Chimney chase question

I have a 90s era home with a framed chase on an exterior wall along a metal flue pipe. it’s in St. Louis, MO with hot/humid summers and cold winters. The fireplace is freezing in the winter when not in use because only the front (inside) wall of the chase has insulation.
I’m preparing to convert from a wood burning insert to a gas fireplace and have a chance to rectify some of the energy and comfort issues while the front wall of the chase is torn out.
Questions:
a.) Should I insulate the front wall of the chase or just the 3 exterior facing walls?
b.) I can only insulate up to the drywall top (firestop). How do I insulate the top? Should I sandwich mineral wool between the existing drywall firestop and another layer of drywall, respecting the 1″ clearance around the flue? I’d use high temp caulk to air seal the metal collar that the flue passes through on the original top.
c.) Where should the vapor barrier go? It’s currently behind the drywall on the insulated interior wall.
GBA Detail Library
A collection of one thousand construction details organized by climate and house part
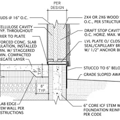
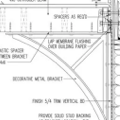
Replies
In order:
a.) Insulate and air seal just the exterior walls, which brings the flue chase fully inside of conditioned space.
b.) The 1" clearance to B-vent is only to combustibles. Rock wool is not combustible (less combustible than the B-vent itself) and thus needs no clearance, whereas paper-facers on gypsum board are combustible, thus the need for a flanged metal collar for sealing that annular ring. The top side air barrier can also be drywall (with clearance.)
c.) A kraft facer is not a true vapor barrier- it's a "smart" vapor retarder, about 0.5 perms when dry, but becomes fairly vapor open when the moisture content in the cavity reaches levels that support mold growth. In a zone 4 climate it's slightly better to put it on the interior side of the assembly when using kraft faced batts. In zone 4A there is no need or desire for a true vapor barrier such as 4-6 mil polyethylene, but air tightness matters. Vapor barriers create more problems than they solve in that climate. Making the interior side air barrier drywall painted with at least one coat of standard interior latex primer to bring it's vapor permeance down to about 5 perms or so is sufficient. That will allow the exterior sheathing to dry toward the interior if/when necessary. If it's a wood sheathed wall with wood, fiber cement or vinyl siding it's fine to go with "vapor barrier latex" primer (about 0.5 perms). But with masonry or stucco cladding it's better to leave it more vapor-open than that.
Since exterior chimneys don't have roof overhangs, the bulk water handling details at the top matter quite a lot, since any faults introducing bulk water into the insulated chimney chase has a lot of damage potential at the now colder-in-winter sheathing layer. Back ventilated cladding (such as vinyl, or an air gap to brick, etc) adds a lot to the resilience factor. What does the total stackup currently look like, and what sort of flashing details are there at the top?
Dana,
Thanks for the reply. You are spot on about chimney chases and the potential for bulk water issues. Mine was recently stripped down and rebuilt due to rot. It consists of 2x4 construction, plywood sheathing, fan-fold insulation, followed by non-insulated vinyl siding. The chimney top was the main culprit with an insufficient skirt. The new chase will be stainless steel with diagonal creases, a 3" skirt, a drip edge, and soldered/welded corners.
When the chase was rebuild, I asked my contractor to install Rockwool Comfort Batt up to the fire stop. He instead installed Rockwool's Safe and Sound product, which I understand to have no R value assigned by the manufacturer and isn't sold as thermal insulation. I've heard speculation that it approximates R11, but have no way of knowing. I do have the opportunity to replace it with Comfort Batt if that's truly helpful. Of course, neither of these products have a kraft facer. When I'm adding drywall to the inside walls, presume from your prior message that I should simply add a coat of interior latex primer and omit the polyethylene vapor barrier and kraft paper?
