Climate Specific Affordable Comfort

I think “we” could come up with some generic “recipes”
for Not-So-Costly and Not-So-Brown homes.
I would like to start with Hot/Mixed Humid
(a neglected Climate)
I will try to present a current recipe for “affordable low energy” in Dallas,Texas.
A typical Habitat for Humanity type of house.
And then “Study Group” Alternate Recipe suggestions
GBA Detail Library
A collection of one thousand construction details organized by climate and house part
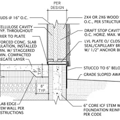
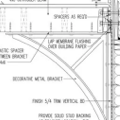
Replies
This is roughly what I remember from a HFH site visit about a year ago.
Energy Star Rated
all electric
3 bedroom 2 bathroom one story plus 1 car garage
narrow street frontage (zero lot line) with alleys
guessing 1200 sf
Slab on Grade Foundation
Simple floor plan 9 ft ceilings
Gables & trusses
Fiber Cement Siding
maybe 15% glazing/floor area
windows=vinyl frame LowE 0.35 SHGC
U value = 0.35
2x6@24oc walls built offsite by volunteers
fully sheathed in OSB
fully covered with 3/4"(I think) XPS(donated)
I can not remember if they used housewrap
stud cavites and underside of roof deck = Open Cell Foam(at retail cost)
Air Source Heat pump with fresh air controller
Air handler on ground floor in a closet
Ducts in the attic
water heater in the garage
Oh yeah and stylish BLACK roof! WTF
here is an aerial view
I don't have any streetview photos yet
I will be back with more details later
Hey, you gotta go with what's donated, and the building supply house was probably not selling many black shingles on the open market.
John I think the "less foam approach" you've been playing with is a good start. I liked what Jon Wyman was doing with using flat trusses as rafters over a cathedral ceiling. And I really like the double stud wall approach. so...
8" block foundation on paint-on asphalt capillary break with 2" foam on interior and fully insulated floating slab.
Double stud walls, dbl ply upper top plate, blown full of Spider or Cellulose, fully sheathed w/ ply for hurricane resistance, Vertical fiber cement or wood siding, horizontal Fiber Cement, or cedar shingle siding. (horizontal wood siding grows mold too much for me in the south)
18" open web truss ceilings with OSB attic floor deck and over-framed, vented attic, Light asphalt shingle solar angle roof (better than steel for hurricane repair) Alternate flat roof with second floor deer-free growing area and third floor solar racks behind parapet. Foil OSB on porch roof only, high venting of porch ceiling volumes.
HVAC unit in closet ducted in trusses using App State duct design. (curved fin registers on ceilings as close to air handler as possible, one return in Master Suite, one as close to air handler as possible) all focused on minimizing developed duct length.
Galvanized termite flashings, advanced low-toxic pest management, Rain gardens at all gutter outlets, water conserving fixtures, Calculated flow branch and twig plumbing w/ demand recirculation.
Drain-back solar hot water, w/ spot radiant heat in a few areas only w/ tile or brick pavers over and resilient Marmoleum or wood flooring elsewhere.
The building section here was drawn by Colyer Durovich a teenage intern from a local Waldorf school his first scale drawing ever.
I will try and contact Habitat this week and get more details.
When I went to the open house last year ... I asked about the shingle color.
The shingles were NOT donated ... this was the choice of management based on homeowner survey.
Dark Brown, Dark Grey and BLACK shingles are the fashion rage here!!!
They don't show the dirt from polluted air as much as light colored shingles (and they show up better in aerial photographs).
What is the advantage with all electric?
Where I live (Ontario rates/very cold climate) this would be gifting the occupants an outrageous heating bill.
What about ductless mini-splits?
This must be a hot/mixed humid thing?
I am working with a Habitat Chapter that is building a Passive House prototype, don't sell them short.
Until recently, and probably still in most parts of the country, HFH has been concerned with building houses that are very affordable to buy but not necessarily affordable to operate. They often use the least expensive mechanical systems (and other materials as well).
Fortunately, local HFH affiliates are given wide latitude to create locally-appropriate housing and a few have begun to focus on operating affordability.
In the early 90s, a HFH affiliate in W. MA built what I believe was Habitat's first superinsulated house in Northampton. I built the second on Greenfield MA, initially for a local community land trust and housing coop - both of which suffered from a market collapse and reneged on the agreement to purchase, so we sold it to Habitat.
The Green Mountain HFH chapter just built a house in Charlotte VT, ostensibly to Passive House standards, though the administrators of that chapter keep referring to it as a Passive Solar House and don't seem to understand the difference.
I certainly respect H for H
The homes they are building here in Dallas are superior in many ways to many of the "custom built" homes.
