Wall Assembly for Cold, Wet Climate

I have a mid-90s ranch with the normal OSB sheathing over 2×4 fiberglass batt insulated construction. I’ll be doing renovations since we need new siding and windows, so I’m going to insulate and attempt to reach as close to PH standards as possible since we spend a ton on propane with average temps in the -30s for months in winter. I live in far Northern WI climate zone 7, very wet and cold in winter, wet and 80s in the summer with little direct sun.
The two redesigns I’ve narrowed it down to after all the research I can find (been planning this for about 18 months) are the following from the outside in:
#1 siding, rain screen gap, R-Guard, plywood, 2×4 structural wall with mineral wool, 3.5″ gap insulated (haven’t decided dense packed or mineral wool yet), intelligent vapor barrier, 2×4 non-structural with mineral wool, shiplap
#2 siding, rain screen gap, R-Guard, original OSB, 2×4 structural wall with mineral wool, intelligent vapor barrier, 2×4 non-structural with mineral wool, shiplap
Obviously #2 has less insulation, which is not desired. I’m trying to keep condensation down. I’d rather not do exterior rigid foam if I can.
Is plywood good for #1? If #1 won’t work then would OSB be ok with only 7″ of insulation behind it or will that cause condensation problems just like 10.5″ would?
This is a house we’ll be staying in for decades and raising a family in, so I’m willing to put in the effort and money to do this right the first time. Sadly bulldozing and rebuilding is not an option, so I’m making the best of what I have. Our other goal is to go off grid and be completely self-sufficient, hence why heat loss has to be an absolute minimum.
Thanks for all the help!
GBA Detail Library
A collection of one thousand construction details organized by climate and house part
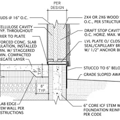
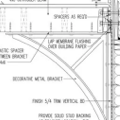
Replies
There are two big advantages to using exterior insulation. One is that it is (nearly) continuous. Any retrofit interior options get very fussy at penetrations, intersecting walls, utility chases, and all of the other complexity on the inside of the house. You can reach high performance goals from the inside, but it is far more difficult. Second is that it does not require complete gutting of the interior. Once you gut the interior and exterior of the house, you will be approaching the cost of a rebuild, unless you are doing most of the work yourself. Even if you are doing it yourself, there is a cost to that, associated with the cost to you of doing something else for either money or pleasure with the same time. OK, three advantages. The third is that it keeps the structural sheathing warm and dry. Oh yes, the fourth is that with your air/water barrier applied to warm & dry sheathing, you can skip the interior smart membrane entirely.
If your resistance to exterior insulation is a desire to minimize use of foam plastics, you should consider one of the non-foam insulation materials. These would include rigid Rockwool, wood insulating panels (ie Gutex), and some others. You could also cross-strap the existing 2x4 wall on the outside and fill that space with something low-energy and fluffy. With any of the exterior approaches, you can keep the existing sheathing and air-seal that layer either by taping the seams and holes, or by using a liquid or self-adhesive air/water barrier material.
And after that, back to your original questions. Both #1 and #2 would be durable solutions in your climate zone. #1 is difficult to build, as there is no way to easily attach the vapor retarder to the backside of the inner stud wall. With #2, you could put it on the interior side of the structural studs before building the inner wall. Other than that, the only real difference in the walls is the extra insulation space between the stud walls. That extra 3.5" will have a very long payback period. You probably know it already, but where possible, you want the studs in the inner and outer walls staggered to limit the thermal short.
Thank you. My resistance to exterior insulation is more the design of the roofline, which has very small overhangs on all but the two shortest and least weather affected walls. Adding even 2" of foam with the rain screen and siding will cut my overhang by half.
I'll be doing all the work myself and we are completely rearranging the layout of the interior, so gutting the inside is already in the plan.
Just to clarify, but would you recommend resheathing with plywood for only the 7" of insulation or would my existing OSB be safe without the exterior insulation? That's what I can't find an answer to.
I'm surprised you haven't received more replies by others, sorry about that.
Why are you planning to replacing the OSB and fiberglass? Its possible but not certain that wintertime vapor condensation led to damage. It may be in good condition and not require replacement. Rockwool mineral wool batts are superior to fiberglass, but I don’t believe its worth replacing fiberglass if the fiberglass is in good condition and was installed well. You might put your money into upgrades elsewhere. There is 20% or so framing factor thermal bridging in the stud wall, so upgrading the insulation R-value won’t benefit as much as adding extra insulation to the continuous insulation area between the double walls. If the existing fiberglass was installed well, filling all the airspaces in the stud bays, it should be okay.
