Changes in Building Practices due to Changing Economic Factors

Maybe this is too broad/general for a good Q&A thread, but given the philosophical bent to the end of a tough year…..here goes:
It seems that residential building practices over the last few decades have been shaped by two broad economic factors: (1) consistently low mortgage/equipment/material financing rates, and (2) until recently, relatively low fuel, material and labor cost inflation. Over time these factors have led to bigger structures and practices and designs that did not always place efficient use of materials or labor as a paramount concern.
The recent spike in inflation has caused a stir, but continued low financing costs have blunted the impact for now. At some point interest rates will likely rise, and this will compound the sting of inflation. If and when this happens, I am wondering if the many experts on this site envision a big change to residential construction practices. When you add in the rising concern for imbedded energy/carbon in building materials, I am wondering if we will see a return to practices where materials are husbanded more carefully and designs pay closer attention to more frugal use of materials with less waste? I am wondering too whether the selection of materials will focus more on cost, availability and how well they adapt to less wasteful applications.
I am not expecting us to go back to the 1970’s (with 15% mortgage rates and constant double digit inflation)…. when I remember de-nailing 2x4s to reuse them and even collecting and straightening 16 penny nails around the job site (imagine young carpenters going around doing that now!) But I think there will be some changes-at first subtle, but later more pronounced….I was curious what you guys thought about this. Thanks.
GBA Detail Library
A collection of one thousand construction details organized by climate and house part
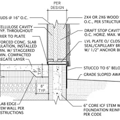
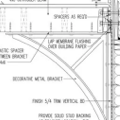
Replies
Nick,
I think the factors you've noted are why we'll continue to see a shift to more prefabrication of panelized and modular building systems. The industry is notoriously slow to adapt but the merits of off-site construction are too great to ignore considering the higher quality potential along with cost, time and material savings. If/when public perception shifts in favor I suspect demand will spike rapidly like it has for electric vehicles. That's just my idle speculation.
I think you are right. There are many advantages to this type of construction. One big disadvantage is that it separates much of the labor from the area where the housing is being built. One of the virtues of stick building is that for the most part the labor is local. In fact, given the disappearance of so many small manufacturing companies, it is one of the few locally made "things" left in so many areas. This is why I hope prefab/modular companies develop smaller localized factories to serve local or at least regional markets.
It is difficult for me to imagine gains through resource efficiency offsetting the economic and environmental costs of current and historical land use (policy).
Interesting. Do you have time to elaborate?
It is not uncommon in many markets, even ones with relatively inexpensive housing, for property to be purchased with the express purpose of tearing down the extant house and building the largest house that can be crammed onto the lot. There's an environmental cost to this, as well as the alternative, of urban sprawl.
When land carries that kind of premium, savings from resource efficiency are almost immaterial, if you'll forgive the expression. Put another way, it's the cost of land forcing resource efficiency to generate savings, not higher commodity prices. The economic imperative would still support moving the savings from resource efficiency to building a larger house.
^This
Bryan,
You make a good observation but this last statement reads somewhat ironic: "The economic imperative would still support moving the savings from resource efficiency to building a larger house."
The 'build-as-big-as-the-lot-allows' mentality follows from a faulty value proposition IMO. It's horribly common, but it only prevails because real estate professions have convinced (nearly) everyone that dollars per square foot is the key metric by which to measure value. The smart move, they would have us believe, is to spend not a single dime on what won't assess to greater real estate value. Tighter construction? Upgraded insulation and mechanicals? Zero value over the baseline. HERS rating? What's that?
It will take a lot more savvy homebuyers in the marketplace to shift the paradigm unfortunately.
I really don't think real estate professionals are that persuasive.
Yes, there are a lot of players -- houses don't get built if banks won't finance them, and banks won't finance them if they don't appraise. And taxes and insurance are a factor. But at the end of the day the thing that drives the whole industry is what sells, and that's ultimately determined by what a willing buyer offers to pay.
I would argue that cheap land leads to sprawl, expensive land leads to density, and that the environmental benefits of density far outweigh the environmental costs of inefficient use of materials.
I generally agree, but zoning ordinances in many (most?) places in the US limit density and are in part what makes land expensive.
Zoning ordinances are a large factor in sprawl, and zoning ordinances are largely driven by property tax considerations. When communities get their money from property taxes, they want big, pricey houses to maximize revenue. Property tax drives all sorts of terrible behaviors. If we could raise a similar amount of money in another way, that'd be a huge improvement, IMO.
