Check my wall strategy?

We’re about to begin framing on a new house in zone 6A (Minneapolis). From months of reading and following posts here, I’ve devised what I think is a wall/insulation strategy that will work. Does this look right, or are there any tweaks that could make it:
a) perform better (within reason; we’re going after the “pretty good” model, not a Passivhaus)
b) more cost-effective
c) easier to build
The concept (inside to out):
– Drywall
– 2×6 stud wall
– Membrain or similar (6-mil poly if the inspector insists…sigh)
– 5.5″ blown fiberglass cavity insulation (BIBS) = R-23
– OSB sheathing
– 2.5″ XPS = R-12.5 (1″ + 1.5″ layers)
– Tyvek
– 1×4 vertical rainscreen furring strips screwed to studs
– Horizontal lap siding (fiber cement or smartside)
…for a total nominal R-value of ~35.5, with 35% on the exterior of the sheathing.
Thanks for any analysis and input.
GBA Detail Library
A collection of one thousand construction details organized by climate and house part
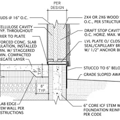
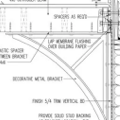
Replies
The usual definition of "Pretty Good House" has r6o ceilings, r40 walls, r20 below grade walls r10 basement slab. You are far short of r40, between r27 and r29.5 depending on how much wood is used in the 2x6 framing. Your wall is 9 1/4" thick from inside of siding to outside of drywall Can it be thicker? . With XPS you have very limited drying toward the exterior and interior poly would be a very bad idea. Without meticulous attention to the integrity of the air barrier (either the membrane or drywall) you risk moisture issues with the OSB. If you can accept a 2" thicker wall you can have true r40 (r45 mid cavity) with much less risk of moisture problems for an additional $1 to $2/sq ft of wall by using 2 2x4 walls spaced 3 1/2" apart with the OSB on the outer face of the inner wall using the same blown in insulation in both the inner wall cavities and the mid wall cavity + outer wall stud spaces. This alternative moves the air barrier to the OSB and eliminates any need for drywall sealing and simplifies the window and door flashing and installation as well. It will, also, have excellent drying potential both inward and outward This alternative eliminates the membrane and exploits the fact that OSB is a "smart" vapor retarder. It also eliminates the furring and rain screen gap substituting Greenguard DC14, a 1/4" thick fan fold XPS drainage plane over the house wrap.
Joshua,
Your wall will perform well.
Many builders prefer cellulose insulation to blown-in fiberglass, but either type of insulation can work well if it is conscientiously installed.
Many builders have concluded that they can get more bang for their buck (in terms of R-value) by building a double-stud wall rather than a 2x6 wall with exterior foam. But your approach has a major advantage over the double-stud approach: you end up with warm, dry wall sheathing instead of cold, damp wall sheathing.
Jerry,
Having read your replies to similar wall design questions in recent days, I am struck by your 'respect' for the difficulty of getting windows/doors installed correctly when dealing with wall designs that involve out-sulation. Although I have been following GBA pretty closely over the past several months, I have not noticed a similar level of caution from others. With all due respect, are you especially 'sensitive' to this aspect of such wall designs or is this a pretty big concern that others have just not highlighted or discussed much. I ask because I am considering wall designs using out-sulation and would appreciate any insight into construction difficulties that may be encountered.
Separately, a while back I proposed a few wall designs one of which consisted of double-stud walls with insulation in the 'gap'. A comment I received in response to that design had to do with the lack of a thermal break at the band joist and subfloor. It seems to me the design you have suggested above also suffers from this shortcoming. Is that correct?
Martin - It sounds to me that Joshua can't rule out the possibility that he will have to install poly inside the house. If that were the case, would your assessment that the wall would perform well still hold? Wouldn't there be a risk of moisture inside the wall not being to escape because of the foam outside and the poly inside?
Rob,
You're right; in my answer I didn't address the question of interior polyethylene -- and perhaps I should have.
I have addressed the topic in many articles, especially those that discuss exterior rigid foam. (Here's an example: Calculating the Minimum Thickness of Rigid Foam Sheathing.)
In case there is any uncertainty on this issue: If you want to install exterior rigid foam, your wall assembly has to be able to dry to the interior.
Ordinary latex paint is a perfectly adequate vapor retarder for this type of wall.
If your building inspector is grumpy, you can use vapor-retarder paint, a code-approved option.
If your building inspector is both grumpy and unwilling to read the code book, you can install MemBrain.
Under no circumstances should you install interior polyethylene on this type of wall.
Rob,
I am not sure what your wall assembly looked like, or the comment you received, but here is my take.
Double stud walls can thermally break the rim/band joist by having the outer wall directly on the foundation, and the inner wall sit upon the floor framing. Sometimes, this is actually a Larsen truss variation. Some call it Swedish platform framing.