I assume you have at least 6" clearance between the ground and the home's walls, to reduce the effects of ground moisture on the walls. Does the ground slope down and away from the walls in all directions? Has there been any problems with ice dams on the edge of the roof? If you find no rot in the OSB, it should be fine after you add a rain screen and R-Guard or other air-bulk water barrier, and upgrade to your well-designed higher R-value double wall. There are many references on this site that state that OSB is okay if protected from remaining wet, and that double stud walls do not result in sheathing rot if properly detailed and allowed to dry out when condensation does occur, despite worries about that issue.
Your double wall proposal #1 is similar to many double wall examples used by others successfully. Usually, contributors suggest that those who proposed wall #2, add insulation between the double walls to capitalize on all the work of building double walls by adding more R-value at lower cost or less labor. (Especially if you do decide on option #2, staggering the studs would be important.)
Detailing the interface between the foundation, windows, doors and your OSB or plywood air barrier are critical points where moisture intrusion are most likely. There's lots of information on this site and elsewhere on ideal window installation to avoid water intrusion, which I assume you are following given the time and thought you have invested in upgrading your home, and targeting Passive House standards.
It may be somewhat difficult to install smart vapor retarder-air barrier sheet stock on the exterior side of your new 2x4 interior double wall, although I can imagine a few ways of accomplishing it and insulating between the double walls. Its an ideal location keeping it away from the interior surface, subject to more holes from electrical receptacles, hanging pictures, etc.
Many on this site are happy to find people like yourself who take the effort to transform their home into a more energy-efficient and comfortable building. We appreciate your good work, and best of luck with your project!
When is the roof due for replacement? You could extend the overhangs at that point. I am with Robert in that you leave the current insulation in place if in good condition and add R-20 continuous exterior insulation. Being off the natural gas grid gives a large incentive to improve the thermal performance of your house. Passive House levels of performance may be a bit too high a bar. Superinsulation levels, R-30 wall, R-60 ceiling, ACH50 of near 1 will cut your energy bill drastically. Use your current annual energy usage as a guide for cost effective upgrades.
Your proposed remodel is a really big project - but it has the potential to really pay off over
a long period of time. Your existing wall likely has an R value of around 7 - why? because older homes with 2x4 walls insulated with fiberglass usually are about 25% wood and 75% fiberglass.
Thus, the R value calculation looks like this (4+3x11)/4=9.25 but there is wiring and plumbing
in it and the fiberglass installation is usually sloppy and then there are thousands of nails
and/or other fasteners holding on the sheetrock and the sheathing and the siding - every one
of which acts as a little heat sink, so, I apply a fudge factor and call it 7. NoWonder you "spend a ton on propane" in climate zone 7!
Attempting to nearly achieve passive house standards will likely mean you will want to approach R 40 in the walls, do something to the windows, reduce air infiltration and a few other things but lets talk about the walls. There is a better way to construct double walls -
The better way is to insert a layer of foam in the middle - in your case for your option #1
this would mean utilizing foil faced polyiso in the gap instead of fiberglass or mineral wool.
You were proposing a 3.5" gap - if you filled the stud wall on both sides with mineral wool
and the same in the gap your total R value for the wall would come out around 37. Using
polyiso raises it to around 43 (yes, I am still applying a fudge factor to get these numbers -
2x4 walls filled with mineral wool are figured at R 11 each and the polyiso at R 6 per inch).
Note that there is at least one brand of polyiso (Thermax) which claims no thermal degradation at low temperatures - using other brands would lead to an R value of around 40 in this wall at low temperatures (say negative 20 or colder).
Why would you choose this - There are some real good reasons! First, you don't need a vapor barrier because the foil faced polyiso is already the best vapor barrier money can buy. Water vapor can not pass through the wall in either direction and the foil face will remain above the dew point inside the wall under any conceivable conditions. Example: assume you are holding the inside temperature at 75 f and it's -35 f outside and snowing (so the relative humidity outside is 100%) the interior foil face of the polyiso will be 47 f - running the numbers on a
relative humidity calculator will show an interior relative humidity of about 2% under these conditions (which is absurd) - with people actually living in the house your relative humidity
will probably be up above 25% - checking a dew point calculator will show a dew point of 37 f
with an interior temp. of 75 f and humidity of 25% - This entire example is a little absurd because it's very seldom going to be anywhere near this cold with 100% humidity even in
northern WI. It just shows that there will never be a condensation problem with this wall.