With respect to Andrew's response above regarding property taxes. Property taxes are also often regressive, particularly against elderly who have stayed in a home for years only to see their property tax bills rise much faster than their income. This is a huge problem in much of suburban Northern New Jersey, where the property tax to income ratio is perhaps the highest in the country and got much higher with elimination of the SALT deductions.
@Nick
"With respect to Andrew's response above regarding property taxes. Property taxes are also often regressive, particularly against elderly who have stayed in a home for years only to see their property tax bills rise much faster than their income. This is a huge problem in much of suburban Northern New Jersey, where the property tax to income ratio is perhaps the highest in the country and got much higher with elimination of the SALT deductions."
- Believe it or not a lot of counties outside NJ exempt Seniors from having to pay some property tax such as School Taxes. NJ could do that but obviously non-seniors would face an even higher bill.
Interesting...A great example of this is Long Beach Island NJ where my dad bought a house in 1966 for $11,000. Today, very few houses under $1 Million and many tear downs-especially after Sandy.. Glad my dad never tore his down-we just rebuilt....
Interesting side note, one of my neighbors on LBI gave away a house and the new owner had it delivered by barge to his property...
Tough to say because there are a lot of moving parts:
Mortgage rates have been at historic lows for about a decade. This initially pulled demand from the future into the present. The Fed allegedly is going to begin curtailing the amount of MBS it purchases every month. So expect rates to rise a little but not much because the Fed is under pressure from the Legislature/Executive Branches of the USG to keep rates overall low. Low interest rates mean lower interest payments for the US Gov which has been spending like mad for decades.
Baby boomers are aging out.
Millennialss are aging-in.
Builders, having learned their lesson from 2008, have not been keen on expanding supply.
The mortgage interest rate deduction continues to act as a subsidy for the sector as a whole and special interests will make sure it remains as such.
Building materials have by in large remained unchanged with advancements limited to windows and mechanicals.
Edit: One other thing. Today the vast majority of homes are built by production builders who already operate at the razor edge of efficiency.
Thanks. Much to consider in your post...Personally, I have been astounded how long rates have remained low. I was sure they would be higher by now. What worries me is that low rates force so many to take on more risk for a little bit of yield. That is how bubbles grow.....
Agree.
Nick,
I look at houses as being primarily cultural artifacts. That's apparent from their shape and the spaces we expect to find in them. Before we go too far down the road of reusing or optimizing materiel use I think there are much larger gains to be made from re-thinking what we build.
A good example is the two car garage that has dominated the front of North American homes for the last few decades. Over time it has evolved so that almost no one uses it for parking vehicles, and instead it is a catchall for household storage. Developers around here have acknowledged that and now frequently use a door too narrow to admit all but the smallest cars. Rethinking this space would probably save more materials than most recycling efforts.
Yes I agree. I support a charity that builds clinics and schools in African villages, especially remote rural parts of Rwanda. When I was last there before COVID I wandered around the village and observed their small homes and how they were built and used. I also observed how they made building products (mostly palm fronds, hand sawn Eucalyptus lumber and clay/bricks) . Absolutely nothing was wasted and every inch of space carefully used. Their homes were indeed their biggest cultural artifact.
Yea I think this occurred because
No 1 - It is cheaper to build slab-on-grade and attach the garage to the house. The added benefit is smaller footprints which mean more lots per acre of land.
No 2 - Today vehicles are as big or bigger than what they were in the 1970s. This is why homes built in the 1960s to mid-1980s had larger garages. Oil crises forced people to buy smaller more fuel efficient cars so garages began to get smaller as well.
Deleted
This thread puts me in mind of an excellent article--in fact, former FHB editor Justin Fink called it "the most important story we've ever published"--by Kevin Ireton: "Why Don't We Build Better Houses?" I've attached it for y'all to read.
Great article thanks for sharing!
Thanks, a great article!
Perhaps less freedom of choice is the best way to a cleaner, healthier and wealthier world. It's sad but likely true. Who gets to decide what is what is the most concerning part.
On every jobsite there are constant discussions about substituting labor for materials and equipment for labor. It's pretty much all anyone talks about, all day. Materials are used inefficiently when the labor to use them efficiently costs more than the material savings that would result. Right now labor is quite expensive by the standards of recent decades.
Another consideration is the cost of disposal. By and large, dumpsters are ridiculously cheap. So it really is cheaper to throw a 2x4 with nails in the dumpster and pick a new one off of the pile than to pull the nails out.
