Clarification on old house insulation

Long time reader, first time questioner. Now I don’t mean to be trite, but I have not found the answer to this question after about 8 years of searching. Please only answer if you have experience or in depth knowledge.
So now on to the burning question, but first some back story.
So I currently live in Climate Zone 5. My home was finished in 1901 with some updates in the mid 50’s. I have done some minor improvements, replaced the windows with Energy Star rated double pane U-.30 whatever qualified for cash for caulkers program. I have also removed the window casings and used expanding foam in the open cavities and spaces behind the casings.
Now, I have some extra cash and some high energy bills. Best I can tell from the placards on the equipment the central air, with untaped and uninsulated ducts, and furnace are from the late 70’s early 80’s. They are pretty worn but going strong with regular maintenance. Maybe they are both 70-80% efficiency, and single stage. I added an attic access so that I could insulate the attic and make some storage space. Its a vented attic and low and behold when the roof was replaced in 2003, and the SLATE ROOF was removed they blew cellulose, 8-10″ (not enough but still score). After we dusted the plaster off, vacuumed out the cellulose, and installed the attic ladder I decided that since something was there, and I had bought unfaced fiberglass batts for a porch enclosing project. I threw those up there and covered a good deal of the surface area adding an extra R-30.
So that’s one thing to put on the back burner. I have insulation in the attic, it’s not enough to meet code, but its still more than most houses its age. So now that I have a thermal barrier, without an air barrier mind you, I think to myself, “Well, if the attic is kind of insulated and even though heat rises 2/3 of the surface area of my house are the walls, and they are very uninsulated, maybe I should focus there.
My goal has always been to create an as good as I can air sealed envelope. So, my plan was, for the last 4 years of planning, to blow cellulose or fiberglass into the walls. No one in my area does dense packing so I was going to give it the old college try and attempt to dense pack the walls as best i can myself. Then, after blowing insulation I was going to save some more money and put up 1.5″ EPS (R-5.3) for the cold, and then .5″ of foil faced polyiso (R-2.8 in cold/ 3.5 in heat) taped and staggered then reside the house with fiber cement lap.
Now I am second guessing myself. It dawned on me that most places that have horror stories of cellulose in old houses, don’t air seal the exterior. Cold air gets forced under the lap or the cold siding touching the cellulose and then the positive pressure of the forced air system pushes warmer air into the cellulose and viola condensate in/on the cellulose.
Now my question is this. What is the process I should follow? I have, as I see it, 3 ways to do this.
1) Seal the rim joists with expanding and rigid foam.
2) Blow cellulose or fiberglass into the wall as best I can
3) Put up the rigid foam taped and lapped
4) Reside the house
Or
1) Seal the rim joists with expanding and rigid foam.
2) Put up the rigid foam tapped and lapped
3) Reside the house
4) Blow insulation
or
Leave it be and deal with it.
Removing the siding is out of the question. $10,200 quote to remove the 3,600ft2 of assumed asbestos fiber cement siding.
Please, am I correct? Is there a better way to insulate my walls? I really don’t want to use foam, or tear down my plaster and lathe. I really want my walls insulated. If I put cellulose in my walls without being able to air seal the siding or seal out vapor on either side will my cellulose get wet? Can I get away with a heating season without having the exterior air sealed?
So many questions, so long of a story. Thank you
GBA Detail Library
A collection of one thousand construction details organized by climate and house part
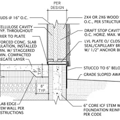
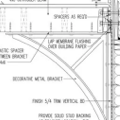
Replies
Azica,
It's too bad you removed R-37 cellulose from your attic and replaced it with R-30 fiberglass batts. That was a step backward.
Your suggested retrofit options are confusing.
1. When you mention installing rigid foam, are you thinking of installing the rigid foam on the interior side of your walls or the exterior side of your walls?
2. One of your suggested options is "Reside the house." Later, you tell us that "Removing the siding is out of the question." Please clarify.
Alright, I figured with a post that long and so late, I would need to make corrections or be more clear.
A) I added the fiberglass over the blown in the attic. My vacuuming comment was about the surprise I had when cutting out the plaster and it actually had something there. There was previously no access except for the wood gable vents to the attic.
2) The wall assembly would be as follows:
Exterior fiber cement lap siding
Air gap
2” of rigid foam taped and staggered
Asbestos fiber cement siding
Felt paper (it’s already there as a rain shield) from previous owners renovations
1x6 clapboard cladding
Blown cellulose or fiberglass in the wall cavities
Wood Lathe and plaster(no metal screening)
Latex interior paint
I hope that clears up any confusion.
Simplified:
Air infiltration is the primary cause, typically, in old leaky houses that get blown insulation for moisture problems in the insulation.. So without an air barrier to prevent infiltration I’m just asking for problems with moisture correct?
If that’s true it would be better for me to put the rigid foam on the exterior of the house to cover the asbestos and create an air/vapor barrier, and then blow the insulation correct?
Without an air barrier on the outside or inside I’m going to have wet cellulose in my walls after a single heating season correct?
The wall stackup matters. If there is plank sheathing with rosin paper or some sort of tar paper between the pre-existing siding and sheathing on the antique part of the house it's relatively safe to dense pack it with cellulose. The worst that happens in the first several years in that situation is that the paint on the siding fails. Take a very close look at the window flashing details before dense packing the cavities directly below windows though- bulk water intrusions due to improper or absent window flashing can be a real problem.
Dense packed cellullose in walls is sufficiently air tight to prevent it from becomeing soaked by wintertime moisture accumulation.