Many Thanks,
Paul
Safe'n'Sound is reportedly R11.7, per Rockwool Int'l's tech support, but being only 3" thick it's not even a full cavity fill, which makes it prone to convective thermal bypassing. See response #6 of this thread:
https://www.greenbuildingadvisor.com/question/safensound-r-0-vs-comfortbatt-r-15-for-interior-2x4-walls-only
Code minimum walls for US climate zones 3, 4, & 5 would be 2x6/R20, or 2x4/R13 + R5 continuous insulation. I suspect the fan-fold is only R1-1.5-ish, and with only R11.7 not fully filling the cavities it's not even close to meeting code. Since the chase will be one of the WARMEST parts of the house when the heater is in use, the lower-performance wall will negatively impact the overall thermal performance.
Swapping out the Safe'n'Sound for R15 batts and installing 1/2" foil faced polyiso (seams taped with aluminum HVAC tape) under the interior side drywall might just barely meet code, but with 3/4" polyiso it's for sure. Foil facers being a true vapor barriers (< 0.1 perms) the vapor retardency of the drywall layer becomes irrelevant, but is still needed as fire protection for the rigid foam. As long as the fan-fold on the exterior is perforated or at least not foil-faced, the sheathing can dry to the exterior under the vinyl siding.
Dana,
The fan-fold insulation is perforated.
I picked up some 1/2" polyiso for the side and 1" for the back of the chase. Because of the fireplace width requirements vs my chase width, I can only fit 1/2" polyiso on one of the sides and then cover with 1/2" or 5/8" drywall. Could I use 3/8" drywall to cover polyiso? If so, I can have 1/2" polyiso on both sides. I can't find anything on building code regarding which specific drywall thickness and type is required. If it matters, I'm installing a gas fireplace, not a wood burner.
Many Thanks,
Paul
>"Could I use 3/8" drywall to cover polyiso?"
It wouldn't meet the spec for a "thermal barrier" for fire safety with only 3/8" thick gypsum. But thermal barriers are only required between the foam and living space.
Since the chase isn't living space it only really needs an "ignition barrier", as long as there is still half-inch gypsum between the chase and the conditioned space, with no direct air communication between the chase and conditioned space. With those caveats, 3/8" over the foam on on the sides would qualify as an ignition barrier, so it should be fine.
See IRC 2018 section R316 on p77 (p102 in PDF pagination) :
https://www.ci.independence.mo.us/userdocs/ComDev/2018%20INTL%20RESIDENTIAL%20CODE.pdf
Excellent, I'll do that then.
For the floor of the chase, do you see any concerns with using two layers of 2" XPS rigid foam with a sheet of 3/4" plywood on top? The manufacturer doesn't impose any restrictions with respect to the fireplace sitting on combustibles. This would get the fireplace to the desired height and provide R20 for the floor of the cantilever. Do I need a vapor barrier?
The fireplace weighs about 400 pounds over a 50"x20" space, so I thought I'd use 25 psi foam. Assuming the weight is distributed roughly evenly over that space, it would be much, much less than 25 psi. Any reason to believe the foam wouldn't hold up to compression forces over the long term? It's pretty much impossible to get at once the drywall and finishes go up.
Thanks Again,
Paul
Any thoughts on insulating the floor of my chase from above? It's already insulated from below with XPS foam. In fact, it's similar to the diagram linked below except it's XPS instead of polyiso and doesn't have foam blocking to seal off the bay at the foundation wall. Sealing it at the foundation wall confuses me about where the thermal barrier lies.
https://terrylove.com/forums/index.php?threads/insulation-where-floor-joists-overhang-foundation.49767/page-2
If it's cantilevered out over open air it needs at least R19 total to meet IRC 2018 minimums in zone 4A St. Louis.
The thermal and pressure boundary of the house would include the foundation wall. The foundation should be insulated with a continuous R10 (or equivalent) to meet current IRC code unless there is R19 between the joists, but many homes have zero. Is it finished basement down there, a crawlspace?
Does air flow freely in the joist bays under the chase across the foundation to under the conditioned space floor (whether the floor is insulated or not?
The house has a conditioned basement and the fireplace chase cantilevers out over open air. The cantilever (underneath of the chase) was air sealed/insulated from inside the basement by installing 2" XPS foam on top of the plywood floor of the cantilever and on the sides and then foamed in at the seams. The cantilever doesn't have blocking at the foundation wall, so inside air can circulate through the cantilever bays.