The throw away attitude you highlight is so different than what is prevalent in the Third World. In rural Africa where my group works, no one would ever throw away something like a 2x4. Landfills do not exist. And it is not just that labor is cheap-building materials are hard to come by. They either have to be trucked in on miles of dirt paths (which we do with concrete for our buildings) or made by hard work with local labor. I will never forget watching two Rwandan sawyers cut a eucalyptus log (anyone who has worked with this knows it is hard) long ways into planks with a big old double handle saw. They did this all day long! It is no wonder the local woodworker was very careful with every inch of board he got! And the craftsmen were very serious about everything they make, from the maternity clinic we made out of concrete to the simple furniture sold at the local market...
Great post, brought back many memories from the 1960s/70s, especially on conservation of building materials such as 2x4s and nails, while that could have been in part due to family depression era experiences in Europe and US, my father did switch to a fuel efficient truck in 1973 (a Toyota pickup). I have long thought that modular is the way to go but around here, you say that word and, akin to piers, people think it's cheap. Architect Chris Pardo did a friend's house and he's done commercial modular too (e.g., Arrive Hotel, Palm Springs). With modular, there's more control of waste (think LEAN).
Some of the modular today is amazing! It would be great if se companies could build small factories in many localities so the labor remains close to where the demand for housing is great...
Pickle barrel idea. You would end up in the same place.
Agreed. Where possible, would be interesting to do local with at least some locally sourced materials including use of viable "wastes" from local industries, recycled, etc. Worked on a one-seed juniper/recycled polymer composite in NM. Sometimes "green" needs to consider utilization of non-green waste (capture?).
There's a house for sale near me, 12,000 square feet, 9 baths, asking $11,950,000. All modular. Built by BluePrint Robotics out of Maryland. So modular isn't necessarily cheap.
We're in a pickle barrel folks.
Modular or not makes little difference. It is very difficult to find value, quality and efficiency in any housing. Most importantly in a location a person would want to live long term makes the challenge nearly impossible considering the size of our population.
Outer space anyone? I think I see what's happening now.
James,
"Modular or not makes little difference. It is very difficult to find value, quality and efficiency in any housing."
Elaborate on that point, if you would.
Off-site modular and panelized construction are both proven ways to reduce waste, cost and risk. No weather delays, ideal working conditions and opportunity for quality control. Applies to all construction sectors as well, not just single-family homes. How does that not equate to more value? The resistance usually comes down to perception and design/construction process inertia more so than design limitation.
There isn't really much waste on commercial construction projects. Production residential builders, as previously mentioned, work very efficiently -- and they have to, since their buisness depends on it. I work mostly in the commerical world, and it's the same for us. Steel framing comes prefabricated, and basically bolts together. Concrete pours are planned based on the size of the trucks, to minimize material waste. Wasted materials is lost money, and a lot of effort goes into minimizing that waste. You'll always have some amount of waste, but it's not all that much. Even old crunched up concrete gets reused as aggregate in new pours!
I think people outside of the industry tend to think there is a lot of waste everywhere, but that's really not the case -- a LOT of effort goes into efficiency, which keeps costs down. The same goes for commerical energy efficiency -- there is a big push to save money, and that pushes upgraded lighting, variable frequency motor drives, all kinds of other things. I even bill my services on some projects where I charge no hourly rate, but I get a percentage of the energy costs I save my customer over the next 5 years or so. This is usually a win for the customer, since they only pay me what I can save them, and the amount they pay me is always less than the total amount I save them. A huge amount of my work goes into optimizing energy efficiency.
In the residential world, there is probably more that can be done for energy efficiency, since residential projects -- especially older structures -- tend to not have specilized consultants going over everything to optimize things as much as possible.
I'm totally against mandating living spaces, housing, and things like that. Doing that makes life miseral for people. The Soviets did that, and while there was some gain in efficiency, the cost in reduced quality of life more than offset those savings, with predictable results that are now part of history. Packing people together tends to cause problems. The sole goal here can't be "greeness", or "efficiency", there has to be some regard for the wellbeing of the people living there, and this can't be brushed aside by saying things like "it's greener, so we have to". These are not simple problems.
Bill
Bill --
A counterpoint: I got a friend who builds custom houses to share his budget for a recent build. One line item stuck out to me, construction waste disposal: ten dumpsters. This was separate from pre-construction demolition which was a separate line item.
To put that in perspective, about a year ago I took down a house and it was ten dumpsters. So as a rough approximation as much gets thrown away as goes into building a house.