The Black roof was a little shocking to me ...
but heck...almost all of the custom homes down here have dark roofs too.
I will try to get more facts and details this week.
Funny thing is that it was HFH houses in Miami-Dade County that survived Hurricane Andrew better than many tract homes because the volunteers actually nailed the roofing shingles by hand rather than pneumatically stapling them, and the roof sheathing was attached with full-head nails rather than the clipped-head pneumatic nails that most builders used.
So the codes were changed to force all the builders to build like HFH. Go figure.
Well, at least H for H homes are a far cry from monstrosities like these:
http://ca.video.yahoo.com/watch/2375925/7419516
5(!) fireplaces
6500(!) sq ft.
It might take every penny the recipient family has just to keep the lights on!
Sorry John, not really what you're looking for.
Lucas,
I was going to get back to your questions and got sidetracked.
Robert answered the question about why electric... less upfront cost
At least the homes are reasonably tight and insulated so the heating bill is not too awful.
Gas heat would cost less to operate.
Down here the water heaters are almost always in the garage or the attic.
The builders do not want to give up air conditioned space to mechanical equipment.
Ductless minisplits are not fashionable even for low income housing.
kinda like the light colored roof thing
and the 6500sf 5 fireplace
would barely qualify as a starter McMansion down here
John, it seems like your biggest problem is that creative freedom is being hamstrung by "de rigeur". It really seems a shame that you cannot entertain the idea of ductless mini-splits.
Central a/c doesn't seem to be that widely used on the Hawaiian islands... Maybe energy just has to get more expensive first.
lucas,
a/c isn't needed when you've got properly sited buildings, trade winds, deep overhangs, large operable windows/doors and 'aloha attire'.
John Brooks,
The problem I see with white-colored asphalt shingle roofs here in Vermont is the problem with roof algae -- a problem that seems to be getting worse, because shingle manufacturers are using more mineral fillers and less asphalt, and (perhaps) because of global warming.
Do you have the same problem in Texas? Here in Vermont, a white shingle roof looks like a zebra in about 5 or 6 years, due to the algae streaks.
And yes, I know that it's possible to address the problem with a galvanized steel ridge cap. That's a good idea, but nobody seems to be doing it.
In the late 60's light colored roofs were very common here (Dallas)
The upscale roofs were wood shingle and most others were white composition shingle.
There are still some homeowners that continue to use white shingles.
I don't remember the staining to be a problem here.
Air conditioning is the bear here.
H for H houses with the not-so-high r-value open cell at the roof deck would use less electricity on an anual basis with a light colored roof.
I remember a pretty good improvement in the HERS index for my house when the light colored roof was factored in.
I am not going to get hung up an the roof color because I think the real solution for my mixed climate is to use better than code r-value instead of less than code r-value.
With enough insulation at the ceiling plane the roof color will barely matter.
Lucas,
Personally... I would not have a problem with the aesthetics of ductless mini-split.
It would be too costly to put one in every room.
I think one or two centrally located mini-splits would have to be coordinated with a well engineered ventilation strategy in order to mix the air and provide comfort in all the rooms.
Could you please explain a ductless mini-split? Thanks
Roy,
To learn more about ductless minisplits, see Heating a Tight, Well Insulated House.
I have mentioned "ducted" mini-split at least once before.
Something like this may be a good solution in the near term.
The photo I am posting is of a Daikin
This will give you an idea of how COMPACT the air handler can be.
I do not agree with the(plenum & octopus ductwork) installation in the photo.
The air handler combined with rigid ducting could have been installed in a dropped ceiling of around 12 inches
I believe that The unit is serviced from the bottom
Except in the durability of the roofing. All things being equal, dark composite shingles have a shorter lifespan than light shingles. The more R-value below the roof deck, the more heat is retained in the roofing and the shorter the shingle life.
It was for that reason that almost all shingle manufacturers used to NOT honor their warranty when the roofing was applied on a hot roof.
Dark exterior. Right now (29 degrees outside) much of my own home's exterior is warmer (80-110 degrees) than the inside via the sun. Energywise, I heat and don't use or need AC. Seems like the dark colors are lowering my primary energy costs while the sun is shining.
As to shingle life. The shingles are 23 years old and are likely to last many more years as they are not curling or losing granules or moss covered. They are black and are on a vented roof.
Zone 6. I like all the solar gain I can get.
Any thoughts on dark exteriors being a positive?
perhaps on a new thread
John, could such a dropped ceiling be under a "hat" style roof or maybe between stories under the floor framing?
to post 25
yes, Lucas this exactly what have been considering.
It could also exist between floors "within" the floor framing.
if open web trusses were used
the hallway area could be framed a little differently and the unit
could be above a hallway or laundry room.