Regardless of what you call it, or the exact details; this creates some space for insulation in front of the rim/band joist area. It can usually be adapted to fit most foundation types/thicknesses. To bring the R value in this area in line with the (thicker) wall assembly, you can either add some insulation in the joist bays, or bump up the R/inch with some rigid foam.
cheers
Jason,
Thanks for the information. My 'design' placed both walls on the floor framing which, compared to the configuration you describe, places it at a disadvantage. It still seems to me that even 'your' setup is at a disadvantage relative to out-sulation because you can have thermal bridging through the outer wall studs on into the band joist. But I guess if you catch it with the joist bay insulation then it is pretty close to the out-sulation case. Yes?
Thanks again.
Rob,
There can be a gap, between the outer wall studs, and the rim/band joist. The size of that gap will, of course, be limited by the thickness of your foundation. In other words, you can set the rim/band joist area back enough from the outer wall to get some R value. Part of the equation is which wall is the load bearing wall.
Outsulation has it's own pros and cons, as do double stud walls (and variations). That debate might be better left for another thread, but suffice to say that it needs to be assessed on a project by project basis, in my opinion.
cheers
Rob,
Over the years that I've been interested in and researching wall designs, I've seen many questions about framing, flashing and sealing windows with outsulation. I've seen many details proposed and none is as straight forward and "traditional as installing an "outie" in a double stud wall. The most common methods of dealing with exterior foam etc involve a substantial amount of thermal bridging with a plywood (typically 3/4") box around the window. With a double stud wall this can be eliminated or drastically reduced by making the "box" (which may still be needed to continue the air barrier) out of very thin material such as Thermoply.. To me it is an important offset of the labor necessary to build the double wall that is all too easily overlooked.
Regarding your second question: I did not address the details below the floor. The "band joist" region can be designed in many ways and have an effective r value of over 40 after fully accounting for the thermal properties (what some call bridging) of all the elements used. Jason mentions some options in post 5, there are many other as well. That cost optimization is another topic entirely as is the heat loss through the foundation.
Joshua,
Martin's response and mention of cold sheathing refers to a traditional double stud wall with the sheathing on the exterior. The wall I proposed moves the sheathing to the outer face of the inner wall where it will be even warmer and dryer than the rigid foam alternative!
Martin / Rob --
Yes, I'm definitely concerned with the issue of the poly. Trouble is we're in Minnesota where our codes delete the relevant sections of the IRC and add a universal requirement for 6-mil poly or equivalent. I'm waiting to hear back whether the inspector will allow us to go without poly on an exterior-foam assembly.
Jerry --
I had given a look to a double-stud assembly some time ago, but decided against it due to concerns with moisture at the exterior sheathing (some discussion in Building Science's BA-0903, which uses Minneapolis as one of it's modeling environments). I'm not familiar with the detail you describe placing the OSB on the interior wall; do you have a drawing? What provides rigidity to the exterior wall frame?
Another option I've considered is to sprayfoam the whole thing and omit the exterior foam, which would come at significant added cost, and obviously has more thermal bridging; but seems to eliminate the possible performance problems.
Joshua,
The general answer to "What provides rigidity to the exterior wall frame?" is shear planes at the top and bottom. These are small area thermal bridges necessary for structural integrity and need to be compensated by more insulation elsewhere.
I've attached the details of my planed cross section. In my case the main floor walls have an OSB layer as a top plate that ties the walls together and continues to become the top of the ceiling service cavity, At their base, the two walls are fully tied together by the top of the PWF basement wall and subfloor. In addition the type of cladding I'm using (thin brick adhered to metal substrates) has considerable racking strength although it's not needed. While I show mineral wool bats the high density blown in fiberglass, you've selected, is the same r/"
Joshua,
Here is a discussion of double wall construction with the sheathing on the inner wall:
https://www.greenbuildingadvisor.com/community/forum/general-questions/19942/sunrise-home
If you replaced the 2.5" of XPS with 3" of unfaced Type-II EPS (R12.6) you would have about 2x the drying capacity toward the exterior, and a much lower greenhouse gas foot print due to the differences in global warming potential of the blowing agents used (HFC134a @ ~1400x CO2 for XPS, compared to pentane @ only 7x CO2 for the EPS.)
Furthermore, after about 30 years the 3" of EPS will be outperforming the 2.5" of XPS, since XPS gradually loses performance as the HFC blowing agents leak out, doing their damage, whereas the pentane in EPS is mostly gone by the time it reaches the distributor's lot, and is not a factor in it's rated R value. After about 50-75 years the perforrmance of XPS & EPS are virtually identical at a given thickness & density, but the vapor permeance doesn't change much for either.
At 3" the vapor permeance of Type-II EPS is about the same as 1" of 1.5lb density XPS, and if you get stuck having to use 6mil poly instead of a smart vapor retarder this will be a significant difference in the resilience of the assembly.