the best is to tape the sheathing on the outside.