Now you can argue about what constitutes waste. Is it waste to only use a quarter of a sheet of drywall and throw away the rest, if that results in fewer seams, which results in a better outcome at lower cost for the customer?
To your Soviet comparison, I learned long ago that capitalism doesn't value efficiency, it values productivity. Sometimes productivity and efficiency overlap, and sometimes they don't.
Efficiency is a component of productivity. Always has been. The economic system in the US has for the most part always been capitalistic with a heavy dose of political cronyism. It was never capitalism.
If you're demoing a house, then yeah, you're going to have a lot going in the trash. That's unfortunate too, since there ARE things that can get reused. In the commerical world, there are companies that specialize in this, and they'll come into a property prior to demolition and remove everything salvagable (this usually means valves, electrical switchgear, pumps, and larger pipe and wire). Steel from structures tends to be mostly recycled.
Maybe the residential guys are behind the commercial guys here? Maybe not as much residential materials can be reused (I can see that with wood framing)? I had been thinking new structures, which should have less going in the trash, since there isn't an existing structure to remove first. I wouldn't call the material demoed from an old structure "waste" the same way I'd call stuff from a new project "waste". Waste here would be stuff that had been new, but didn't get used in the final product, so things like cutoff excess, etc. Old material from a demoed structure isn't really waste, although I agree some of that material is wasted when sent to the trash.
Capitalism does value efficiency, that's just not the only thing. No system is going to be perfect. The more socialistic systems tend to end up producing a lot more waste, it's just done in different ways, and there is a bigger incentive for those running the show to hide the waste. Anytime people are running something, you're going to have problems, since there are the less useful parts of human nature that come out and mess with things.
Bill
Bill --
You're missing my point. His budget was ten dumpsters for the construction phase. That's in addition to demo.
I would agree that residential guys are behind commercial. Commercial is more expensive across the board, and pays better. Residential is the minor leagues by comparison.
I agree with both, commercial being more sophisticated as generally more $ / time can be "saved". On residential, I had one month with 4,000 kWh consumed in a 2,100 sq ft house because an electric resistance heater was used with windows open (in January) to allow for drying/degassing of painted trim/doors. HVAC was rightly concerned with activating the heat pump/air handlers before interior construction, sanding, painting, etc., was finished. Many moving pieces and factors, especially when the city makes you do sidewalks, road work/paving before issuing an occupancy permit and with the asphalt plant closed for the winter. The city talks "green" (e.g., requires a HERS rating) but maybe the city should be rated too (as to how they regulate/delay things in a manner that greatly increases waste - they seem to not hesitate to make decisions that increase costs and time).
Ten big rolloffs seems like an awful lot for the new construction phase of a house to me! Admittedly my experience is mostly in the commercial world. The last decent size (~50,000 sq ft) project I did I think we used two or three large rolloffs, and most of that was for old drywall that we removed to reconfigure some walls. Old raised floor (this was a datacenter) was scrapped, I had my guys seperate out the metal understructure for salvage. We get PAID for the old metal, since it's worth scrap value. Even my electricians save all their cut wire ends, which they scrap at the end of the month to buy their crew a big pizze lunch or two. I'd love to find a way to scrap (BTW, in my world, "scrap" means it goes to a salvage company for recycling, instead of to the trash) the old drywall too, but as far as I know, no one will take that for salvage value. We do scrap out all the old steel studs though. I've even by able to scrap old floor tiles in the past sometimes.
It surprises me the residential guys don't do this more. On my projects, we always figure out what we can scrap out and about how much money that will bring in to offset the new materials. We usually get thousands or tens of thousands of dollars this way. I also use a lot of used/refurbished equipement to save my customers money.
PBP: I completely agree about the issues with the city. I've run into that too with energy code issues. There can be a lot of counterproductive regulations here. I run into that sometimes when using used equipment, since they claim it doesn't meet current efficiency standards. The thing is, we check all that (electrical costs are our biggest operating cost by far), so it's all been factored in, with the used equipment being as good or better than new in our specific operating enviornment.
Bill
One of the few benefits of high materials cost is that the recycled/reclaimed materials business becomes more interesting economically. People who know what they are doing can do very well. New York City probably has more 19th/early 20th Century high quality wood (harvested from old growth forests) imbedded in it than virtually anywhere in the world (except perhaps London), much of it in the form of long, heavy beams and joists. Every time an old building comes down or is renovated this stuff should be saved. Also, much of this wood dates back to trees that started growing before the industrial revolution took hold here and scientists are very interested in studying the rings in this wood to find clues to climate change over the last 4-500 years.