One inch foil faced Type-I EPS is pretty cheap- usually cheaper than half-inch polyiso. It's rated ~R3.9 @ 1" at a mean temp of 75F, but rises to R4.15 or more when the mean temp through the foam is 40F. A layer of 1" Type-II between an exterior 1" of foil-faced Type-I would perform at about R4.5 in winter, so you'd be looking at R8.65 With the half-inch polyiso/1.5" Type-II EPS solution the polyiso is good for about R2.5 in winter when it's on the coldest side of the assembly, and the 1.5" of EPS would perform at about R6.75 for R9.25 total before factoring in the facer & air gap.
That's only about an R0.6 difference, and not enough to MAKE a difference from either a peak load or dew point control.
To the first part of this reply. I plan to entirely reflash the windows with aluminum casing this fall/winter. I have not had any moisture problems yet, or leaks.
To The type of rigid foam, eps as you mentioned is cheap and effective across a temperature span. I chose the polyiso as the top layer because i wanted to lap the foam to create a better envelope.
I am a layman so the last part of your reply kind of confused me a bit as I had read that as long as the rigid foam in my climate had to be at least 27% of the wall rvalue to prevent condensation. So are you saying
A) That if it’s cheaper to just use EPS the r value difference is of no concern and it will prevent condensation.
Or
B) The r value isn’t high enough to prevent condensation either way
Or
C) Something else completely.
As I minor note the rigid foam types I had mentioned was the thinnest combination AND least expensive combination at the stores I have available.
I have other questions in response to the answers to this reply. So more to come.
I thought tar paper was only an effective water barrier/rain screen. It’s enough to slow wind drive?
Or are you saying 3.5lbs/ft3 is enough air barrier to not allow condensation?
Why will the paint peel if either of these measures is enough to prevent condensate in the walls or cladding?
Tar paper isn't a true air barrier, but it's a heluva lot more air retardent than plank sheathing. Air can still get around it's edges and seams and through the gaps in the plank sheathing, which is where the cellulose comes into play. Dense packed cellulose is very air retardent, but also not a true air barrier, enough that it's thermal efficiency isn't much robbed by air leakage around the tarpaper.
With your stackup dense packed cellulose is sufficiently air retardent that air leaks from the interior side won't saturate the cellulose over a winter in you climate. In climate zone 7 it might get wet, but also might not, depending on how air tight and vapor permeable the walls interior surfaces are. In zone 5 the sheathing & siding (and cellulose) will still take on some water, but not enough to do damage.
Before any exterior foam is added, with dense packed cellulose in the cavities the paint may peel on the original siding, assuming the siding hasn't been painted on the back side, since the siding & sheathing will now run colder/wetter. When it warms up outdoors the siding will be releasing it's wintertime moisture burden (still not enough moisture burden to damage the siding), and the vapor pressure behind the paint combined with the cupping/curl/ flexing from the uneven drying causes the paint to crack & fail. That's something of a worst case. There are many homes in zone 5 where it's tight enough already toward the interior, and there is sufficient roof overhang to also limit exterior moisture drives to where dense packing the walls won't cause the paint to fail. (It's hardly made a difference in my 1920s bungalow with 2' roof overhangs, also in zone 5.)
With full dimension 2x4s you get at most ~R15 in the cavities. With R8.7 on the exterior the total is R23.7, and (8.7/23.7=) 37% of that is exterior to the sheathing, which is a significant margin. It's fine to use the half inch polyiso too, but the assembly already beats IRC code minimum, and is moisture safe with the 1" Type-II + 1" foil faced Type-I.
Ahhh. Now that makes sense now that someone has explained it to me about why the paint will peel. Hopefully it’ll be a non issue since within a year I should be able to put up the foam and reside over the foam. Thank you so much for that explanation.
I’m feeling quite a bit more comfortable with starting with the cellulose and then adding the other things to the exterior.
Knowing that the peeling paint is from outdoor thermal physics rather than in wall thermal physics puts my mind at a lot more ease.
To be honest Bob Yapp’s website scared the crap out of me and made me think I was going to rot my house out
Ok so I have been marking my studs while using my FLIR (worlds most expensive stud finder). I cannot find a contractor or rental place that does dense packing.
What would be my best options for doing dense packing. I live in Northern WV if anyone has any references that aren’t listed in google or the phone book. The only places I have found are in Charleston and Wheeling. They won’t travel 15 miles outside their radius to do my job.
So I guess what I’m asking is, what are my options to dense pack. I can do the math and figure out how many lbs I need for each cavity. But if the blower machine won’t build the pressure what options do I have?
I don’t want anyone to roll their eyes, and think I’m just being one of “those guys”. But what about the people that have used wood shop dust collectors to remove cellulose, it seems pretty slick if not a little dog hole. Would something like that work if it was a last resort? I mean it’s kinda goofy but beats tearing down plaster to insulate right?
If nobody does dense-packing, "2-hole method" cellulose at ~2.5lbs+/- density still has pretty good air retardency, but may have to be "topped off" in about 15-20 years if the stud bays settle a bit.
It's possible to dense-pack to 3.2lbs+ with a single stage rental blower, but it'll take longer, and still requires the use of dense-packing hoses inserted into the holes. It's not rocket science, but there are lots of details to get right. A guy named Karg has published a lot on the topic on the web, if you want to figure out how to DIY it. eg:
http://www.karg.com/pdf/Presentations/Dense_Pack_Cellulose_Insulation.pdf
Thank you so much!