Some other reasons - It's easy to build, it's no more expensive than all mineral wool, the two
stud walls protect the polyiso from fire, insects, and physical damage, you can adjust the
total R rating of the wall up or down by changing the thickness of the polyiso and it is also a near perfect air barrier (tape the seams and tape and/or caulk to the floor and ceiling).
Last I would not recommend less than 3.5 inches of polyiso in your climate because going with less would lower the surface temperature of the interior foil face in cold weather - going thicker has the opposite effect and would be even better - utilizing fiberglass batts instead
of mineral wool would have no effect other than to lower both the total R rating and cost.
GOOD LUCK!
One of the reasons that double walls do well, despite concerns about potential sheathing rot (due to water vapor condensation in wintertime), is that they dry out: They have a ventilated rainscreen on one side, and are able to dry out to the interior on the other side. Putting a vapor barrier between the double walls (e.g., foil-faced polyiso) stops inward drying of the sheathing. Adds risk to sheathing rot, in a wet climate especially.
Polyiso is a great product as exterior insulation, due to its high R-value per inch. I used it myself, but as exterior insulation. But for double walls, if you want more R-value, most people would suggest increasing the thickness of vapor open continuous insulation in the gap between the two wood frame walls in double wall construction. BrokeMedic was considering either mineral wool or dense packed cellulose, which are both good choices that would allow good water vapor management in double wall construction.
If BrokeMedic keeps the fiberglass insulated exterior wall, adds a 2x4 wall with mineral wool, with 3.5" dense-packed cellulose between the walls, the total R-value is about R-35. Adding the R-value of the sheathing, rainscreen exterior air space with cladding, interior drywall and interior air film, about R-38 total. With mineral wool between the walls, about R-40. Excellent choices. Windows, doors, and the exterior edge of the ceiling or other thermal bridging would become the items of highest concern for heat losses.
Robert Opaluch
I beg to differ! Double wall construction is usually considered valuable because of the ease
of adjusting the insulation thickness and therefor the total wall R value. The ability to dry is related to a large number of variables including but not limited to leakage of liquid water,
the adsorptive and absorptive qualities of the construction materials, temperature and
humidity, and air movement through the wall.
Placing an impermeable polyiso layer in the center of the wall affects none of those
variables except the movement of air through the wall and movement of air through walls
is undesirable. It carries heat and moisture with it. A wall built this way still has sheetrock on
one side and rainscreen on the other and will still dry both inside and out but moisture is prevented from transfer through the center. The thickness of the polyiso is then adjusted
to ensure that the temperature of the foil faces will always be above the dew point for all
expected combinations of temperature and humidity. This prevents condensation from
occurring in the fluffy insulation selected for the stud walls on either side.
Even considering cellulose (dense pack) for the gap in such a wall has become anathema
to me (I' m extremely aware of its unwarranted popularity). To understand why you need to
consider information which is not normally seen in publications like this. Take a look at
couple of the following:
https://insulationinstitute.org/wp-content/uploads/2016/02/BI460.pdf
https://www.youtube.com/watch?v=Xen_VWyDezY
The first of these is a study of drying potential of cellulose in walls. The second is a
seminar by Thorsten Chlupp on how he constructed his house in Fairbanks and problems and mistakes with it. I realize that neither of these is definitive proof of the undesirability of cellulose in walls but it's enough to activate suspicious minds (like mine). The first one shows that there are real problems with cellulose in walls drying after moisture gets in (regardless
of the moisture source). In the second article Thorsten found significant settling in his
cellulose filled walls after a year or two. This is suspicious because he went to extremes
trying to prevent it by blowing it in at 4 lbs/cubic-ft and then leaving the gap between the
walls open at the top and blowing an extra 2 feet of cellulose over the opening so it could
fall in if any settling occurred. It did not work! What we need is an extensive long term study
of both settling and effects of moisture on the R value of cellulose in walls - and by long
term I mean what happens over 10 years or more at varying humidity's. The manufactures
of the stuff have no incentive or a negative incentive to conduct or participate in such
Studys. I don't expect to see any within my lifetime.
Double wall construction is useful because traditional framers and general contractors tend to be more willing to build a second stud wall, and less inclined to deal with exterior insulation, battens, driving long screws through to find studs, somewhat squishy mineral wool exterior insulation board (which could result in wavy exterior surface if not careful)...and anything unfamiliar for that matter. Otherwise, exterior insulation (though a bit tricky to install in greater depths) has the advantage of keeping the ply/OSB/board sheathing above the dew point and not subject to water vapor condensation during winter. (OSB especially is more subject to damage from moisture.) Exterior insulation also has the advantage of providing some weather protection for any foundation insulation below, although that’s not relevant for this example.
