Choosing insulation.

I’m still trying to decide a few details of my walls. If i choose dense packed cellulose what r/ ” should I expect.? In searching this topic I’ve found values ranging from 3’0/” to 4.0/” Is there an agreed value supported by actual testing? If I should choose Roxul comfort bat I know the maximum r value but must degrade that to account for installation imperfections. Does anyone have any insight on how to estimate the degradation in a double stud wall with 3 layers of bat insulation?
GBA Detail Library
A collection of one thousand construction details organized by climate and house part
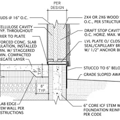
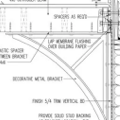
Replies
Jerry,
A good R-value for dense-packed cellulose insulation is R-3.7 per inch.
It's a fool's errand, in my opinion, to waste a lot of time trying to calculate the whole-wall R-value of a double-stud wall insulated with 3 layers of Roxul batts. Sharpening your pencil for this calculation is misplaced accuracy. Roxul comes in a variety of densities, but if you use a product that is rated at R-4 per inch, and you end up installing 12 inches, that would be R-48, minus the penalty imposed by the framing. It doesn't really matter if you call it an R-40 wall or an R-44 wall, in my opinion -- the difference in energy performance is trivial compared to many other factors (like occupant behavior and electrical appliances).
The R value of cellulose begins to fall with density after peaking at 2.7-2.8lbs density. Most dense pack starts at 3lbs. National Fiber ( a regional manufacturer near me) specs R3.7/inch @ 3.2lbs density. To legally make that claim in the US requires samples to be independently tested by a certified lab in accordance with ASTM C 518, the same requirements for R-value labeling on batts or rigid foam.
I've never read a spec for cellulose that hit R4/inch at any density (somebody is just rounding up, I s'pose) , but R3/inch would be a significantly under the real performance of anything currently being manufactured. Blown cellulose made from newsprint has been around for the better part of a century, didn't have a very refined manufacturing or installation process until about 1950, and didn't really take off until the late 1970s, but a lot of smaller low-quality vendors got in the game between 1975 and 1985- maybe some of them had R3/inch goods. The quality of the shred during manufacture as well as the control & quality of the blowers has improved quite a bit since 1920, or even since the 1950s. Most manufacturers will specify somewhere in their literature the settings on a particular blower model for achieving the labeled R-performance, but they need not be followed explicitly to get good results, and dense-packing will often require different air setting to achieve a particular density goal. (Better installers take sample cores and test density as part of the process.)
Like batts or foam, the real in-situ performance of blown insulation is ultimately in the hands of the installer.
At 4lbs density it's R value will be marginally lower, but it's air retardence will be measurably higher, which may trump the loss in R. Depending on the climate and how the house is used it may take 3.5lbs+ density to reliably eliminate settling in tall cavities over the long term, but it's always possible to "top off" any cavity that has settled over 2-3 decades, after which the settling rates would be even more miniscule. The settling issue is highly overstated IMHO. With cellulose settling is a function of density and seasonal humidity cycling, and with air tight interior/exterior skins and rainscreened siding even 2.8lb density could go decades without appreciably degraded performance in climates and conditions where less-tight houses would see an issue in only 10 years at that density.
With any batt solution it's difficult to state what the thermal-bypass penalty will be for the inevitable compressions and gaps, but when there are no obstructions to trim around and the framing spacing is pretty accurate, it can be pretty good.
What get with dense-packed blown fiber that you don't get with batts is a fair amount of air sealing during installation, since the material is blown into the cavity at high pressure until the blower stalls, the hose is pulled back a few inches to pack further until the blower stalls, repeat until the enclosed cavity is fill. The fiber being expelled along any air leak paths clogs & mostly-seals that air leak, and field experience indicated that seal though not perfect, does not degrade measurably over time.
But it's difficult to properly dense-pack large open cavities like you'd have in a double studwall- difficult, but not impossible. But even at less than perfectly uniform density most of the benefit of dense packing will be there if the installer is really going for the best possible installation.
The space heating load on any house with R40-ish walls will be dominated by the windows & doors, and/or the whole-house air leakage, which is why air-sealing becomes paramount for reaping the full benefit of the other performance features of the building envelope, and part of why the extreme 0.6ACH/50 became enshrined the PassiveHouse spec. (Though there were other reasons for the latter that make less sense to some of us.)
Any house with R40-ish walls needs at least some verification of air-tightness IMHO, even if a full calibrated blower door test (or multiple tests) isn't necessarily warranted. Defining the primary air barrier in the plan and INSPECTING the air tightness measures as the place comes together when errors can still be rectified avoids lower than expected performance surprises later. The best insulated wind tunnel in the world is still expensive to heat & cool.
I've convinced myself that the Roxul choice will give the highest thermal resistance with anything even close to a grade 1 installation. My chosen wall has 10 1/2" cavities and is framed with aligned 2x4's 24" OC and has 3/4" fiberboard exterior sheathing and 1/2" plywood on the outer face of the inner wall as the detailed air barrier and drywall. For this wall a near perfect inter stud layer (r 15) should be easily achieved. If I assume 2 perfect layers and concentrate the installation errors in one layer a simplified 1 dimensional analysis is possible. Using cellulose at r 3.7/" and Roxul comfort bat at r 15/3.5" and assuming a framing fraction of 15% it would take more than 40% missing insulation, in one wall, for the Roxul to be degraded to the thermal resistance of perfect cellulose. (R 37.6 perfect cellulose, r42.6 perfect Roxul)