John, I remember you once described a way to move the plane of the ceiling air barrier from the under side of the ceiling joists to the top of the ceiling joists.
If I am remembering correctly, I think you were trying to create an "air barrier surface" that could be easily tied to an "air barrier box" that would contain the HVAC equipment in the attic.
I was thinking that an "air barrier surface" under the ceiling joists (ie ADA "goo as you go") could be more easily tied to an "air barrier box" that was part of an insulated drop ceiling under a "hat" style roof.
I don't imagine it would be easy to run rigid duct-work through an insulated drop-ceiling.
I imagine the duct work would have to leave the "air barrier box" downward into a wall chase of some kind.
That sounds easier than my idea.
In a one story house or on the second floor of a 2 story house.
I would install the COMPLETE lid of airtight drywall and THEN
lower the ceiling in a hallway, closets or soffit for the unit and the ducting.
I still think my idea for an airtight Attic Floor (topside of joists) would work
It would not be the most affordable though
The concept is not new (thin profile mechanical below the drywall)
A production builder in Texas was doing this in the 70's
the equipment was not very sophisticated
they located it above the shower with a dropdown servicing panel
the condensate overflow would drip into the shower
a very rude surprize to get hit with that icy cold water
John, re: "the Mooney wall"
I am not-so-familiar with zone 3A.
Is double wall/truss wall excessive?
Would you do a 2x6 "Mooney wall"?
Edit: reformatted for clarity.
Lucas,
Builder's Guide
data for Dallas, Texas
2407 HDD 2603 CDD
winter design temp 22F
summer dry bulb 100F wet bulb 75F
average ground temp 66F
precip 33.7 inches
for a 1 story affordable house it may turn out that 2x4 or 2x6 wall with cross hatch and ADA
could perform better than HERS 50 if other good design strategies are used.
I am basing this guess on my existing home
John, I have thought about the "Mooney wall" in the past.
One problem could be it doesn't seem to provide any easy-outs for a no-foam thermal break at the rim-joist.
I wonder if a cross-hatched ballon frame would be better?
Is it even possible to get 2x lumber in 20' lengths any more?
If the joists are fastened with hangars to a let-in ledger there is room to insulate to the outside of the ledger. I think goo-as-you-go could work with the cross-hatch and ledger. I will try to post a doodle later to better show what I mean.
John, nevermind.
Turns out my idea was less-than-half-baked.
Lucas,
I'm curious about your cross-hatched balloon frame question. (balloon frame Mooney wall?)
What 's the reason that you abandoned this thought?
20' SPF 2x framing lumber is readily available here in MD. You should hand pick your boards at the lumber yard though.
Roy, I think there might be some potential there still.
Last night I had a headache and couldn't quite push the idea to half-baked status.
Today I got a .pdf package from my architect and have been pouring over my own details looking for oopses ;-)
There's always tomorrow.
I like balloon frames - they're cool in the same way an old tractor is cool. I think that's one reason I've always liked Robert's truss system... It sort of reminds me of a super-thick balloon frame.
I think the best way to get a no-foam thermal break at the rim joist is with a truss frame.
Or one of my varieties of double-wall frame that uses the inner wall to support the floor assemblies and the outer wall to support the roof.
John - I have been working on a concept similar to your airseal top of ceiling joist and keeping the mechanicals and duct below the ceiling. Have been trying to come up with a compromise of HVAC in the attic but not doing an unvented attic or conditioned attic and avoiding spray foam. We discussed this a bit long ago but did not have my ductwork inside the thermal envelope.
Working on a two story house with two HVAC systems. Not enough room to put the HVAC in a closet and client and architect do not want dropped ceilings or soffits. Thinking of building an insulated HVAC penthouse in the attic. Building an inverted soffit up in the attic to house the main plenum. Each branch of the plenum can be rundown inbetween the ceiling joists and can air seal the top of the ceiling joist cavity with rigid foam. On top of all of this more than likely will be blown in cellulose. Still working on some of the details as to the rigid foam/blown in transitions. Anyone ever done something like this?
Robert,
I really like the version of the double wall posted above.
But I wonder... will some of the weight from the trusses transfer to the inner wall? And 12 inches of cellulose in a two story wall seems prone to settling. Any concerns there?
Also would this wall work in a heavy seismic zone? Or do the floor joist need to tie into the exterior wall with the CDX sheathing for shear?
There are a lot of good suggestions coming in.
I would Like to see others start threads for other specific Climates
I hope to keep this one focused on my climate
I have emailed the local "H for H" chapter trying to get more details about current practice
so far they have not returned any info.
I will post a typical floor plan and wall section soon.
An Affordable house in Dallas will be a Small One Story House on a Slab on Grade
So I don't think the Rim Joist is an issue for my climate.