You can vary the thickness and R-value for exterior insulation, or in stud bays by increasing stud depth (2x6 or 2x8), but you are correct, you can make more precise adjustments to total wall R-value by varying the gap between double walls if you are using cellulose or other blown-in insulation, and to some extent if you use various available thicknesses of polyiso board.
Building scientists considered double wall construction risky for sheathing rot, due to water vapor condensation on sheathing during winter. This was debated until testing was done. Results showed that double wall construction did fine, since sheathing got damp during winter but would dry out afterwards—which could include drying to the interior as well as drying via the rain screen. Recommendations for double walls (or any walls) include interior-facing smart vapor retarders and vapor open materials. (Eventually, water will get in there, one way or another.)
Would a vapor barrier (foil) inside a double wall risk insufficient drying potential (with no drying to the interior?) In a dry climate, I would guess not likely at all. In a wet climate like this example, it could be considered risky. Many considered double wall construction risky for sheathing rot due to water vapor condensation, before those test results showed the walls dried out okay during spring and summer. Look through the various articles here on GBA:
https://www.greenbuildingadvisor.com/?s=double+wall+moisture+OSB+condensation+drying
The problem with a water vapor barrier in the middle of the double wall is that water vapor cannot move from wet or damp sheathing to dry to the interior. You could use polyiso that is NOT foil-faced to allow some water vapor migration.
Here are some perm ratings:
Polyiso with foil facing, 1” thick 0.05 perms (blocks water vapor migration)
Polyiso without facing, 1” thick 26 perms
Mineral wool, 4” thick 29 perms
Cellulose insulation 4” thick, 29 perms
Fiberglass insulation, 4” thick, 29 perms
From https://www.greenbuildingadvisor.com/article/all-about-vapor-diffusion
But there’s another problem with polyiso between double walls. Previously I thought about polyiso for the continuous insulation layer between double walls, but abandoned the idea, partly due to construction difficulties. It would be very convenient to install 4’x8’ polyiso board before adding the inner stud wall. However, it gets in the way more than alternative insulation choices that can be added after plumbing, electrical, vents, … and building inspections. Think through the construction sequencing.
Cellulose will absorb moisture, then give off moisture when temps rise and relative humidity falls. So it acts as a buffer, which helps with the wintertime water vapor issue.
Its true that blown-in cellulose will settle. But BrokeMedic mentioned dense-packed (cellulose). Dense-packed cellulose won't settle (and provides a slightly higher R-value/inch). Lots of examples of dense packed cellulose being used in double stud walls on GBA. Most use dense packed cellulose for the stud walls as well as the inner continuous insulation layer. Seems to be the preferred material IF a contractor is available in the area that has the equipment and experience. (Not a DIY method like installing mineral wool batts.) But batts are fine too.
I would really love to hear from someone who has real experience with double walls built
foam in the center (in either wet or dry climates). Personally, I have only had experience with two houses built this way - hardly statistically significant.
The only people I am aware of who might have enough experience to
really influence the thinking are the firm "Passive Design Solutions" (A small Nova Scotia architecture design firm) Natalie Leonard, P. Eng., Founder.
Apparently, this group has designed and built a number of single family and multi-family
houses with this type of wall - I don't know what we could do to influence Natalie to write
an article for Green Building Advisor about double walls with polyiso (or other foam) centers - but it would make my day if she would!
Yes good idea, I've reached out to Natalie/Passive Design Solutions, since I'm interested in double-wall vs. exterior insulation in Nova Scotia and NE USA coast. In what locations or climate did you use foil-faced polyiso for the two houses you built this way?
Anyone else used foil-faced polyiso or other foam board inside double walls?? What was your climate?
It also would be very interesting if BrokeMedic installed some moisture sensors in his walls, particularly on walls facing northward, or any that receive the least sun year or the most precipitation year round. Maybe someone interested in evaluating double stud walls and moisture accumulation would help out and publish some data in the future. This sounds like a potentially challenging climate for double walls. BrokeMedic describes the climate as "far Northern WI climate zone 7, very wet and cold in winter, wet and 80s in the summer with little direct sun." A number of good choices are available, and local material and labor costs and availability also factor into these choices that BrokeMedic could make.